T. Patrício, M. Domingos, A. Gloria, U. D'Amora, J.F. Coelho and P.J. Bártolo
The main purpose of this research work is to study the effect of poly lactic acid (PLA) addition into poly (e-caprolactone) (PCL) matrices, as well the influence of the mixing…
Abstract
Purpose
The main purpose of this research work is to study the effect of poly lactic acid (PLA) addition into poly (e-caprolactone) (PCL) matrices, as well the influence of the mixing process on the morphological, thermal, chemical, mechanical and biological performance of the 3D constructs produced with a novel biomanufacturing device (BioCell Printing).
Design/methodology/approach
Two mixing processes are used to prepare PCL/PLA blends, namely melt blending and solvent casting. PCL and PCL/PLA scaffolds are produced via BioCell Printing using a 300-μm nozzle, 0/90° lay down pattern and 350-μm pore size. Several techniques such as scanning electron microscopy (SEM), simultaneous thermal analyzer (STA), nuclear magnetic resonance (NMR), static compression analysis and Alamar BlueTM are used to evaluate scaffold's morphological, thermal, chemical, mechanical and biological properties.
Findings
Results show that the addition of PLA to PCL scaffolds strongly improves the biomechanical performance of the constructs. Additionally, polymer blends obtained by solvent casting present better mechanical and biological properties, compared to blends prepared by melt blending.
Originality/value
This paper undertakes a detailed study on the effect of the mixing process on the biomechanical properties of PCL/PLA scaffolds. Results will enable to prepare customized PCL/PLA scaffolds for tissue engineering applications with improved biological and mechanical properties, compared to PCL scaffolds alone. Additionally, the accuracy and reproducibility of by the BioCell Printing enables to modulate the micro/macro architecture of the scaffolds enhancing tissue regeneration.
Details
Keywords
Abstract
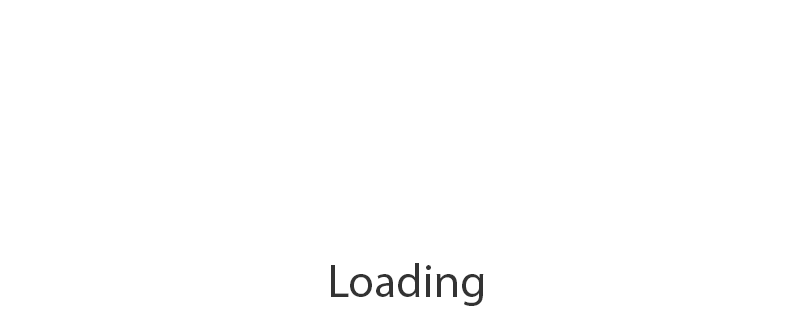
Purpose
Additive manufacturing (AM) or solid freeform fabrication (SFF) technique is extensively used to produce intrinsic 3D structures with high accuracy. Its significant contributions in the field of tissue engineering (TE) have significantly increased in the recent years. TE is used to regenerate or repair impaired tissues which are caused by trauma, disease and injury in human body. There are a number of novel materials such as polymers, ceramics and composites, which possess immense potential for production of scaffolds. However, the major challenge is in developing those bioactive and patient-specific scaffolds, which have a required controlled design like pore architecture with good interconnectivity, optimized porosity and microstructure. Such design not only supports cell proliferation but also promotes good adhesion and differentiation. However, the traditional techniques fail to fulfill all the required specific properties in tissue scaffold. The purpose of this study is to report the review on AM techniques for the fabrication of TE scaffolds.
Design/methodology/approach
The present review paper provides a detailed analysis of the widely used AM techniques to construct tissue scaffolds using stereolithography (SLA), selective laser sintering (SLS), fused deposition modeling (FDM), binder jetting (BJ) and advanced or hybrid additive manufacturing methods.
Findings
Subsequently, this study also focuses on understanding the concepts of TE scaffolds and their characteristics, working principle of scaffolds fabrication process. Besides this, mechanical properties, characteristics of microstructure, in vitro and in vivo analysis of the fabricated scaffolds have also been discussed in detail.
Originality/value
The review paper highlights the way forward in the area of additive manufacturing applications in TE field by following a systematic review methodology.
Details
Keywords
Hongbin Li, Taiyong Wang, Jian Sun and Zhiqiang Yu
The purpose of this paper is to study the effects of these major parameters, including layer thickness, deposition velocity and infill rate, on product’s mechanical properties and…
Abstract
Purpose
The purpose of this paper is to study the effects of these major parameters, including layer thickness, deposition velocity and infill rate, on product’s mechanical properties and explore the quantitative relationship between these key parameters and tensile strength of the part.
Design/methodology/approach
A VHX-1000 super-high magnification lens zoom three-dimensional (3D) microscope is utilized to observe the bonding degree between filaments. A temperature sensor is embedded into the platform to collect the temperature of the specimen under different parameters and the bilinear elastic-softening cohesive zone model is used to analyze the maximum stress that the part can withstand under different interface bonding states.
Findings
The tensile strength is closely related to interface bonding state, which is determined by heat transition. The experimental results indicate that layer thickness plays the predominant role in affecting bonding strength, followed by deposition velocity and the effect of infill rate is the weakest. The numerical analysis results of the tensile strength predict models show a good coincidence with experimental data under the elastic and elastic-softened interface states, which demonstrates that the tensile strength model can predict the tensile strength exactly and also reveals the work mechanism of these parameters on tensile strength quantitatively.
Originality/value
The paper establishes the quantitative relationship between main parameters including layer thickness, infill rate and deposition velocity and tensile strength for the first time. The numerically analyzed results of the tensile strength predict model show a good agreement with the experimental result, which demonstrates the effectiveness of this predict model. It also reveals the work mechanism of the parameters on tensile strength quantitatively for the first time.
Details
Keywords
Ida Papallo, Domenico Solari, Ilaria Onofrio, Lorenzo Ugga, Renato Cuocolo, Massimo Martorelli, Teresa Russo, Ilaria Bove, Luigi Maria Cavallo and Antonio Gloria
This study aims to integrate design methods and additive manufacturing with the use of a thermoplastic elastomer certified for medical use and reverse engineering towards a new…
Abstract
Purpose
This study aims to integrate design methods and additive manufacturing with the use of a thermoplastic elastomer certified for medical use and reverse engineering towards a new concept of a customized buttress model with optimized features for the reconstruction of the osteo-dural opening after endoscopic endonasal transtuberculum-transplanum approach.
Design/methodology/approach
Additive manufacturing allows making of cost-effective and useable devices with tailored properties for biomedical applications. The endoscopic endonasal approach to the suprasellar area enables the management of different intradural tumours, and the craniectomy at the skull base is generally wide and irregular. Defining an optimal strategy for osteodural defect closure at the preoperative stage represents a significant challenge.
Findings
Using the results obtained from a computed tomography analysis, skull base defects were designed to plan the surgical approach. Several concepts of customized buttress models were first built up, initially focusing on thin, flexible edges characterized by different thicknesses. Finite element analyses and design optimization allowed us to achieve the optimal design solution with improved compliance/flexibility for easy intranasal manoeuvrability, maintaining an adequate mechanical stability. As the thickness of the edges decreased, an increase of strain energy values was found (i.e. 1.2 mJ – Model A, 1.7 mJ – Model B, 2.3 mJ – Model C, 4.3 mJ – Model D). However, a further optimization (Model E) led to a significant increase of the compliance (strain energy of 14.1 mJ).
Originality/value
The results obtained from clinical evaluations demonstrated the feasibility of the proposed technical solutions, improving surgery effectiveness.
Details
Keywords
Prashant Anerao, Atul Kulkarni and Yashwant Munde
This paper aims to investigate the current state of biocomposites used in fused deposition modelling (FDM) with a focus on their mechanical characteristics.
Abstract
Purpose
This paper aims to investigate the current state of biocomposites used in fused deposition modelling (FDM) with a focus on their mechanical characteristics.
Design/methodology/approach
The study presents a variety of biocomposite materials that have been used in filaments for 3D printing by different researchers. The process of making filaments is then described, followed by a discussion of the process parameters associated with the FDM.
Findings
To achieve better mechanical properties of 3D-printed parts, it is essential to optimize the process parameters of FDM while considering the characteristics of the biocomposite material. Polylactic acid is considered the most promising matrix material due to its biodegradability and lower cost. Moreover, the use of natural fibres like hemp, flax and sugarcane bagasse as reinforcement to the polymer in FDM filaments improves the mechanical performance of printed parts.
Originality/value
The paper discusses the influence of critical process parameters of FDM like raster angle, layer thickness, infill density, infill pattern and extruder temperature on the mechanical properties of 3D-printed biocomposite.
Details
Keywords
Saahil V. Mehendale, Liliana F. Mellor, Michael A. Taylor, Elizabeth G. Loboa and Rohan A. Shirwaiker
This study aims to investigate the effect of three-dimensional (3D)- bioplotted polycaprolactone (PCL) scaffold geometry on the biological and mechanical characteristics of human…
Abstract
Purpose
This study aims to investigate the effect of three-dimensional (3D)- bioplotted polycaprolactone (PCL) scaffold geometry on the biological and mechanical characteristics of human adipose-derived stem cell (hASC) seeded constructs.
Design/methodology/approach
Four 3D-bioplotted scaffold disc designs (Ø14.5 × 2 mm) with two levels of strand–pore feature sizes and two strand laydown patterns (0°/90° or 0°/120°/240°) were evaluated for hASC viability, proliferation and construct compressive stiffness after 14 days of in vitro cell culture.
Findings
Scaffolds with the highest porosity (smaller strand–pore size in 0°/120°/240°) yielded the highest hASC proliferation and viability. Further testing of this design in a 6-mm thick configuration showed that cells were able to penetrate and proliferate throughout the scaffold thickness. The design with the lowest porosity (larger strand–pore size in 0°/90°) had the highest compression modulus after 14 days of culture, but resulted in the lowest hASC viability. The strand laydown pattern by itself did not influence the compression modulus of scaffolds. The 14-day cell culture also did not cause significant changes in compressive properties in any of the four designs.
Originality/value
hASC hold great potential for musculoskeletal tissue engineering applications because of their relative ease of harvest, abundance and differentiation abilities. This study reports on the effects of 3D-bioplotted scaffold geometry on mechanical and biological characteristics of hASC-seeded PCL constructs. The results provide the basis for future studies which will use this optimal scaffold design to develop constructs for hASC-based osteochondral tissue engineering applications.
Details
Keywords
Li Wu, Xinxin Li, Tianmin Guan, Yong Chen and Chunwei Qi
The 3 D bioprinting technology is used to prepare the tissue engineering scaffold with precise structures for the cell proliferation and differentiation.
Abstract
Purpose
The 3 D bioprinting technology is used to prepare the tissue engineering scaffold with precise structures for the cell proliferation and differentiation.
Design/methodology/approach
According to the characteristics of the ideal tissue engineering scaffold, the microstructural design of the tissue engineering scaffold is carried out. The bioprinter is used to fabricate the tissue engineering scaffold with different structures and spacing sizes. Finally, the scaffold with good connectivity is achieved and used to cell PC12 culture.
Findings
The results show that the pore structure with the line spacing of 1 mm was the best for cell culture, and the survival rate of the inoculated cells PC12 is as high as 90%. The influence of the pore shape on the cell survival is not evidence.
Originality/value
This study shows that tissue engineering scaffolds prepared by 3 D bioprinting have graded structure for three-dimensional cell culture, which lays the foundation for the later detection of drug resistance.
Details
Keywords
Daniel Aragón-Lozano, Mariana S. Flores-Jimenez, Alejandro Garcia-Gonzalez, Yocanxóchitl Perfecto-Avalos, Fabian Rho-Mas, Ricardo García-Gamboa, Rita Q. Fuentes-Aguilar and Isaac Chairez
This study aims to develop and validate an integrated extrusion bioprinting system that produces planar and non-planar scaffolds with embedded living material (bacteria or…
Abstract
Purpose
This study aims to develop and validate an integrated extrusion bioprinting system that produces planar and non-planar scaffolds with embedded living material (bacteria or mammalian cells), overcoming the limitation of traditional extrusion bioprinting, where the material is deposited and cultured in planar layers.
Design/methodology/approach
The bioprinting device was constructed by modifying a fused deposition modelling 3D printer, adapting the extrusion holder for hydrogel-bioinks, going from an 8-bit architecture to a 32-bit one andad hoc updating the firmware, increasing the processing capacity and enabling accurate deposition of material. The device performance was assessed in hydrogel 3D planar and non-planar extrusion, considering different radius of curvature to form porous scaffolds, evaluating their ability to retain the designed curved geometry and the cell viability maintaining in bacterial and mammalian cells bioinks.
Findings
The viability (up to 99%) and growth of bacteria and mammalian cells embedded in the scaffolds was confirmed by confocal microscopy. The suggested bioprinting platform and procedure integrates an efficient strategy for producing hydrogel-based scaffolds, obtaining 98% resolution in planar deposition. For non-planar scaffolds, it was found that they are capable of maintaining the designed curvature even after being removed from the support, with an 88% of resolution.
Originality/value
It is reported a novel and advanced 3D extrusion bioprinting strategy for producing curved and complex scaffolds, preserving resolution and sterile conditions, introducing in addition a methodology for direct design and generation of a g-code with continuous and smooth paths, pioneering on the 3D bioprinting of bacterial bioinks.
Details
Keywords
Adib Bin Rashid, Abu Saleh Md. Nakib Uddin, Fahima Akter Azrin, Khondker Safin Kaosar Saad and Md Enamul Hoque
The main objective of this paper is to illustrate an analytical view of different methods of 3D bioprinting, variations, formulations and characteristics of biomaterials. This…
Abstract
Purpose
The main objective of this paper is to illustrate an analytical view of different methods of 3D bioprinting, variations, formulations and characteristics of biomaterials. This review also aims to discover all the areas of applications and scopes of further improvement of 3D bioprinters in this era of the Fourth Industrial Revolution.
Design/methodology/approach
This paper reviewed a number of papers that carried evaluations of different 3D bioprinting methods with different biomaterials, using different pumps to print 3D scaffolds, living cells, tissue and organs. All the papers and articles are collected from different journals and conference papers from 2014 to 2022.
Findings
This paper briefly explains how the concept of a 3D bioprinter was developed from a 3D printer and how it affects the biomedical field and helps to recover the lack of organ donors. It also gives a clear explanation of three basic processes and different strategies of these processes and the criteria of biomaterial selection. This paper gives insights into how 3D bioprinters can be assisted with machine learning to increase their scope of application.
Research limitations/implications
The chosen research approach may limit the generalizability of the research findings. As a result, researchers are encouraged to test the proposed hypotheses further.
Practical implications
This paper includes implications for developing 3D bioprinters, developing biomaterials and increasing the printability of 3D bioprinters.
Originality/value
This paper addresses an identified need by investigating how to enable 3D bioprinting performance.
Details
Keywords
Taylor Davis, Tracy W. Nelson and Nathan B. Crane
dding dopants to a powder bed could be a cost-effective method for spatially varying the material properties in laser powder bed fusion (LPBF) or for evaluating new materials and…
Abstract
Purpose
dding dopants to a powder bed could be a cost-effective method for spatially varying the material properties in laser powder bed fusion (LPBF) or for evaluating new materials and processing relationships. However, these additions may impact the selection of processing parameters. Furthermore, these impacts may be different when depositing nanoparticles into the powder bed than when the same composition is incorporated into the powder particles as by ball milling of powders or mixing similarly sized powders. This study aims to measure the changes in the single bead characteristics with laser power, laser scan speed, laser spot size and quantity of zirconia nanoparticle dopant added to SS 316 L powder.
Design/methodology/approach
A zirconia slurry was inkjet-printed into a single layer of 316 SS powder and dried. Single bead experiments were conducted on the composite powder. The line type (continuous vs balling) and the melt pool geometry were compared at various levels of zirconia doping.
Findings
The balling regime expands dramatically with the zirconia dopant to both higher and lower energy density values indicating the presence of multiple physical mechanisms that influence the resulting melt track morphology. However, the energy density required for continuous tracks was not impacted as significantly by zirconia addition. These results suggest that the addition of dopants may alter the process parameter ranges suitable for the fabrication of high-quality parts.
Originality/value
This work provides new insight into the potential impact of material doping on the ranges of energy density values that form continuous lines in single bead tests. It also illustrates a potential method for spatially varying material composition for process development or even part optimization in powder bed fusion without producing a mixed powder that cannot be recycled.