Abstract
Purpose
Powder bed-based additive manufacturing (AM) is a promising family of technologies for industrial applications. The purpose of this study is to provide a new metrics based on the analysis of the compaction behavior for the evaluation of flowability of AM powders.
Design/methodology/approach
In this work, a novel qualification methodology based on a camera mounted onto a commercially available tap density meter allowed to assess the compaction behavior of a selection of AM materials, both polymers and metals. This methodology automatizes the reading of the powder height and obtains more information compared to ASTM B527. A novel property is introduced, the “tapping modulus,” which describes the packing speed of a powdered material and is related to a compression/vibration powder flow.
Findings
The compaction behavior was successfully correlated with the dynamic angle of repose for polymers, but interestingly not for metals, shedding more light to the different flow behavior of these materials.
Research limitations/implications
Because of the chosen materials, the results may lack generalizability. For example, the application of this methodology outside of AM would be interesting.
Originality/value
This paper suggests a new methodology for assessing the flowing behavior of AM materials when subjected to compression. The device is inexpensive and easy to implement in a quality assurance environment, being thus interesting for industrial applications.
Keywords
Citation
Sillani, F., Wagner, D., Spurek, M.A., Haferkamp, L., Spierings, A.B., Schmid, M. and Wegener, K. (2021), "Compaction behavior of powder bed fusion feedstock for metal and polymer additive manufacturing", Rapid Prototyping Journal, Vol. 27 No. 11, pp. 58-66. https://doi.org/10.1108/RPJ-01-2021-0010
Publisher
:Emerald Publishing Limited
Copyright © 2021, Francesco Sillani, Dominik Wagner, Marvin Aaron Spurek, Lukas Haferkamp, Adriaan Bernardus Spierings, Manfred Schmid and Konrad Wegener.
License
Published by Emerald Publishing Limited. This article is published under the Creative Commons Attribution (CC BY 4.0) licence. Anyone may reproduce, distribute, translate and create derivative works of this article (for both commercial and non-commercial purposes), subject to full attribution to the original publication and authors. The full terms of this licence may be seen at http://creativecommons.org/licences/by/4.0/legalcode
1. Introduction
Additive manufacturing (AM) is attracting strong interest in many industries: production of end-use parts can be achieved within a few hours or days for an increasing number of applications.
Powder bed fusion (PBF) of both polymers and metals is the family of AM technologies that is closest to industrial applications: complex parts with a wide range of properties can be produced on demand and with much more design freedom compared to traditional machining. Nevertheless, the material range is still limited, and especially for selective laser sintering (PBF-LB/P, powder bed fusion of polymers with a laser beam, according to ISO/ASTM 52900 [ASTM International and ISO, 2018]), the material palette is mostly restricted to polyamide 12 (PA12) and its composites.
Recently, the interest of material suppliers to offer new polymer classes and metal alloys has grown. This is due to an overall PBF market growth, mainly driven by industrialization of this family of technologies, which can be estimated by looking at the year-over-year growth of polymer and metal feedstock, which in 2018 was 37.9% and 41.9%, respectively (Caffrey and Wohler, 2019). Gas atomization and plasma rotating electrode processes have become the industrial standard for the production of metal powders for selective laser melting (PBF-LB/M, powder bed fusion of metals with a laser beam, according to ISO/ASTM 52900 [ASTM International and ISO, 2018]) and yield spherical powders with low amount of porosity, as reported by Sames et al. (2016). Polymer powders are currently produced through different routes: cryogenic milling is the most common technique for short time-to-market products, thanks to its simplicity compared to more complex processes such as dissolution–precipitation. The dissolution–precipitation procedure is carried out with ethanol as solvent in specific temperature and pressure conditions, as reported by Baumann and Wilczok (1998), and is used to produce PA12 particles characterized by a “potato” shape (Schmid et al., 2017). Melt emulsification is used to produce powders from an immiscible mixture of a “carrier” and “target” polymer. The mixture is coextruded at high temperature, and then the “carrier” polymer is selectively washed away using an appropriate solvent that does not dissolve the “target” polymer. Vetterli (2019) reported a regular distribution of spherical particles for polypropylene produced through melt emulsification, and Kleijnen et al. (2019) confirmed the same for polybutylene terephthalate. Schmid et al. (2014) report that optimization of powder shape and size distributions brings significant advantages for flowability, for which the following definition from Gotoh et al. (2001) can be used: “[flowability represents the powder] ease of flow and relates to the change of mutual position of individual particles forming the powder bed.” Gotoh also suggests numerous ways to assess flowability, as real powder flow typically occurs as a combination of different “flow patterns,” a term that comes from fluid mechanics and that is used to define how a fluid flows through a reactor. Vock et al. (2019) report that the main flow pattern is strongly application dependent, whereas different expressions of flowability can refer to the same flow pattern. In AM, for example, the typical flowability metrics are angle of repose (gravitational, compression and fluidized flow) and compressibility (compression and vibration flow) (Vock et al., 2019), both qualitatively depicted in Figure 1.
For polymers, the flowability measured through the angle of repose is critical for obtaining smooth powder layers and, consequently, an error-free processing (Amado, 2016). Vetterli (2019) reported a positive correlation between the final part density and the powder bed density, highlighting the importance of compressibility in PBM of polymers. Regarding metals, powder flowability (Spierings et al., 2016; Seyda, 2018) and powder bed density (Spierings et al., 2016; Li et al., 2010; Ali et al., 2018) are also often stressed as relevant influences on part density. Haferkamp et al. (2021), however, recently showed only a limited correlation between powder layer density (similar to powder bed density) and part density: this might mean that flowability affects PBM of polymers and metals in a different way.
Numerous examples in AM literature (Vetterli, 2019; Vock et al., 2019; Amado, 2016; Ziegelmeier et al., 2013; Berretta, 2015) suggest that the dynamic angle of repose, also called avalanche angle, is the most used mean to model the flowing behavior during the recoating step. Kiani et al. (2020) and Spierings et al. (2016) furthermore argue that the avalanche angle measurement corresponds well to the process condition in PBF. The compaction behavior, on the other hand, is typically measured by the Hausner ratio H:
ASTM B527, in particular, prescribes to let the powder compact inside of a cylinder with a certain diameter (depending on its material density ρm), subjected to an oscillating motion in the vertical direction with an amplitude of 3 mm for 3,000 periods (taps), as shown in Figure 2.
The final value of the powder volume Vpowder is manually read from the cylinder and used to compute ρtap according to:
The tap density is the packing density of a powder in the highest possible state of compaction. When measuring the tap density according to ASTM B527, some information is lost, as powders can have the same Hausner ratio H but different curves when compacting from bulk to tap density. This has been already observed by Vetterli (2019), who compared two commercially available polyamide 12 powders: Duraform PA12 (3 D Systems, USA), produced using dissolution–precipitation (Baumann and Wilczok, 1998), and Orgasol Invent Smooth (Arkema, France), produced via direct solvent polymerization (Schmid et al., 2017). The powders had a similar particle size but, because of their production process, different shape distributions. The device used by Vetterli (2019) was capable of recording the powder height after every tap, but the prescription of “compression under its own weight” reported in ASTM B527 was not respected because a metal disk was placed on the top powder surface. The obtained results showed very similar Hausner ratios but substantially different “compaction curves,” as reported in Figure 3.
Scope of the current work is thus to investigate the compaction behavior of a selection of commercially available AM powders, both polymers and metals. The evaluation of the compaction behavior will be carried out with a novel approach on a device specifically designed for this purpose. Repeatability of the aforementioned device is validated, and it will provide additional insights on powder flowability under compression flow compared to the methodologies currently available on the market. Finally, the compaction behavior will be correlated with dynamic angle of repose αA and Hausner ratio H to understand its possible utility as quality assurance method for PBF AM.
2. Materials and methods
2.1 Powders
This study was carried out on commercially available materials that cover a broad spectrum of size and shape distributions, as highlighted in subsection 3.1. All materials were tested as received, with no specific conditioning, and their data are reported in Table 1 and Table 2.
2.2 Particle size and shape distributions
The particle size distribution (PSD) was assessed using a LS230 laser diffraction device (Beckman Coulter – Brea, CA, USA) with conventional measurements taken on dispersed samples (0.03Wt.% in ethanol). A DM-6 (Leica – Wetzlar, Germany) optical microscope was used with the procedure introduced in the study of Sillani et al. (2019) to calculate the particle shape distribution. The shape was characterized using elliptic smoothness ES after fitting each particle with an ellipse of same area, orientation and centroid as in Figure 4 using the software ImageJ.
The shape factor ES was then calculated as follows:
Using elliptic smoothness for metal feedstock is unusual, as the atomization process typically produces very spherical particles. Nevertheless, being circles a particular case of ellipses, and considering that in this work both polymer and metal feedstock are simultaneously analyzed, the usage of ES seems reasonable in this context.
2.3 Evaluation of compaction behavior
A BeDensi T3 Tap Density Meter (Bettersize, Dandong, Liaoning, China) was modified and used for the measurement of the compaction behavior. The existing motor controller of the device was replaced with a Raspberry Pi 3 Model B+ (Raspberry Pi Foundation, Cambridge, UK) and a IDS UI-3360CP (IDS Imaging Development Systems GmbH, Obersulm, Germany) camera for the automated evaluation of the powder height was integrated. The final setup is depicted in Figure 5.
The bulk density ρbulk of each powder was assessed according to ASTM B417, and then the weight of 90 cm3 of material was calculated with:
Afterwards, this amount of powder was weighted using a AE200 balance with a AB33360 measuring unit (Mettler Toledo, Schwerzenbach, Switzerland) and carefully inserted into the glass cylinder using a funnel. The measurement itself consisted of 1,000 taps at two different tapping frequencies with 3 mm motion amplitude, whereas a video was being recorded using the camera. The first frequency was selected to be 0.16 Hz for taps 1 to 25, whereas the second tapping frequency used was 2 Hz for taps 26 to 1,000. Compared to the recommended values of 1.6 Hz to 5 Hz (ASTM B527), these tapping frequencies were selected to allow complete powder movement after each tap (settling). A MATLAB[textregistered] script was first used to calculate the height of the powder h(tx) for every frame x, as shown in Figure 6.
Afterwards, each tap was automatically recognized, as highlighted in Figure 7.
The same script automatically calculated the settling volume
Then, the settling volume
Following relations also hold:
2.4 Evaluation of dynamic angle of repose
A REVOLUTION Powder Analyzer (Mercury Scientific – Newton, CT, USA) was used to assess the dynamic angle of repose αA. The measurement was repeated three times for every sample, with 128 avalanches recorded per run. The dynamic angle of repose was calculated for every avalanche, and an average value was used.
2.5 Characterization of compaction curve
Each compaction curve was first normalized for every tap i using as follows:
Then, a linear regression was applied to the first 15 data points to capture the most linear part of the compaction behavior. The slope of the obtained line is defined as the normalized tapping modulus
2.6 Repeatability evaluation of setup
The performances of modified tapping device introduced in this work had to be statistically evaluated to assess its repeatability. Every material was tested five times by the same operator, and the variance per feedstock was then calculated according to the procedure outlined in Figure 8.
All the five curves referring to the same powder are used to obtain an average powder density after every tap
3. Results and discussion
3.1 Material selection
The feedstock used for this work was chosen to cover a variety of powder properties and to show the suitability of the proposed methodology to study the flowability of AM materials. The powder data set comprises size distribution [Figure 9(a)], shape distribution (Figure 9(c)] and flowability [Figure 9(b), Hausner ratio H and Figure 9(d), avalanche angle αA]. The verification was done qualitatively by plotting the most relevant properties of each powder: this analysis shows that the chosen materials are covering a wide spectrum of characteristics, and this supports a wide applicability of the proposed methodology for the evaluation of compression/vibration flow for AM feedstock.
3.2 Compaction behavior – Tapping modulus
Compaction curves for all the powders were measured following the procedure in subsection 2.3, and the average curve for each material is shown in Figure 10(a). To assess the compression/vibration flow behavior associated with each material, all curves were further characterized according to the methodology in subsection 2.5. The results of the linear regression are reported in Figure 10(b) together with the quality of the fit R2, whereas
Materials exhibiting higher
To better understand the utility of the
3.3 Compaction behavior – Repeatability study
Compaction curves for all feedstock were shown in Figure 10(a) as an average of five experimental runs, and their relative standard deviations
The standard deviation shows that most of the variance in the powder density is created in the first tens of taps, possibly as a consequence of the cylinder filling procedure based on pouring. Nevertheless, the maximum
4. Conclusion and outlook
In the current work, a novel methodology for the evaluation of flowability has been designed, tested and compared with the dynamic angle of repose and Hausner ratio. A commercially available tap density meter was upgraded with a camera that allowed to obtain the change of powder density in real-time. A representative sample of AM feedstock, including both metals and polymers, was chosen for this work through the analysis of four indicators (median diameter, elliptic smoothness, avalanche angle and Hausner ratio). The heterogeneity of the samples with respect to the proposed properties was confirmed and hence supports wide applicability of the proposed methodology in the field of AM. A novel indicator of compression flow is proposed, namely, the “normalized tapping modulus”
Figures
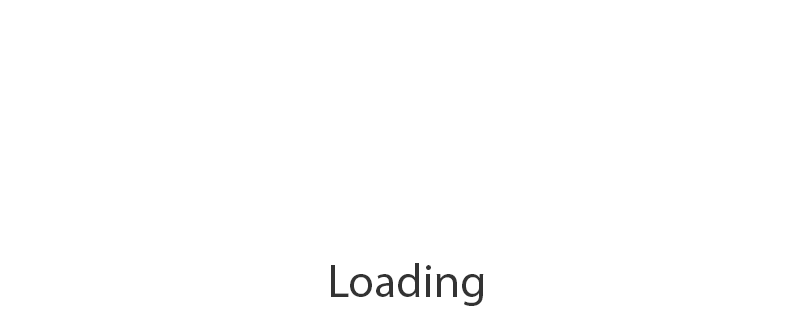
Figure 3
Compaction of Duraform PA12 (H = 1.13) and Orgasol Invent Smooth PA12 (H = 1.12) from Vetterli (2019)
Polymer feedstock
Producer | Commercial name (short) | Material type | Production method |
---|---|---|---|
3 D Systems (Rock Hill, SC, USA) | Duraform PA12 (PA12-SLS) | Polyamide 12 | Dissolution precipitation |
EOS (Kreilling, Germany) | PA1102 (PA11-SLS) | Polyamide 11 | Cryogenic grinding + particle rounding |
Diamond Plastics (Gräfenberg, Germany) | Laser PP CP 50 (PP-SLS-1) | Polypropylene | Cryogenic grinding |
Aspect (Tokyo, Japan) | iCoPP (PP-SLS-2) | Polypropylene | Melt emulsification |
3 D Systems (Rock Hill, SC, USA) | Duraform Flex (TPE-SLS) | Thermoplastic elastomer | Cryogenic grinding |
Metal feedstock
Producer | Commercial name (short) | Material type | Production method |
---|---|---|---|
Carpenter (Philadelphia, PA, USA) | Micro Melt 316 L 15 µm (316 L-MIM-1) | 1.4404 stainless steel | Gas atomization |
CNPC (Shanghai, China) | SS316 powder D50 30 µm to 50 µm (316 L-SLM) | 1.4404 stainless steel | Gas atomization |
Praxair (Danbury, CT, USA) | FE 271–1 (316 L-MIM-2) | 1.4404 stainless steel | Gas atomization |
IMR Metal powder technologies GmbH (Velden am Wörthersee, Austria) | AlSi10Mg Gries (A360-SLM-1) | AlSiMg10 | Gas atomization |
Tekna Advanced Materials Inc. (Sherbrooke, QC, Canada) | AlSi10Mg-64/20-CS05 (A360-SLM-2) | AlSiMg10 | Plasma atomization |
Material |
|
---|---|
316L-MIM-2 | 5.52 |
316 L-MIM-1 | 5.33 |
A360-SLM-1 | 4.68 |
PP-SLS-2 | 4.62 |
PA11-SLS | 4.55 |
A360-SLM-2 | 4.43 |
PA12-SLS | 4.30 |
316 L-SLM | 3.78 |
PP-SLS-1 | 3.72 |
TPE-SLS | 2.63 |
Material |
|
ρm |
|
---|---|---|---|
PP-SLS-2 | 0.007 | 1.000 | 0.007 |
Iron | 0.100 | 7.874 | 0.013 |
References
Ali, U., Mahmoodkhani, Y., Shahabad, S.I., Esmaeilizadeh, R., Liravi, F., Sheydaeian, E., Huang, K.Y., Marzbanrad, E., Vlasea, M. and Toyserkani, E. (2018), “On the measurement of relative powder-bed compaction density in powder-bed additive manufacturing processes”, Materials & Design, Vol. 155, doi: 10.1016/j.matdes.2018.06.030, ISSN 02641275.
Amado, F. (2016), “Characterization and prediction of SLS processability of polymer powders with respect to powder flow and part warpage”, PhD thesis, ETH Zürich.
ASTM International and ISO (2018), “ISO/ASTM 52900 – 18: additive manufacturing terminology”.
ASTM International (2018), “ASTM B417 – 18: standard test method for apparent density of non-free-flowing metal powders using the carney funnel”.
ASTM International (2015), “ASTM B527 – 15: standard test method for tap density of metal powders and compounds”.
Baumann, F.-E. and Wilczok, N. (1998), “Preparation of precipitated polyamid powders of narrow particle size distribution and low porosity”.
Berretta, S. (2015), “Poly ether ether ketone (PEEK) polymers for high temperature laser sintering (HT-LS)”, p. 341.
Caffrey, T. and Wohler, T. (2019), Wohlers Report 2019, Technical report.
Gotoh, K., Masuda, H. and Higashitani, K. (2001), Powder Technology Handbook, volume 10, CRC Press, ISBN 9780429190186, doi: 10.1016/0921-5093(93)90508-c, available at: www.taylorfrancis.com/books/9781439831885
Haferkamp, L., Haudenschild, L., Spierings, A., Wegener, K., Riener, K., Ziegelmeier, S. and Leichtfried, G.J. (2021), “The influence of particle shape, powder flowability, and powder layer density on part density in laser powder bed fusion”, Metals, Vol. 11 No. 3, doi: 10.3390/met11030418, ISSN 2075-4701.
Kleijnen, R., Schmid, M. and Wegener, K. (2019), “Production and processing of a spherical polybutylene terephthalate powder for laser sintering”, Applied Sciences, Vol. 9 No. 7, p. 1308, doi: 10.3390/app9071308, ISSN 2076-3417, available at: www.mdpi.com/2076-3417/9/7/1308
Kiani, P., Scipioni Bertoli, U., Dupuy, A.D., Ma, K. and Schoenung, J.M. (2020), “A statistical analysis of powder flowability in metal additive manufacturing”, Advanced Engineering Materials, Vol. 22 No. 10, doi: 10.1002/adem.202000022, ISSN 1438-1656.
Li, R., Shi, Y., Wang, Z., Li, W., Liu, J. and Jiang, W. (2010), “Densification behavior of gas and water atomized 316L stainless steel powder during selective laser melting”, Applied Surface Science, Vol. 256 No. 13, ISSN 01694332, doi: 10.1016/j.apsusc.2010.02.030.
Ramanujan, S. (1914), “Modular equations and approximations to π”, Quarterly Journal of Mathematics, Vol. 45, pp. 350-372.
Rietema, K. (1991), The Dynamics of Fine Powders, Elsevier Science Publishing Co., Inc., New York, NY, ISBN 1-85166-594-3.
Sames, W.J., List, F.A., Pannala, S., Dehoff, R.R. and Babu, S.S. (2016), “The metallurgy and processing science of metal additive manufacturing”, International Materials Reviews, Vol. 61 No. 5, pp. 315-360, doi: 10.1080/09506608.2015.1116649, ISSN 0950-6608, available at: www.tandfonline.com/doi/full/10.1080/09506608.2015.1116649
Schmid, M., Amado, F. and Wegener, K. (2014), “Materials perspective of polymers for additive manufacturing with selective laser sintering”, Journal of Materials Research, Vol. 29 No. 17, pp. 1824-1832, doi: 10.1557/jmr.2014.138, ISSN 0884-2914, available at: www.journals.cambridge.org/abstract_S0884291414001381
Schmid, M., Kleijnen, R., Vetterli, M. and Wegener, K. (2017), “Influence of the origin of polyamide 12 powder on the laser sintering process and laser sintered parts”, Applied Sciences, Vol. 7 No. 5, p. 462, doi: 10.3390/app7050462, ISSN 2076-3417, available at: www.mdpi.com/2076-3417/7/5/462
Seyda, V. (2018), “Werkstoff- und prozessverhalten von metallpulvern in der laseradditiven fertigung”, ISBN 978-3-662-58232-9.
Sillani, F., Kleijnen, R.G., Vetterli, M., Schmid, M. and Wegener, K. (2019), “Selective laser sintering and multi jet fusion: process-induced modification of the raw materials and analyses of parts performance”, Additive Manufacturing, Vol. 27, pp. 32-41, doi: 10.1016/j.addma.2019.02.004, ISSN 22148604, available at: https://linkinghub.elsevier.com/retrieve/pii/S2214860418308972
Spierings, A.B., Voegtlin, M., Bauer, T. and Wegener, K. (2016), “Powder flowability characterisation methodology for powder-bed-based metal additive manufacturing”, Progress in Additive Manufacturing, Vol. 1 Nos 1/2, doi: 10.1007/s40964-015-0001-4, ISSN 2363-9512.
Vetterli, M. (2019), “Powder optimization for laser sintering: an insight in powder intrinsic and extrinsic properties”, PhD thesis, ETH Zurich.
Vock, S., Klöden, B., Kirchner, A., Weißgärber, T. and Kieback, B. (2019), “Powders for powder bed fusion: a review”, Progress in Additive Manufacturing, Vol. 4 No. 4, doi: 10.1007/s40964-019-00078-6, ISSN 2363-9512, available at: http://link.springer.com/10.1007/s40964-019-00078-6
Ziegelmeier, S., Wollecke, F., Tuck, C., Goodridge, R. and Hague, R. (2013), “Characterizing the bulk & flow behaviour of LS polymer powders”, Solid Freeform Fabrication Symposium, pp. 354-367.