A new fabrication process for rapid prototyping is proposed in this paper. Optical and thermal effects are simultaneously used in this process to locally induce a phase change in…
Abstract
A new fabrication process for rapid prototyping is proposed in this paper. Optical and thermal effects are simultaneously used in this process to locally induce a phase change in a liquid resin. This phase change phenomena is used to “write” three‐dimensional shapes or patterns. Such objects or patterns can involve macroscopic engineering prototypes through to nanostructures for exploitation in waveguiding and photonic crystals. Several advantages can be achieved through this new process, in terms of accuracy, cost and time.
Details
Keywords
T. Patrício, M. Domingos, A. Gloria, U. D'Amora, J.F. Coelho and P.J. Bártolo
The main purpose of this research work is to study the effect of poly lactic acid (PLA) addition into poly (e-caprolactone) (PCL) matrices, as well the influence of the mixing…
Abstract
Purpose
The main purpose of this research work is to study the effect of poly lactic acid (PLA) addition into poly (e-caprolactone) (PCL) matrices, as well the influence of the mixing process on the morphological, thermal, chemical, mechanical and biological performance of the 3D constructs produced with a novel biomanufacturing device (BioCell Printing).
Design/methodology/approach
Two mixing processes are used to prepare PCL/PLA blends, namely melt blending and solvent casting. PCL and PCL/PLA scaffolds are produced via BioCell Printing using a 300-μm nozzle, 0/90° lay down pattern and 350-μm pore size. Several techniques such as scanning electron microscopy (SEM), simultaneous thermal analyzer (STA), nuclear magnetic resonance (NMR), static compression analysis and Alamar BlueTM are used to evaluate scaffold's morphological, thermal, chemical, mechanical and biological properties.
Findings
Results show that the addition of PLA to PCL scaffolds strongly improves the biomechanical performance of the constructs. Additionally, polymer blends obtained by solvent casting present better mechanical and biological properties, compared to blends prepared by melt blending.
Originality/value
This paper undertakes a detailed study on the effect of the mixing process on the biomechanical properties of PCL/PLA scaffolds. Results will enable to prepare customized PCL/PLA scaffolds for tissue engineering applications with improved biological and mechanical properties, compared to PCL scaffolds alone. Additionally, the accuracy and reproducibility of by the BioCell Printing enables to modulate the micro/macro architecture of the scaffolds enhancing tissue regeneration.
Details
Keywords
Fengyuan Liu, Srichand Hinduja and Paulo Bártolo
This paper aims to describe the control software of a novel manufacturing system called plasma-assisted bio-extrusion system (PABS), designed to produce complex multi-material and…
Abstract
Purpose
This paper aims to describe the control software of a novel manufacturing system called plasma-assisted bio-extrusion system (PABS), designed to produce complex multi-material and functionally graded scaffolds for tissue engineering applications. This fabrication system combines multiple pressure-assisted and screw-assisted printing heads and plasma jets. Control software allows the users to create single or multi-material constructs with uniform pore size or pore size gradients by changing the operation parameters, such as geometric parameters, lay-down pattern, filament distance, feed rate and layer thickness, and to produce functional graded scaffolds with different layer-by-layer coating/surface modification strategies by using the plasma modification system.
Design/methodology/approach
MATLAB GUI is used to develop the software, including the design of the user interface and the implementation of all mathematical programing for both multi-extrusion and plasma modification systems.
Findings
Based on the user definition, G programing codes are generated, enabling full integration and synchronization with the hardware of PABS. Single, multi-material and functionally graded scaffolds can be obtained by manipulating different materials, scaffold designs and processing parameters. The software is easy to use, allowing the efficient control of the PABS even for the fabrication of complex scaffolds.
Originality/value
This paper introduces a novel additive manufacturing system for tissue engineering applications describing in detail the software developed to control the system. This new fabrication system represents a step forward regarding the current state-of-the-art technology in the field of biomanufacturing, enabling the design and fabrication of more effective scaffolds matching the mechanical and surface characteristics of the surrounding tissue and enabling the incorporation of high number of cells uniformly distributed and the introduction of multiple cell types with positional specificity.
Details
Keywords
Abstract
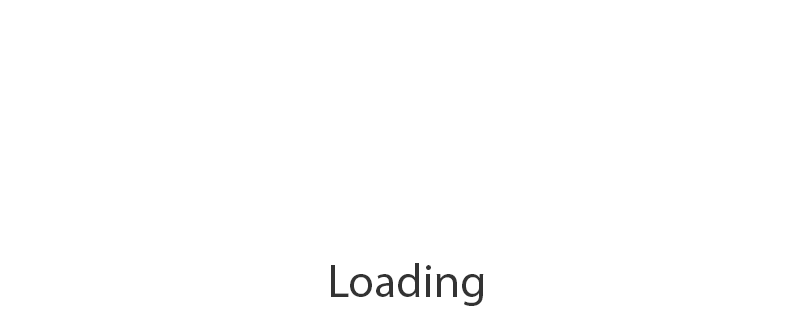
Purpose
Additive manufacturing (AM) or solid freeform fabrication (SFF) technique is extensively used to produce intrinsic 3D structures with high accuracy. Its significant contributions in the field of tissue engineering (TE) have significantly increased in the recent years. TE is used to regenerate or repair impaired tissues which are caused by trauma, disease and injury in human body. There are a number of novel materials such as polymers, ceramics and composites, which possess immense potential for production of scaffolds. However, the major challenge is in developing those bioactive and patient-specific scaffolds, which have a required controlled design like pore architecture with good interconnectivity, optimized porosity and microstructure. Such design not only supports cell proliferation but also promotes good adhesion and differentiation. However, the traditional techniques fail to fulfill all the required specific properties in tissue scaffold. The purpose of this study is to report the review on AM techniques for the fabrication of TE scaffolds.
Design/methodology/approach
The present review paper provides a detailed analysis of the widely used AM techniques to construct tissue scaffolds using stereolithography (SLA), selective laser sintering (SLS), fused deposition modeling (FDM), binder jetting (BJ) and advanced or hybrid additive manufacturing methods.
Findings
Subsequently, this study also focuses on understanding the concepts of TE scaffolds and their characteristics, working principle of scaffolds fabrication process. Besides this, mechanical properties, characteristics of microstructure, in vitro and in vivo analysis of the fabricated scaffolds have also been discussed in detail.
Originality/value
The review paper highlights the way forward in the area of additive manufacturing applications in TE field by following a systematic review methodology.
Details
Keywords
J. Vasco, P. J. Bártolo, B. Silva and C. Galo
Laser milling is a non‐conventional layer‐by‐layer material removal technology suitable for machining a wide range of materials. This technology is particularly suitable to…
Abstract
Purpose
Laser milling is a non‐conventional layer‐by‐layer material removal technology suitable for machining a wide range of materials. This technology is particularly suitable to produce microstructures inside cavities, also obtained by other conventional processes, though with larger material removal rates, or for the direct development of microcavities not requiring high removal rates. This paper seeks to evaluate the capacity of laser milling for manufacturing of mould inserts.
Design/methodology/approach
The paper examined several specific features of laser milling, important for the manufacturing of mould inserts, such as walls verticality, unselected illuminating areas, due to an incorrect STL removal volume definition, aspiration process and orientation, to prevent welding of re‐solidified particles on the surface. Two mould inserts were produced too, assembled on a metallic mould frame and tested with different injection conditions.
Findings
The findings suggest that laser milling is a suitable technology to produce small mould insert for injection moulding, though injection conditions are different as one moves from macroscopic to microscopic injected parts. New design guidelines must be undertaken jointly with the assessment of laser milling performance to make mould microcavities. One of the major difficulties of this process is to keep the side walls vertical plus the generation of undesirable machined volumes, due to unselected illuminating areas below the STL volume, corresponding to the volume to be removed, whenever laser milling is used to operate with structures previously machined. To prevent welding of re‐solidified particles on the surface a proper aspiration must also be considered.
Originality/value
The paper describes the benefits of laser milling technology.
Details
Keywords
A. Touati, S. Corbel and J.P. Corriou
Photolithography allows the fabrication of a solid polymer object through polymerization of a monomer resin by means of a laser source guided according to the data of computer…
Abstract
Photolithography allows the fabrication of a solid polymer object through polymerization of a monomer resin by means of a laser source guided according to the data of computer aided design. However, one drawback of this method is the inaccuracy of the dimensions of the objects related to the shrinkage phenomenon which depends on the polymerization, on the laser flux and on the used sweeping procedure. In this paper, the deformation of an isolated voxel (elementary volume) or a voxel interacting with its neighbor is described. This simulation is based on a kinetic model that takes into account the gel effect and a model of volumetric variation due to the difference of the length of the bonds between the monomer and polymer molecules.
Details
Keywords
M. Tarik Arafat, Ian Gibson and Xu Li
This paper aims to review the advances in additive manufactured (AM) scaffolds for bone tissue engineering (TE). A discussion on the state of the art and future trends of bone TE…
Abstract
Purpose
This paper aims to review the advances in additive manufactured (AM) scaffolds for bone tissue engineering (TE). A discussion on the state of the art and future trends of bone TE scaffolds have been done in terms of design, material and different AM technologies.
Design/methodology/approach
Different structural features and materials used for bone TE scaffolds are evaluated along with the discussion on the potential and limitations of different AM scaffolds. The latest research to improve the biocompatibility of the AM scaffolds is also discussed.
Findings
The discussion gives a clear understanding on the recent research trend in bone TE AM scaffolds.
Originality/value
The information available here would be useful for the researchers working on AM scaffolds to get a quick overview on the recent research trends and/or future direction to work on AM bone TE scaffolds.
Details
Keywords
M. Domingos, F. Chiellini, A. Gloria, L. Ambrosio, P. Bartolo and E. Chiellini
This paper aims to report a detailed study regarding the influence of process parameters on the morphological/mechanical properties of poly(ε‐caprolactone) (PCL) scaffolds…
Abstract
Purpose
This paper aims to report a detailed study regarding the influence of process parameters on the morphological/mechanical properties of poly(ε‐caprolactone) (PCL) scaffolds manufactured by using a novel extrusion‐based system that is called BioExtruder.
Design/methodology/approach
In this study the authors focused investigations on four parameters, namely the liquefier temperature (LT), screw rotation velocity (SRV), deposition velocity (DV) and slice thickness (ST). Scaffolds were fabricated by employing three different values of each parameter. Through a series of trials, scaffolds were manufactured varying iteratively one parameter while maintaining constant the other ones. The morphology of the structures was investigated using a scanning electron microscope (SEM), whilst the mechanical performance was assessed though compression tests.
Findings
Experimental results highlight a direct influence of the process parameters on the PCL scaffolds properties. In particular, DV and SRV have the highest influence in terms of road width (RW) and consequently on the porosity and mechanical behaviour of the structures.
Research limitations/implications
The effect of process and design parameters on the biological response of scaffolds is currently under investigation.
Originality/value
The output of this work provides a major insight into the effect of process parameters on the morphological/mechanical properties of PCL scaffolds. Moreover, the potential and feasibility of this novel extrusion‐based system open a new opportunity to study how structural features may influence the characteristics and performances of the scaffolds, enabling the development of integrated biomechanical models that can be used in CAD systems to manufacture customized structures for tissue regeneration.
Details
Keywords
Valiollah Panahizadeh, Amir Hossein Ghasemi, Yaghoub Dadgar Asl and Mohammadmahdi Davoudi
This paper aims to study multiobjective genetic algorithm ability in determining the process parameter and postprocess condition that leads to maximum relative density (RD) and…
Abstract
Purpose
This paper aims to study multiobjective genetic algorithm ability in determining the process parameter and postprocess condition that leads to maximum relative density (RD) and minimum surface roughness (Ra) simultaneously in the case of a Ti6Al4V sample process by laser beam powder bed fusion.
Design/methodology/approach
In this research, the nondominated sorting genetic algorithm II is used to achieve situations that correspond to the highest RD and the lowest Ra together.
Findings
The results show that several situations cause achieving the best RD and optimum Ra. According to the Pareto frontal diagram, there are several choices in a close neighborhood, so that the best setup conditions found to be 102–105 watt for laser power followed by scanning speed of 623–630 mm/s, hatch space of 76–73 µm, scanning patter angle of 35°–45° and heat treatment temperature of 638–640°C.
Originality/value
Suitable selection of process parameters and postprocessing treatments lead to a significant reduction in time and cost.
Details
Keywords
Xiangquan Wu, Qin Lian, Dichen Li and Zhongmin Jin
This study aims to develop a multi-material stereolithography (MMSL) technique to directly fabricate a biphasic osteochondral scaffold.
Abstract
Purpose
This study aims to develop a multi-material stereolithography (MMSL) technique to directly fabricate a biphasic osteochondral scaffold.
Design/methodology/approach
A bespoke prototype MMSL system was developed based on a bottom-up mask projection approach. The system was controlled by a multi-material fabrication algorithm with minimum number of switching cycles during fabrication. A variable-power light source was used to fabricate materials with significantly different curing characteristics. The light-curable poly(ethylene glycol) diacrylate (PEGDA) hydrogel and beta-tricalcium phosphate (β-TCP) ceramic suspension were used for fabricating the biphasic osteochondral scaffold.
Findings
The bonding strength of the multi-material interface is shown to be mainly affected by the type of photopolymer, rather than the switching of the materials in MMSL. Lighting power densities of 2.64 and 14.98 mW/cm2 were used for curing the PEGDA hydrogel and the ß-TCP ceramic suspension, respectively. A biphasic osteochondral scaffold with complex interface was successfully fabricated.
Originality/value
This study proposes a potential technical method (MMSL) for manufacturing a complex biphasic osteochondral scaffold composing a PEGDA hydrogel/ß-TCP ceramic composite in a time-efficient and precise manner. The designed bone-cartilage scaffold interface and the surface of the cartilage scaffold can be precisely manufactured.