Abstract
Purpose
Buckling should be carefully considered in steel assemblies with members subjected to compressive stresses, such as bracing systems and truss structures, in which angles and built-up steel sections are widely employed. These type of steel members are affected by torsional and flexural-torsional buckling, but the European (EN 1993-1-2) and the American (AISC 360-16) design norms do not explicitly treat these phenomena in fire situation. In this work, improved buckling curves based on the EN 1993-1-2 were extended by exploiting a previous work of the authors. Moreover, new buckling curves of AISC 360-16 were proposed.
Design/methodology/approach
The buckling curves provided in the norms and the proposed ones were compared with the results of numerical investigation. Compressed angles, tee and cruciform steel members at elevated temperature were studied. More than 41,000 GMNIA analyses were performed on profiles with different lengths with sections of class 1 to 3, and they were subjected to five uniform temperature distributions (400–800 C) and with three steel grades (S235, S275, S355).
Findings
It was observed that the actual buckling curves provide unconservative or overconservative predictions for various range of slenderness of practical interest. The proposed curves allow for safer and more accurate predictions, as confirmed by statistical investigation.
Originality/value
This paper provides new design buckling curves for torsional and flexural-torsional buckling at elevated temperature since there is a lack of studies in the field and the design standards do not appropriately consider these phenomena.
Keywords
Citation
Possidente, L., Tondini, N. and Battini, J.-M. (2022), "Fire buckling curves for torsionally sensitive steel members subjected to axial compression", Journal of Structural Fire Engineering, Vol. 13 No. 2, pp. 171-193. https://doi.org/10.1108/JSFE-06-2021-0034
Publisher
:Emerald Publishing Limited
Copyright © 2021, Luca Possidente, Nicola Tondini and Jean-Marc Battini
License
Published by Emerald Publishing Limited. This article is published under the Creative Commons Attribution (CC BY 4.0) licence. Anyone may reproduce, distribute, translate and create derivative works of this article (for both commercial and non-commercial purposes), subject to full attribution to the original publication and authors. The full terms of this licence may be seen at http://creativecommons.org/licences/by/4.0/legalcode
1. Introduction
Steel angle, cruciform and tee sections are frequently employed in bracing systems or in truss structures, in which they are mainly subjected to compressive actions. Thus, their resistance can be affected by instability phenomena. Local effects are negligible for compact sections and global buckling modes govern the behaviour of the steel elements. Unless flexural buckling is prevented by lateral restraints, in compressed hot-rolled or welded I or H profiles, torsional effects are rare. Nonetheless, for angle, tee and cruciform steel sections, torsional or flexural-torsional buckling can be relevant, notably in a low slenderness range. Hereafter angles, tee and cruciform sections are referred to as L, T and X sections, respectively.
Bracing systems and truss structures can be commonly found, for instance, in single-storey buildings, such as industrial halls. These structures may store large quantities of combustible material; thus, fire can be a significant threat. Consequently, assessment of the structural fire performance becomes paramount. In addition, these building typologies are generally characterised by large floor areas that increase the probability of ignition. Indeed, also the fuel material may be of particular hazardous nature, e.g. chemical substances, paints, that enhance the danger of fire occurrence too. Hence, the spread of a fire may have significant consequences. In terms of fire risk, for instance Possidente et al. (2020) showed an example of application of fire risk assessment applied to a multi-storey steel building.
In the European norm, prescriptions for the design of compressed steel members are given in two separate codes for ambient, EN 1993-1-1 (CEN (European Committee for Standardisation), 2005a), and elevated temperature, EN 1993-1-2 (CEN (European Committee for Standardisation), 2005b), respectively. Instead, the American Specification for Structural Steel Buildings AISC 360-16 (AISC American Institute of Steel Construction, 2016) considers the behaviour of steel members at both ambient and elevated temperature, though the latter is described only in Appendix 4 (AISC American Institute of Steel Construction, 2016). In both the European and American specifications, the resistance of axially compressed steel members is reduced according to the slenderness of the element. The evolution of the design resistance with the slenderness is summarised into the form of buckling curves. These curves were based on experimental and numerical results for H- and I-profiles and later, were calibrated and extended to other profiles, such as L profiles. In detail, in EN 1993-1-2 flexural buckling is considered according to the model presented by Franssen et al. (1995), whereas the indications given in AISC 360-16 are based on the more recent buckling curve proposed by Takagi and Deierlein (2007). Only pure flexural buckling of compressed steel members in fire situation is analysed in both norms, whilst curves for flexural-torsional and torsional buckling are not explicitly integrated. Apparently, the prescribed buckling curves are deemed adequate also for the design of steel elements prone to flexural-torsional and torsional buckling at elevated temperature.
In the last decades, researchers investigated different instability phenomena in steel elements in fire situation, such as lateral-torsional buckling (Bailey et al., 1996; Vila Real and Franssen, 2000; Vila Real et al., 2004b) and its interaction with local instabilities (Vila Real et al., 2004a; Couto et al., 2014; Prachar et al., 2015; Couto et al., 2016; Couto et al., 2018; Franssen et al., 2016). Nevertheless, there is a lack of studies about the torsional and flexural-torsional buckling of angles and built-up steel members in compression at elevated temperature made of hot-rolled profiles, whereas such buckling phenomena have been studied for cold-formed steel profiles at both ambient and elevated temperatures (Schafer, 2008; Popovic et al., 2001; Ranawaka and Mahendran, 2010; Silvestre et al., 2013; Laím and Rodrigues, 2018; Craveiro et al., 2018; Arrais et al., 2021). Indeed, owing to the shape and the small thickness, an interaction of local, distortional and global buckling influences the resistance of L, T and X thin-walled members at ambient temperature, as demonstrated by Dinis et al. (2010). Further discussions about X sections were provided in Dabrowski (1988), Chen and Trahair (2006) and Trahair (2012).
In this context, the present paper treats the torsional and flexural-torsional buckling of compressed L, T and X steel profiles, obtained by coupling L sections or by cutting H or I hot-rolled profiles. Two dedicated buckling curves that better reproduce the results of a numerical investigation were proposed based on the EN 1993-1-2 and AISC 360-16 curves, respectively. A statistical investigation allowed for an additional discussion about the results of the proposed curves and the ones prescribed in the European and the American codes.
2. European and American norm provisions
The current approaches for the evaluation of the resistance of compressed steel members in fire recommended in the European and American standards are briefly presented in this section. In the Eurocodes, fire is treated separately and provisions for structural steel of EN-1993-1-1 (CEN (European Committee for Standardisation), 2005a) are modified and adapted to the fire situation in EN-1993-1-2 (CEN (European Committee for Standardisation), 2005b). The degradation of mechanical properties at elevated temperature is taken into account and equations for the definition of the design buckling resistance
2.1 EN 1993-1-2 provisions
According to EN 1993-1-2, the resistance of steel members should be reduced to account for the effect of buckling at elevated temperature. For compressed elements with a uniform temperature
The generalised imperfection factor
While the non-dimensional slenderness
It should be pointed out that EN 1993-1-2 may generate confusion by defining
An analogous argumentation has been extended to the AISC 360-16 buckling curves.
2.2 AISC 360-16 provisions
The Specification for Structural Steel Buildings AISC 360-16 reccomends to determine the nominal strength for compression
The equation for the definition of the critical stress
For comparison purposes, the equations from the Specification for Structural Steel Buildings can be rewritten substituting some quantities with the equivalent counterpart of EN 1993-1-2 (Table 1). Eq. (10) can be rewritten observing that both
Thus Eq. (9) can be rewritten as
Finally, an equivalent reduction factor to reduce the full nominal strength for compression at elevated temperature
3. Numerical simulation
An extensive numerical campaign, consisting of more than 41,000 analyses was carried out to investigate the behaviour of concentrically compressed steel members subjected to fire that may be sensitive to torsional or flexural-torsional buckling. Geometrically and materially imperfect non-linear analyses (GMNIA) by means of finite element analysis (FEA) were performed, and results were collected in terms of resistance and later compared with the buckling curves predictions from EN-1993-1-2 and AISC 360-16. The set of investigated sections consisted of L, T or X cross-sections, defined by coupling L sections back-to-back, in case of T and X sections, or by cutting in two halves H or I hot-rolled steel profiles for additional T sections. In the case of coupled sections, it was assumed that the spacing of the connections was short enough to check the closely built-up members for buckling as single integral members (CEN (European Committee for Standardisation), 2005a). Meaningful predictions of the behaviour of coupled members were obtained with this assumption in several papers (Dinis et al., 2010; Dabrowski, 1988; Chen and Trahair, 2006; Trahair, 2012). Nevertheless, connecting plates or battens could be considered in more refined numerical models. The length, the temperature and the steel grade of the compressed members were varied in the analyses. Three steel grades were selected, namely S235, S275, S355. Members subjected to five different uniform temperatures were studied: 400, 500, 600, 700 and 800 C. Indeed, the temperature range 400–800 C is usually the most relevant temperature range, as proved for columns that buckle flexurally in Franssen et al. (1995) and confirmed by preliminary analyses for the cross-sections studied in this work. For each temperature about 8,200 columns were analysed with a length-to-width ratio higher than 3, in order to limit the analyses to columns of practical interest. Table 2 summarises the partial and the total number of the performed analyses. The analyses that showed convergence problems were discarded and were not considered in the count. A total of 45 different equal leg L profiles of commercial dimensions were studied. 68 T section and 45 X sections were made of 2 and 4 coupled L sections respectively. 129 T sections were obtained by dividing into two halves hot-rolled H- or I-sections. The different section types are summarised in Table 3. The set of the investigated columns was selected so that according to the classification of the sections in fire situation of EN 1993-1-2 and AISC 360-16, only class 1, class 2 or class 3 cross-sections, or non-slender-elements were investigated.
3.1 GMNIA analyses and finite elements
Each one of the GMNIA analyses, performed for a column with given cross-section, length, steel grade and temperature, consisted of a three-step procedure.
Step 1. A linear eigenvalue analysis was performed at ambient temperature to determine the shape of the lowest buckling mode.
Step 2. The buckling mode obtained from STEP 1 was scaled so that the maximum nodal displacement along the column equalled 1/1,000 of the length and was introduced as initial imperfection in the numerical model of the column.
Step 3. A numerical analysis of the imperfect member at the given temperature was performed to determine its resistance, by increasing the applied load.
The numerical analyses were performed with the 3D beam and shell thermomechanical finite elements presented in Possidente et al. (2019, 2020b). The elasto-plastic behaviour of steel was modelled based on the Von Mises yield function and on the uniaxial stress-strain relationship given in EN 1993-1-2. Residual stresses were neglected since it was found that their effect on the resistance of steel member in fire is not significant (Franssen et al., 1995; Vila Real et al., 2004a; Ranawaka and Mahendran, 2010; Quiel and Garlock, 2010; Couto et al., 2015). The Young's modulus value at ambient temperature was set to 210 GPa, and the Poisson ratio was equal to 0.3. Monosymmetric sections (L and T sections) were investigated by means of the 3D beam finite elements developed in Possidente et al. (2020b), whereas for the X sections the shell element proposed in Possidente et al. (2019) was employed. Indeed, shell elements were used as the introduction of imperfections associated to a pure torsional buckling would not be possible in beam elements-based analyses. However, beam elements were preferred for the monosymmetric cross-sections since they enable faster analyses and an easier definition of the boundary conditions, allowing for the investigation of simply supported columns with the rotational degree of freedom along the longitudinal axis blocked. Instead, columns with clamped end conditions were analysed when shell elements were used. The lateral displacements were blocked only at the centroids of the two clamped ends, to allow for thermal expansion. The axial displacement was fixed on one end and free conditions were imposed at the opposite end, which was loaded. The axial load was applied to the centroid and master-slave constraints allowed for a uniform axial displacement of all the other nodes of the loaded end. According to preliminary convergence analyses, 30 elements were sufficient for accurate solutions for beam models, while in the shell-based simulation it was necessary to vary the mesh with the length of the column. A minimum of six elements in each dimension of the section were always used.
The 3D beam and shell thermomechanical finite elements presented in Possidente et al. (2019, 2020b) were employed in the numerical analyses since they have been shown to provide accurate and reliable results and are well-suited for the purpose of the analyses. In particular, the 3D beam element was specifically conceived to properly consider torsion and warping in thin-walled elements with open cross-section at elevated temperature. In addition, the ability of these elements to capture flexural-torsional buckling was numerically validated in Possidente et al. (2020a), since no experimental tests were available in literature. The beam and shell elements gave comparable results for the buckling mode identification and the associated buckling load evaluation of members prone to flexural-torsional buckling. Excellent agreement was found in the analyses at elevated temperature with initial imperfections, determined by scaling the identified buckling modes. In addition, according to the procedure proposed in Jönsson and Stan (2017), it was also proved that the numerical framework can reproduce the flexural buckling curves at ambient temperature from the EN 1993-1-1 (CEN (European Committee for Standardisation), 2005a) by applying an equivalent lateral initial imperfection
3.2 Considerations about the numerical results
The outcomes of the analyses are compared against the buckling curves from the European and American standards, i.e. the reduction factors of the full resistance to compression at elevated temperature
It should be observed that, though
In Figure 3 the results are presented for the T sections consisting of half H or half I only since a comparison with the EN 1993-1-2 for the remaining sections was already proposed in Possidente et al. (2020a). Instead, the numerical results are shown for all the cross-sections in Figure 4, in which the outcomes of the analyses are compared with the AISC 360-16 curve. The buckling curves are expressed with respect to the pure flexural buckling slenderness, allowing for a better representation of the length of the member and improved predictions (Popovic et al., 2001; Possidente et al., 2020a; Taras and Greiner, 2007). From the figures, it can be observed that the design buckling curves from the European and American norms give inaccurate results and over- or underestimate the
In almost all the analyses, the X sections buckled in their pure flexural form. Moreover, few very stocky columns attained failure loads higher than the yielding load
For T sections consisting of half hot-rolled H or I profiles, numerical results are more spread compared with the ones of the other sections (Figures 3 and 4e). This is mainly because these sections have very different geometric dimension, especially when it comes to the depth-to-thickness ratio of the flanges and of the web. Moreover, in some cases, the strong axis of the section is directed along the web, but in the others, it has the same orientation of the flanges. This is not the case for T sections made of coupled L profiles. Indeed, coupling equal leg profiles the strong axis is always directed along the web. A further difference consists in the fact that for T sections consisting of coupled L profiles the web thickness is always two times the flange thickness, while for sections obtained from H- or I-profiles the web thickness is smaller than the flange thickness. For these sections, the actual buckling curves are both conservative and non-conservative. However, since it seems difficult to achieve very dense predictions in this case, buckling curves mainly on the safe side should be preferred.
4. New buckling curve proposals
Buckling curves that allow for a better representation of the results of numerical simulation were developed. The first proposal is based on the curves prescribed in EN 1993-1-2. Its formulation was already described in Possidente et al. (2020a) and is briefly summarised in the following paragraph. A second proposal was developed in this work starting from the equation provided in the AISC 360-16 norm. The predictions obtained with the proposals are compared with the ones from the original curves.
4.1 Modified EN 1993-1-2 buckling curve
To improve the buckling curve formulation from EN 1993-1-2, the generalised imperfection factor
The new generalised imperfection factor
The values of
The proposed buckling curves were compared with the numerical results and the EN 1993-1-2 buckling curve for T sections consisting of half hot-rolled H or I profiles in Figure 3. The results for the other section types can be found in Possidente et al. (2020a). Predictions from the proposal are safer and the introduction of a plateau
4.2 Modified AISC 360-16 buckling curve
Analogously to the previous proposal, another curve was developed modifying the parameters of the original AISC 360-16 curve. In this case, the modifications are applied to the imperfection factor
Like the parameter
Due to the introduction of a plateau, the following limits of validity are defined
Since
In Figure 4 the curves described by the parameters from Table 7 were compared with numerical results and the AISC 360-16 buckling curves. The modified curve is safer and gives a better representation of the numerical outcomes compared to the original one.
4.3 Imperfection factors analysis
In order to provide safe predictions, additional checks on the
The numerical generalised imperfection factor
Substituting the reduction factor at elevated temperature
Similarly, the numerical imperfection factor for the AISC curve formulation
In Figure 5 the evolution as a function of the slenderness of the generalised imperfection factor
In Figure 5, the generalised imperfection factor
4.4 Statistical analysis
The degree of safety of the buckling curves was assessed by comparison with the results from numerical simulation. For each non-dimensional slenderness
It should be observed that the AISC 360-16 design curve always provides better and safer results than the EN 1993-1-2 curve. This can be explained by the fact that Takagi and Deierlein (2007) developed the curve implemented in the AISC 360-16 standard based on numerical and experimental results, regardless from the existing formulations at ambient temperature. Conversely, the EN 1993-1-2 curve was derived fitting numerical and experimental results in the framework of the curve for ambient temperature from EN 1993-1-1 (CEN (European Committee for Standardisation), 2005a). Moreover, the curve by Takagi and Deierlein (2007) seems to be calibrated on the lowest numerical values of resistance collected in their analyses, whereas in EN 1993-1-2 parameters were calibrated so that only 50% of the numerical outcomes were higher than the buckling curve predictions. Hence, the AISC 360-16 buckling curve better captures the numerical outcomes and is safer for the flexural buckling situation, as clearly confirmed for X sections in Figure 6c. From this standpoint, it seems reasonable to expect better predictions from the AISC 360-16 curve also when flexural-torsional and torsional buckling are involved.
5. Conclusions
In this paper, fire buckling curves for the prediction of the resistance of compressed hot-rolled steel L profiles or closely spaced built-up members at elevated temperature were proposed. These curves consider the flexural and flexural-torsional behaviour in fire situation, which seems to be ignored in the current provisions of the European and the American standards, namely EN 1993-1-2 (CEN (European Committee for Standardisation), 2005b) and AISC 360-16 (AISC American Institute of Steel Construction, 2016). Moreover, though the profiles investigated in this work are widely used in the design practice, very few fundamental studies can be found in the literature. Indeed, the scientific community mainly focused on flexural and flexural-torsional behaviour of cold-formed steel members and rarely at elevated temperatures, while such a behaviour in the fire situation was not investigated for hot-rolled or welded profiles. To propose accurate and safe buckling curves, the behaviour of concentrically compressed L, T and X sections was investigated numerically in a parametric study consisting of more than 41,000 GMNIA analyses. Numerical analyses were performed on members with a uniform temperature distribution in the 400–800 C range, since this is usually the most relevant range for steel members in fire situation. Class 1 to class 3 members according to the classification of EN 1993-1-2 and non-slender elements according to AISC 360-16 were selected to study elements that are not sensitive to local buckling. It was found that flexural and flexural-torsional buckling affects the resistance of the investigated sections at elevated temperature, notably in the low slenderness range. The buckling curves were expressed with respect to the pure flexural buckling slenderness, allowing for a better representation of the length of the member and improved predictions. Compared with numerical outcomes, the actual provisions of the European and the American norms lead to both conservative and unconservative predictions. Two new buckling curves were proposed by modifying the formulation of the EN 1993-1-2 and the AISC 360-16 curves, respectively. The proposed factors depend on three parameters each, which were calibrated for each investigated cross-section shape. Both the proposals were proved to be safer and more accurate than the original curves. A statistical investigation was performed assuming a normal distribution, and probabilities of safe predictions higher than 94% for the modified EN 1993-1-2 curve, and higher of 95% for the modified AISC 360-16 curve were reached. For T sections made of half an H or I section, the proposals were less accurate, but still safer and more reliable than the original curves. In conclusion, it was demonstrated that buckling curves that better account for flexural-torsional and torsional buckling can be obtained with simple modifications of the buckling curves implemented in the current European and American norms.
Figures
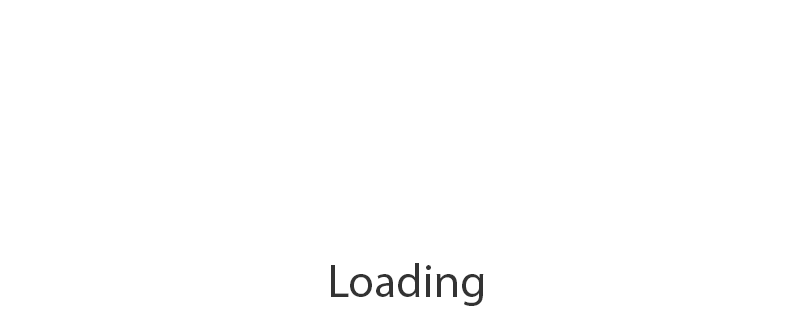
Figure 3
Buckling curves for T sections obtained from half H or I section (L, T and X made of coupled leg sections can be found in Possidente et al. (2020)). S235, S275 and S355 steel grade
Equivalent design quantities in EN-1993-1-2 and AISC 360-16
EN-1993-1-2 | AISC 360-16 |
---|---|
Φc | |
Performed analyses
Section type | N. of sections | N. of analyses* |
---|---|---|
L sections (equal leg L) | 45 | 7,695 |
T sections (2 equal leg L) | 45 | 7,397 |
X sections (4 equal leg L) | 45 | 3,729 |
T sections (2 unequal leg L) | 23 | 2,392 |
T sections (half H or I) | 129 | 19,803 |
Sum | 287 | 41,016 |
Average number of analyses for each of the 5 temperatures | 8,203 |
Note(s): *Numerical analyses with convergence problems were discarded. Only the considered analyses are reported here
Investigated sections
![]() |
Generalised imperfection factors
Note(s): EN 1993-1-2 and associated proposal for modification
Selected values for the parameters of the proposed buckling curve
L | T (2 equal leg L) | T (2 unequal leg L) | T (half H or I) | X (4 equal leg L) | |
---|---|---|---|---|---|
1.00 | 1.25 | 1.10 | 1.50 | 0.85 | |
0.50 | 0.80 | 0.50 | 0.50 | 0.35 | |
0.15 | 0.22 | 0.20 | 0.18 | 0.20 |
Note(s): AISC 360-16 and associated proposal for modification
Selected values for the parameters of the proposed buckling curve
L | T (2 equal leg L) | T (2 unequal leg L) | T (half H or I) | X (4 equal leg L) | |
---|---|---|---|---|---|
0.34 | 0.30 | 0.33 | 0.27 | 0.34 | |
−0.24 | −0.38 | −0.25 | −0.42 | −0.20 | |
0.11 | 0.14 | 0.12 | 0.16 | 0.20 |
References
AISC (American Institute of Steel Construction) (2016), Specification for Structural Steel Buildings, American Institute of Steel Construction, Chicago, IL.
Arrais, F., Lopes, N. and Vila Real, P. (2021), “Fire behaviour and resistance of cold-formed steel beams with sigma cross-sections”, Journal of Structural Fire Engineering, Vol. 12 No. 4, doi: 10.1108/JSFE-11-2020-0037.
Ayrton, W.E. and Penny, J. (1886), “On struts”, The Engineer, Vol. 62, p. 464.
Bailey, C.G., Burgess, I.W. and Plank, R.J. (1996), “The lateral-torsional buckling of unrestrained steel beams in fire”, Journal of Constructional Steel Research, Vol. 36, pp. 101-119.
CEN (European Committee for Standardisation) (2005a), Eurocode 3 Design of Steel Structures – Part 1-1: General Rules and Rules for Building, European Committee for Standardisation, Brussels.
CEN (European Committee for Standardisation) (2005b), Eurocode 3 Design of Steel Structures – Part 1-2: General Rules – Structural Fire Design, European Committee for Standardisation, Brussels.
Chen, G. and Trahair, N.S. (2006), “Inelastic torsional buckling strengths of cruciform columns”, Engineering Structures, Vol. 16, pp. 83-90.
Couto, C., Vila Real, P., Lopes, N. and Zhao, B. (2014), “Effective width method to account for the local buckling of steel thin plates at elevated temperatures”, Thin-Walled Structures, Vol. 84, pp. 134-149, doi: 10.1016/j.tws.2014.06.003.
Couto, C., Vila Real, P., Lopes, N. and Zhao, B. (2015), “Resistance of steel cross-sections with local buckling at elevated temperatures”, Journal of Constructional Steel Research, Vol. 109, pp. 101-114, doi: 10.1016/j.jcsr.2015.03.005.
Couto, C., Vila Real, P., Lopes, N. and Zhao, B. (2016), “Numerical investigation of the lateral-torsional buckling of beams with slender cross section for the case of fire”, Engineering Structures, Vol. 106, pp. 410-421.
Couto, C., Maia, É., Vila Real, P. and Lopes, N. (2018), “The effect of non-uniform bending on the lateral stability of steel beams with slender cross-section at elevated temperatures”, Engineering Structures, Vol. 163, pp. 153-166, doi: 10.1016/j.engstruct.2018.02.033.
Craveiro, H., Rodrigues, J.P.C. and Laim, L. (2018), “Cold-formed steel columns at both ambient and fire conditions”, Journal of Structural Fire Engineering, Vol. 9, pp. 189-202, doi: 10.1108/JSFE-01-2017-0018.
Dabrowski, R. (1988), “On torsional stability of cruciform columns”, Journal of Constructional Steel Research, Vol. 9, pp. 51-59.
Dinis, P.B., Camotim, D. and Silvestre, N. (2010), “On the local and global buckling behavior of angle, T-section and cruciform thin-walled members”, Thin-Walled Structures, Vol. 48, pp. 786-797.
Franssen, J.-M., Morente, F., Vila Real, P., Wald, F., Sanzel, A. and Zhao, B. (2016), Fire Design of Steel Members with Welded or Hot-Rolled Class 4 Cross-Sections (FIDESC4), Final Report, EU Publications, Luxembourg.
Franssen, J.-M., Schleich, J.-B. and Cajot, L.-G. (1995), “A simple model for the fire resistance of axially-loaded members according to Eurocode 3”, Journal of Constructional Steel Research, Vol. 35, pp. 49-69, doi: 10.1016/0143-974X(94)00042-D.
Jönsson, J. and Stan, T.-C. (2017), “European column buckling curves and finite element modelling including high strength steels”, Journal of Constructional Steel Research, Vol. 128, pp. 136-151, doi: 10.1016/j.jcsr.2016.08.013.
Laím, L. and Rodrigues, J.P.C. (2018), “Fire design methodologies for cold-formed steel beams made with open and closed cross-sections”, Engineering Structures, Vol. 171, pp. 759-778, doi: 10.1016/j.engstruct.2018.06.030.
Popovic, D., Hancock, G.J. and Rasmussen, K.J.R. (2001), “Compression tests on cold-formed angles loaded parallel with a leg”, Journal of Structural Engineering, Vol. 127, pp. 600-607.
Possidente, L., Tondini, N. and Battini, J.-M. (2019), “Branch-switching procedure for post-buckling analysis of thin-walled steel members at elevated temperature”, Thin-Walled Structures, Vol. 136, pp. 90-98, doi: 10.1016/j.tws.2018.12.012.
Possidente, L., Weiss, A., de Silva, D., Pustorino, S., Nigro, E. and Tondini, N. (2020), “Fire safety engineering principles applied to a multi-storey steel building”, Proceedings of the Institution of Civil Engineers – Structures and Buildings. doi: 10.1680/jstbu.20.00110.
Possidente, L., Tondini, N. and Battini, J.-M. (2020a), “Torsional and flexural-torsional buckling of compressed steel members in fire”, Journal of Constructional Steel Research, Vol. 171, 106130, doi: 10.1016/j.jcsr.2020.106130.
Possidente, L., Tondini, N. and Battini, J.-M. (2020b), “3D beam element for the analysis of torsional problems of steel-structures in fire”, Journal of Structural Engineering, Vol. 146, 04020125, doi: 10.1061/(ASCE)ST.1943-541X.0002665.
Prachar, M., Jandera, M., Wald, F. and Zhao, B. (2015), “Lateral torsional-buckling of class 4 steel plate beams at elevated temperature: experimental and numerical comparison”, Journal of Structural Fire Engineering, Vol. 6, pp. 223-235, doi: 10.1260/2040-2317.6.3.223.
Quiel, S.E. and Garlock, M.E.M. (2010), “Calculating the buckling strength of steel plates exposed to fire”, Thin-Walled Structures, Vol. 48, pp. 684-695, doi: 10.1016/j.tws.2010.04.001.
Ranawaka, T. and Mahendran, M. (2010), “Numerical modelling of light gauge cold-formed steel compression members subjected to distortional buckling at elevated temperatures”, Thin-Walled Structures, Vol. 48, pp. 334-344, doi: 10.1016/j.tws.2009.11.004.
Schafer, B.W. (2008), “Review: the direct strength method of cold-formed steel member design”, Journal of Constructional Steel Research, Vol. 64, pp. 766-778, doi: 10.1016/j.jcsr.2008.01.022.
Silvestre, N., Dinis, P.B. and Camotim, D. (2013), “Developments on the design of cold-formed steel angels”, Journal of Structural Steel Research, Vol. 139, pp. 680-694.
Takagi, J. and Deierlein, G.G. (2007), “Strength design criteria for steel members at elevated temperatures”, Journal of Constructional Steel Research, Vol. 63, pp. 1036-1050.
Taras, A. and Greiner, R. (2007), “Torsional and flexural torsional buckling – a study on laterally restrained I-sections”, Journal of Constructional Steel Research, Vol. 64, pp. 725-731.
Trahair, N.S. (2012), “Strength design of cruciform steel columns”, Engineering Structures, Vol. 35, pp. 307-313, doi: 10.1016/j.engstruct.2011.11.026.
Vila Real, P. and Franssen, J.-M. (2000), “Lateral torsional buckling of steel -beams in case of fire – numerical modelling”, Presented at the First International Workshop Structures in Fire, Copenhagen.
Vila Real, P., Cazeli, R., Simões da Silva, L., Santiago, A. and Piloto, P. (2004a), “The effect of residual stresses in the lateral-torsional buckling of steel I-beams at elevated temperature”, Journal of Constructional Steel Research, Vol. 60, pp. 783-793, doi: 10.1016/S0143-974X(03)00143-3.
Vila Real, P., Lopes, N., da Silva, L.S. and Franssen, J.-M. (2004b), “Lateral-torsional buckling of unrestrained steel beams under fire conditions: improvement of EC3 proposal”, Computers and Structures, Vol. 82, pp. 1737-1744.
Acknowledgements
The authors acknowledge funding from the Italian Ministry of Education, University and Research (MIUR) in the frame of the Departments of Excellence Initiative 2018-2022 attributed to DICAM of the University of Trento.