Tessa Jane Gordelier, Philipp Rudolf Thies, Louis Turner and Lars Johanning
Additive manufacturing or “3D printing” is a rapidly expanding sector and is moving from a prototyping service to a manufacturing service in its own right. With a significant…
Abstract
Purpose
Additive manufacturing or “3D printing” is a rapidly expanding sector and is moving from a prototyping service to a manufacturing service in its own right. With a significant increase in sales, fused deposition modelling (FDM) printers are now the most prevalent 3D printer on the market. The increase in commercial manufacturing necessitates an improved understanding of how to optimise the FDM printing process for various product mechanical properties. This paper aims to identify optimum print parameters for the FDM process to achieve maximum tensile strength through a review of recent studies in this field.
Design/methodology/approach
The effect of the governing printing parameters on the tensile strength of printed samples will be considered, including material selection, print orientation, raster angle, air gap and layer height.
Findings
The key findings include material recommendations, such as the use of emerging print materials like polyether-ether-ketone (PEEK), to produce samples with tensile strength over 200 per cent that of conventional materials such as acrylonitrile butadiene styrene (ABS). Amongst other parameters, it is shown that printing in the “upright” orientation should be avoided (samples can be up to 50 per cent weaker in this orientation) and air gap and raster width should be concurrently optimised to ensure good “inter-raster” bonding. The optimal choice of raster angle depends on print material; in ABS for example, selecting a 0° raster angle over a 90° angle can increase tensile strength by up to 100 per cent.
Originality/value
The paper conclusions provide researchers and practitioners with an up-to-date, single point reference, highlighting a series of robust recommendations to optimise the tensile strength of FDM-printed samples. Improving the mechanical performance of FDM-printed samples will support the continued growth of this technology as a viable production technique.
Details
Keywords
Abstract
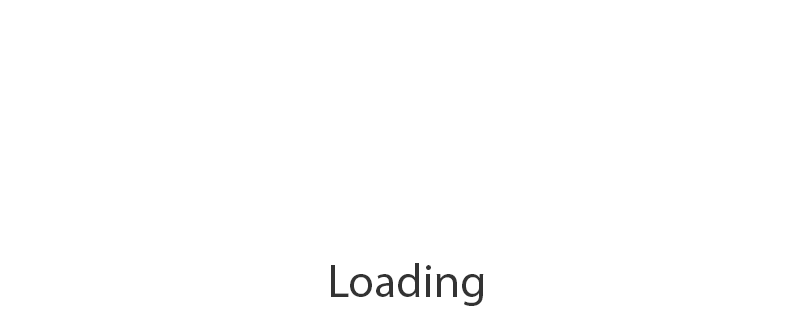
Purpose
Additive manufacturing (AM) or solid freeform fabrication (SFF) technique is extensively used to produce intrinsic 3D structures with high accuracy. Its significant contributions in the field of tissue engineering (TE) have significantly increased in the recent years. TE is used to regenerate or repair impaired tissues which are caused by trauma, disease and injury in human body. There are a number of novel materials such as polymers, ceramics and composites, which possess immense potential for production of scaffolds. However, the major challenge is in developing those bioactive and patient-specific scaffolds, which have a required controlled design like pore architecture with good interconnectivity, optimized porosity and microstructure. Such design not only supports cell proliferation but also promotes good adhesion and differentiation. However, the traditional techniques fail to fulfill all the required specific properties in tissue scaffold. The purpose of this study is to report the review on AM techniques for the fabrication of TE scaffolds.
Design/methodology/approach
The present review paper provides a detailed analysis of the widely used AM techniques to construct tissue scaffolds using stereolithography (SLA), selective laser sintering (SLS), fused deposition modeling (FDM), binder jetting (BJ) and advanced or hybrid additive manufacturing methods.
Findings
Subsequently, this study also focuses on understanding the concepts of TE scaffolds and their characteristics, working principle of scaffolds fabrication process. Besides this, mechanical properties, characteristics of microstructure, in vitro and in vivo analysis of the fabricated scaffolds have also been discussed in detail.
Originality/value
The review paper highlights the way forward in the area of additive manufacturing applications in TE field by following a systematic review methodology.
Details
Keywords
Yan Li, Dichen Li, Bingheng Lu, Dajing Gao and Jack Zhou
The purpose of this paper is to review the current status of additive manufacturing (AM) used for tissue engineering (TE) scaffold. AM processes are identified as an effective…
Abstract
Purpose
The purpose of this paper is to review the current status of additive manufacturing (AM) used for tissue engineering (TE) scaffold. AM processes are identified as an effective method for fabricating geometrically complex objects directly from computer models or three-dimensional digital representations. The use of AM technologies in the field of TE has grown rapidly in the past 10 years.
Design/methodology/approach
The processes, materials, precision, applications of different AM technologies and their modified versions used for TE scaffold are presented. Additionally, future directions of AM used for TE scaffold are also discussed.
Findings
There are two principal routes for the fabrication of scaffolds by AM: direct and indirect routes. According to the working principle, the AM technologies used for TE scaffold can be generally classified into: laser-based; nozzle-based; and hybrid. Although a number of materials and fabrication techniques have been developed, each AM technique is a process based on the unique property of the raw materials applied. The fabrication of TE scaffolds faces a variety of challenges, such as expanding the range of materials, improving precision and adapting to complex scaffold structures.
Originality/value
This review presents the latest research regarding AM used for TE scaffold. The information available in this paper helps researchers, scholars and graduate students to get a quick overview on the recent research of AM used for TE scaffold and identify new research directions for AM in TE.
Details
Keywords
Shihe Xin, Marie‐Christine Duluc, François Lusseyran and Patrick Le Quéré
External natural convection is rarely studied by numerical simulation in the literature due to the fact that flow of interest takes place in an unbounded domain and that if a…
Abstract
External natural convection is rarely studied by numerical simulation in the literature due to the fact that flow of interest takes place in an unbounded domain and that if a limited computational domain is used the corresponding outer boundary conditions are unknown. In this study, we propose outer boundary conditions for a limited computational domain and make the corresponding numerical implementation in the scope of a projection method combining spectral methods and domain decomposition techniques. Numerical simulations are performed for both steady natural convection about an isothermal cylinder and transient natural convection around a line‐source. An experiment is also realized in water using particle image velocimetry and thermocouples to make a comparison during transients of external natural convection around a platinum wire heated by Joule effect. Good agreement, observed between numerical simulations and experiments, validated the outer boundary conditions proposed and their numerical implementation. It is also shown that, if one tolerates prediction error, numerical results obtained remain at least reasonable in a region near the line‐source during the entire transients. We thus paved the way for numerical simulation of external natural convection although further studies remain to be done for higher heating power (higher Rayleigh number).
Details
Keywords
M. Tarik Arafat, Ian Gibson and Xu Li
This paper aims to review the advances in additive manufactured (AM) scaffolds for bone tissue engineering (TE). A discussion on the state of the art and future trends of bone TE…
Abstract
Purpose
This paper aims to review the advances in additive manufactured (AM) scaffolds for bone tissue engineering (TE). A discussion on the state of the art and future trends of bone TE scaffolds have been done in terms of design, material and different AM technologies.
Design/methodology/approach
Different structural features and materials used for bone TE scaffolds are evaluated along with the discussion on the potential and limitations of different AM scaffolds. The latest research to improve the biocompatibility of the AM scaffolds is also discussed.
Findings
The discussion gives a clear understanding on the recent research trend in bone TE AM scaffolds.
Originality/value
The information available here would be useful for the researchers working on AM scaffolds to get a quick overview on the recent research trends and/or future direction to work on AM bone TE scaffolds.
Details
Keywords
Maoyuan Li, Yun Zhang, Shi Zhang, Binkui Hou and Huamin Zhou
The orientation behavior of fiber is of great significance in improving the performance of fiber-reinforced polymer products. Generally, the Folgar–Tucker equation can accurately…
Abstract
Purpose
The orientation behavior of fiber is of great significance in improving the performance of fiber-reinforced polymer products. Generally, the Folgar–Tucker equation can accurately describe the variation of orientation vector of fiber, whereas the stability of numerical algorithms was the major challenge. This paper aims to propose an accurate, stable algorithm to solve the Folgar–Tucker equation for the fiber orientation behavior.
Design/methodology/approach
First, the mismatch problem between the strain rate and the pressure field was solved by using the integral transformation method. Then, an accurate, stable algorithm to solve the Folgar–Tucker equation based on the invariant-based optimal fitting method was proposed. The equation was discretized by finite element/finite difference method, and the Lagrange multiplier method was applied to ensure stability.
Findings
The proposed algorithm is proven to accurately and steadily coincide with the experimental results for different cases, including the fiber orientation behaviors under combined flow field, rectangular sheet, three-dimensional computed tomography imaging of tensile specimen and box cases.
Originality/value
The fiber orientation behavior during the injection molding can be accurately predicted, which plays a significant role in determining the mechanical properties of products.
Details
Keywords
To introduce recent research and development of biopolymer deposition for freeform fabrication of three‐dimensional tissue scaffolds that is capable of depositing bioactive…
Abstract
Purpose
To introduce recent research and development of biopolymer deposition for freeform fabrication of three‐dimensional tissue scaffolds that is capable of depositing bioactive ingredients.
Design/methodology/approach
A multi‐nozzle biopolymer deposition system is developed, which is capable of extruding biopolymer solutions and living cells for freeform construction of 3D tissue scaffolds. The deposition process is biocompatible and occurs at room temperature and low pressures to reduce damage to cells. In contrast with other systems, this system is capable of, simultaneously with scaffold construction, depositing controlled amount of cells, growth factors, or other bioactive compounds with precise spatial position to form complex cell‐seeded tissue constructs. The examples shown are based on sodium alginate solutions and poly‐ε‐caprolactone (PCL). Studies of the biopolymer deposition feasibility, structural formability, and different material deposition through a multi‐nozzle heterogeneous system are conducted and presented.
Findings
Provides information about the biopolymer deposition using different nozzle systems, the relations of process parameters on deposition flow rate and scaffold structural formability. Three‐dimensional alginate‐based scaffolds and scaffold embedded with living cells can be freeform constructed according to various design configurations at room temperature without using toxic materials.
Research limitations/implications
Other biopolymers may also be studied for structure formation. Studying cell viability and cellular tissue engineering behavior of the scaffolds after the cell deposition should be further investigated.
Practical implications
A very useful and effective tool for construction of bioactive scaffolds for tissue engineering applications based on a multi‐nozzle biopolymer deposition.
Originality/value
This paper describes a novel process and manufacturing system for fabrication of bioactive tissue scaffolds, automatic cell loading, and heterogeneous tissue constructs for emerging regenerative medicine.
Details
Keywords
Rodrigo Enzo de Prada, Guillermo Rubén Bossio and Mariano Martín Bruno
The purpose of this study is to investigate how the amount of material used and printing parameters affect the mechanical and water sorption properties of acrylonitrile butadiene…
Abstract
Purpose
The purpose of this study is to investigate how the amount of material used and printing parameters affect the mechanical and water sorption properties of acrylonitrile butadiene styrene printed parts.
Design/methodology/approach
The specimens were printed using different printing parameters such as shell number, infill pattern and printing orientation, while accounting for the amount of material used. The mechanical properties of the printed parts were then evaluated using tensile, compression and flexural tests, along with sorption tests.
Findings
The results revealed that the maximum tensile stress of 31.41 MPa was obtained when using 100% infill and a horizontal printing orientation. Similarly, the maximum flexural strength and compression of 40.5 MPa and 100.7 MPa, respectively, were obtained with 100% infill. The printing orientation was found to have a greater impact on mechanical behavior compared to the number of shells or infill patterns. Specifically, the horizontal printing orientation resulted in specimens with at least 25% greater strength compared to the vertical printing orientation. Furthermore, the relationship between the amount of material used and strength was evident in the tensile and flexural tests, which showed a close correlation between the two.
Originality/value
This study’s originality lies in its focus on optimizing the amount of material used to achieve the best strength-to-mass ratio and negligible water infiltration. The findings showed that specimens with two shells and a 60% infill density exhibited the best strength-to-mass ratio.
Details
Keywords
– This paper aims to relate to the study of mechanical properties of materials used in rapid prototyping (RP).
Abstract
Purpose
This paper aims to relate to the study of mechanical properties of materials used in rapid prototyping (RP).
Design/methodology/approach
Comparison of mechanical properties of commercial RP materials. The study of the literature was the essential source of obtaining the results necessary to complete the evaluations and to determine the property ranges.
Findings
Specifications of mechanical properties collected in one paper about mechanical properties and anisotropy enable to define limitations for prototype properties.
Research limitations/implications
The study is limited to accessible data concerning materials from manufacturers’ offers.
Practical implications
The study is particularly useful in the RP methods application.
Originality/value
The obtained study of mechanical properties makes a quick analysis possible. This article also includes the guideline for design engineers, which determines RP method suitability to create functional prototypes of the machines. Mechanical properties of materials have been adopted as a criterion.
Details
Keywords
Thittikorn Phattanaphibul, Pisut Koomsap, Irwansyah Idram and Suchart Nachaisit
This paper aims to introduce selective vacuum manufacturing (SVM), a powder-based rapid prototyping (RP) technique, and the ongoing development to improve its capability to apply…
Abstract
Purpose
This paper aims to introduce selective vacuum manufacturing (SVM), a powder-based rapid prototyping (RP) technique, and the ongoing development to improve its capability to apply in temporary scaffold fabrication.
Design/methodology/approach
SVM employs a combination of sand casting and powder sintering process to construct a prototype layer by layer. A dense layer of support material is prepared and selectively removed to create a cavity where part material is filled and sintered to form a solid layer. In order for SVM to be considered for scaffold fabrication, besides preparing poly-lactic acid (PLA) for part material, support material preparation and process parameters identification have been studied. Redesigning of SVM machine to be more suitable for the real usage has also been presented.
Findings
Particle size of salt has been controlled, and its suitable composition with flour and water has been determined. Process parameters have been identified to scale down the size of scaffolds to meso-scale and to achieve mechanical requirement. Properties of fabricated scaffolds have been enhanced and can be used for soft tissue applications. A prototype of the medical SVM machine has been constructed and tested. An examination of scaffolds fabricated on this new machine also showed their qualification for soft tissue application.
Research limitations/implications
Further study will be on conducting a direct cytotoxicity test to provide the evidence for tissue growth before the clinical usage, on continuing to scaling down the scaffold size, and on improving SVM to meet the requirement of hard tissue.
Originality/value
This simple, inexpensive RP technique demonstrates its viability for scaffold fabrication.