Abstract
Purpose
Maintenance policy is an element of building maintenance management that deals with organisation policy, planning and procedures, and delineates how maintenance units in an organisation will manage specific building components, auxiliary facilities and services. Given this contextual setting, this study investigates whether organisational maintenance policies (OMPs) utilised in developed countries are relevant in developing countries – using Nigeria as a case study exemplar.
Design/methodology/approach
An empirical research design (using deductive reasoning) was implemented for this research. Specifically, a Delphi study conducted revealed 23 elements that impact OMP development in Nigeria.
Findings
Of these twenty elements, six had a very high impact on maintenance management (VHI: 9.00–10.00), nine variables had a high impact (HI: 7.00–8.99) and eight other variables scored a medium impact (MI: 5.00–6.99). Emergent findings reveal that the elements of organisational maintenance policy that engender effective building maintenance management include preparation of safety procedure, optimisation of the maintenance policy, optimisation of the maintenance action plan, well-defined priority system, risk factor establishment, suitable maintenance procedures and a clearly delineated process.
Practical implications
The study findings will guide policymakers in identifying the main elements required in maintenance policies development towards making national public asset preservation and economic gains. Also, the content of the future educational curriculum on maintenance management study will be more receptive to the body of knowledge and the built environment industry.
Originality/value
Cumulatively, the research presented illustrates that these elements replicate those adopted in other countries and that effective maintenance management of public buildings is assured when these elements are integral to the development of an OMP.
Keywords
Citation
Ogunbayo, B.F., Aigbavboa, C.O., Thwala, W.D., Akinradewo, O.I. and Edwards, D. (2023), "Validating elements of organisational maintenance policy for maintenance management of public buildings in Nigeria", Journal of Quality in Maintenance Engineering, Vol. 29 No. 5, pp. 16-36. https://doi.org/10.1108/JQME-05-2021-0039
Publisher
:Emerald Publishing Limited
Copyright © 2020, Babatunde Fatai Ogunbayo, Clinton Ohis Aigbavboa, Wellington Didibhuku Thwala, Opeoluwa Israel Akinradewo and David Edwards
License
Published by Emerald Publishing Limited. This article is published under the Creative Commons Attribution (CC BY 4.0) licence. Anyone may reproduce, distribute, translate and create derivative works of this article (for both commercial and non-commercial purposes), subject to full attribution to the original publication and authors. The full terms of this licence may be seen at http://creativecommons.org/licences/by/4.0/legalcode
1. Introduction
According to Oke (2005) building maintenance is a major contributor to the profitability and performance of business organisations. Crespo et al. (2009), defines maintenance as consisting of a combination of all technical, management and administrative engagements actions carried out to retain an item in (or to restore it to) an acceptable standard. Seeley (1996), Swanson (2001), Duffuaa et al. (1999) and Ogunbayo and Aigbavboa (2019) asserted that overall maintenance activities can be defined as a combination of all actions intended to retain a building in functional working order.
Conventionally, maintenance has been perceived as an expense account with performance measures developed to track direct costs such as the total duration of forced outages during a specified period (Ding and Kamaruddin, 2015; Ogunbayo et al., 2022). According to Cobbinah (2010) a vibrant maintenance management (MM) system together with experienced and skilful staff can: prevent environmental damage and health safety issues; lower operating costs; increase asset life with fewer breakdowns; and augment quality of life for the users of maintained assets. Given these palpable benefits, Mobley (2002) and Ogunbayo et al. (2018) posit that maintenance organisations must therefore perform maintenance on public buildings. For this present study, public buildings are used by the public for any purpose, such as assembly, transportation, civic, sport, education, entertainment, residence, and worship. Hence, an optimised and appropriate maintenance policy is required by maintenance organisations in achieving all related maintenance activities to save public finances and boost the life span of buildings being maintained. In this study, MM is proxied by a number of variables – namely, maintenance budget; continuous improvement; human resources management; outsource strategy; spare part management; maintenance approach; computerised MM system; task planning; and scheduling, monitoring and controlling benchmarks against a well-organised building and facility organisations in the Nigerian built environment industry (cf. Campbell, 1995; Takata et al., 2004; Ahzahar et al., 2011; Irajpour et al., 2014; Omar et al., 2016). Conversely, organisational maintenance policy (OMP) is defined by BS 3811 (2001) as a strategy through which maintenance decisions are taken. An OMP is developed based on maintenance organisation objectives, available resources, and capabilities (Parida and Kumar, 2009). The policy is concerned with the development of a decision support approach, which is operational for designing maintenance strategies for complex maintenance systems (Ben-Daya et al., 2009). Hence, in this present study OMP encapsulates all activities which describe how maintenance units in an organisation will manage a building's specific components, auxiliary facilities, and services. These activities include suitable maintenance procedure and process; assembling of maintenance; meeting maintenance objectives; and all other activities undertaken by a maintenance organisation that deals with organisation policy, planning and procedures. This contextual definition of OMP is consistent with the definitions found in earlier studies such as Vanneste and Van Wassenhove (1995), Campbell (1998), Cholasuke et al. (2004), Ali (2009), and Lind and Muyingo (2012). According to Oberschmidt et al. (2010), a well-defined OMP ensures optimal building performance.
Although OMP is an essential tool in achieving organised and systematic planning of maintenance work (such as the MM of public buildings), there is a discernible lack of research that delineates OMP for the MM of Nigerian public buildings (Duffuaa et al., 1999). Thus, this study seeks to establish whether the elements of OMP found in other countries are relevant in the maintenance of Nigerian public buildings. Notably, the inherent elements of OMP are organisational, industry and country exact. Hence, depending on the prevalent organisational system and national macroeconomic factors for a specific country (i.e. social, economic, political and legislative), different forms of information may or may not be relevant in OMP development (Ding and Kamaruddin, 2015). Premised upon this observation, it would be presumptuous (indeed, erroneous) to assume elements of OMP are generic and applicable to all maintenance organisations, industries, and nations. Nonetheless, some organisations, industries or countries internationally may share some resemblance with Nigeria. Thus, empirically ascertaining the elements of OMP that influence MM of Nigerian public buildings is essential. Consequently, this study seeks to determine which of the OMP elements influence MM of Nigerian public buildings, and to what extent is the influence. This research is intended to inform the development of an adequate maintenance policy for the Nigerian built environment as a means of improving the maintenance system of infrastructure. For this present research, the built environment industry includes professionally inclined institutions or bodies who are responsible for the construction, management, and maintenance of the public buildings. These include the: Nigerian Institute of Building (NIOB); Nigeria Institute of Quantity Surveyors (NIQS); Nigeria Institute of Architects (NIA); Nigeria Society of Engineers (NSE); Nigeria Institute of Estate Surveyors and Valuer (NIESV); Federation of Building and Civil Engineering Contractors (FBCE); and Real Estate Developers Association of Nigeria (REDAN). This definition is consistent with the provisions of Federal Republic of Nigeria Public Procurement Act (2007) and Federal Republic of Nigeria National Building Code (2006).
2. OMP attributes: relevant survey of existing literature
Maintenance policy is a tool through which maintenance organisations achieve an effective MM process for maintained buildings (Oke and Charles-Owaba, 2006). It also provides guidance for decision-making in maintenance organisations that links the formulation of strategy with implementation (Pinjala et al., 2006). Márquez (2007) and Pintelon and Muchiri (2009) state that maintenance policies are essential tactical level decisions because they outline the rules for triggering maintenance actions. Olanrewaju and Abdul-Aziz (2015) notes that maintenance organisations use OMP to guide their personnel to make decisions and to ensure that building facilities are well maintained to benchmark standards. Wang (2002) states that researchers define OMP in several ways and from different perspectives because of the importance of running a proper maintenance process for bespoke buildings; this was supported by Faghihinia and Mollaverdi (2012) who highlighted different OMP attributes or elements. These elements are more like strategies or guidelines for maintenance decisions (Faghihinia and Mollaverdi, 2012). Nonetheless, OMP is reviewed periodically because it is neither dynamic nor static and depends upon changes both within and outside maintenance organisations (Al-Najjar and Alsyouf, 2004). Through different elements as identified by researchers, maintenance organisations explore every opportunity to improve on OMP toward profitability and performance. Nevertheless, regards explicit elements that constitute OMP, researchers have expressed diverse views which vary depending upon the organisation's business strategy and preventive maintenance design optimisation (Wireman, 2005). Studies by Campbell (1998) and Wireman (2005), and later affirmed by Pintelon and Muchiri (2009), illustrate that element of OMP includes: preparation of maintenance operation; suitable maintenance procedures and processes; assembling of maintenance organisation structure; organisation operational efficiency; preparation of safety procedure; risk factor establishment; and target performance measurement. Tsang (2002) states that in designing organisational OMP external resources must be considered that include: preparing maintenance operation guidance; analysing maintenance procedures; producing an appropriate procurement strategy; creating a suitable spare part management regime; analysing data collected; and understanding the procedures suitable for maintenance processes. Visser (1998) identified the following elements as significant in the development of OMP, namely, establishment of risk factors; development of appropriate maintenance procedures and processes; assembly of maintenance organisation structure; analysis of maintenance procedures; preparation of maintenance operation; and preparation of safety procedures. Lind and Muyingo (2012) and Karia et al. (2014) suggest that significant elements of OMP include: managing spare parts; meeting maintenance objectives; optimising maintenance policy; creating appropriate procurement strategy; changing policy and its associated results; and working together with regulatory agencies.
Pinjala et al. (2006) showed that a maintenance organisation's maintenance policy is a basic constituent part of the maintenance management function (MMF) and it includes elements such as a: well-defined priority system; suitable procurement strategy; change in policy, and its associated results in the maintenance process; better understanding of the regulatory agencies procedure; suitable maintenance contract(s); timely identification of maintenance work; reduction in the meantime to repair; and design and optimisation of the preventive plan. Sherwin (2000) and HajShirmohammadi and Wedley (2004) hypothesised that an element of OMP for effectiveness must include the following: establishment of risk factors; target performance measurement; reutilisation of techniques; development of maintenance strategies; management of available spare-parts; better understanding of maintenance objectives; optimisation of the maintenance policy; optimisation of the maintenance action plan; and a clear priority system and suitable procurement strategy. Atkin (2003) suggests that the element of OMP must include the maintenance objective, that is, what maintenance has to achieve. The elements of a maintenance policy include: information feedback; maintenance programs; maintenance budget; prevention of defects; means of effecting maintenance; standards of care; and use of premises (Atkin, 2003; Pintelon and Muchiri, 2009). Fatokun (1997) proffers that elements of OMP will include: setting out in clear terms the parameters of maintenance standard desired; laying down broad approaches to executing maintenance works; identifying categories of work to be classified under varying maintenance types; instituting the internal feedback system; and sourcing or method of funding maintenance works.
2.1 Theoretical background
In explaining the elements of OMP, MM models as developed by both Campbell (1995) and Wireman (2005) were employed. Campbell (1995) conceptualised effective MM as a four-tiered conceptual construct (refer to Figure 1), namely, (1) strategy development for each asset with a business plan fully integrated; (2) organisation control of each asset functionality throughout its life cycles; (3) application of effective maintenance methodologies (TPM/RCM) with intention of achieving continuous improvement; and (4) maintenance re-engineering to sustain achieved improved process.
Wireman (2005) advanced this earlier theory and stated a five-tiered construct (refer to Figure 2), namely, (1) establishment of preventive maintenance program; (2) maintenance resources management; (3) personnel role/involvement in the maintenance program (predictive/RCM) implementation; (4) routinise the use of optimisation techniques; and (5) continuous improvement through assessment of the process.
An OMP derived from both models will guide a maintenance organisation to strategically position themselves to employ effective MM within its buildings (Campbell, 1995; Wireman, 2005; Marquez and Gupta, 2006; Márquez, 2007; Alzaben, 2015). Moreover, the strength of both the strategic based maintenance policy (Campbell, 1995) and preventive-based maintenance policy (Edwards et al., 1998; Wireman, 2005) varies between both organisations and industrial sectors. Similarly, the combined strength of both models defines the action plans and a necessary platform for measuring the achievement of goals and operational efficiencies within the maintenance organisation (Visser, 1998; Pintelon and Muchiri, 2009). However, the MM process and framework as advance by Márquez (2007) (see Table 1), cautioned that in a maintenance organisation where both strategic and preventive base maintenance policies are used, the process and framework for policy implementation must be defined. Márquez (2007) stated that the MM process must consist of the various tasks that must be accomplished on a daily basis, while the MM framework will provide distinct technological support to the process as envisaged to manage maintenance activities.
From the aforementioned literature reviewed it can be deduced that researchers concur that OMP influences effective MM of buildings (Sherwin, 2000; Lind and Muyingo, 2012; Pintelon and Muchiri, 2009). Nevertheless, there are varying views as to the specific elements that constitute OMP. It was also inferred that some views raised are also closely related which indicates a scientifically grounded consensus in the developed models. Thus, this study provides a holistic framework that synthesises the different models. The elements of the OMP theoretical concept that guided the current study are detailed in Table 2.
3. Research methodology
3.1 Research approach
In affirming the elements of OMP for the MM of public buildings in Nigeria, this study employed an empirical research design (cf. Sing et al., 2021; Ahmed et al., 2021) and deductive reasoning (Edwards et al., 2019; Aghimien et al., 2020). This methodological approach has been extensively used within contemporary construction management literature to, for example: conduct a post occupancy evaluation (GTbPOE) of dormitory building performance (Hou et al., 2020); estimate on-site emissions during ready mixed concrete (RMC) delivery on construction sites (Olanrewaju et al., 2020); and measure hand-arm vibration exposure in the UK utilities sector (Edwards et al., 2020). This body of knowledge demonstrates that the approach adopted in this present study provides a robust epistemological approach that will yield reliable results. From an operational perspective, the Delphi technique was employed to gather and analyse primary data. According to Miller (1993), Rowe and Wright (2001); Fletcher and Marchildon (2014) and Somiah et al. (2020), Delphi applies to both qualitative and quantitative studies and includes the use of structured questionnaires to solicit the views from expert panellists, through iterative rounds until saturation occurs at which point, participants converge on the correct (and most accurate) response (Leung, 2001). Somiah et al. (2020) state that the use of the Delphi technique is a suitably robust and effective tool for capturing essential data in qualitative studies (also refer to Leung, 2001; Aigbavboa, 2014). Consequently, this quantitative study employed and adapted the detailed Delphi process as delineated in Figure 3.
3.2 Target population and selection criteria
Relevant literature was first reviewed to identify relevant elements of OMP that influenced MM of buildings. Experts were then selected to represent a broad spectrum of opinions on the phenomenon under investigation (Loo, 2002; Tilakasiri, 2015; Somiah et al., 2020). Specifically, practically experienced participants who exhibited adequate theoretical knowledge of building maintenance works were drawn from both academia and industry (cf. Aigbavboa, 2014). Hence, the purposive non-probability sampling was adopted to select individuals based on the researcher's knowledge and experience, and desirable characteristics of respondents (Ogunbayo et al., 2021). To formalise the process of sample selection, a prequalification checklist process was developed (refer to Addendum 1). Initially, twenty-five (25) experts were approached through separate e-mails to participate in the Delphi survey. This email included a brief background to the survey together with pertinent ethical considerations to assure strict confidentiality and anonymity, data protection and informed consent (Fisher et al., 2018).
After round two, the Delphi process ended once the range of replies given decreased as the participants converged onto broad consensus. As postulated by Somiah et al. (2020) and Tengan and Aigbavboa (2021) the sample size in the Delphi study is not reliant on a statistical sample most especially as a representation of a population; but depends on bringing together experts on the area of study to share their experience and knowledge until consensus is reached. Based on this notion, the homogenous sample size of fifteen experts was considered appropriate and used for this study. This sample size being deemed adequate in previous studies that recommend that 10–15 participants provide adequate coverage (cf. Aigbavboa, 2014; Somiah et al., 2020).
Questionnaires and instructions for round one and later round two, were then distributed to the fifteen experts' panellists selected (See Appendices 2 and 3).
3.3 Data collection instrument design and analysis method
Using literature as a basis, a structured Delphi questionnaire (Ameyaw et al., 2016) was developed and tested via a pilot study using five members of different built environment industry. They belong to professionally inclined institutions or bodies who are responsible for the construction, management, and maintenance of the public buildings to test for completion period, clarity, lucidity and completeness. Feedback from the pilot study was incorporated into the questionnaire which was subsequently administered. Similarly, a relative importance index (RII) was employed in determining and analysing consensus in experts' responses (Aigbavboa, 2014; Adnan et al., 2018; and Somiah et al., 2020; Tengan and Aigbavboa, 2021). Consensus was measured using:
Strong consensus – median 9–10, relative impact index 0.80–1.00, interquartile deviation (IQD) ≤ 1;
Good consensus – median 7–8.99, relative impact index 0.60–0.79, IQD≥1, 1 ≤ 2; and
Weak consensus – median ≤6.99, relative impact index ≤0.59 and IQD≥2, 1 ≤ 3.
Which is based on a 10-points impact scale where: 1 to 2 denote no impact; 3 to 4 denote low impact; 5 to 6 denote medium impact; 7 to 8 denote high impact; and 10 denote very high impact. Sarantakos (2005), Tengan and Aigbavboa (2021) and Somiah et al. (2020) in their studies emphasised that Delphi findings are grounded on all-encompassing theoretical reasoning coupled with the rigorousness of the collection process of data. Based on this statement, this study adopted a rigorous methodological process (refer to Figure 4); and additionally, the study was underpinned by the: (1) MM model reported upon by Campbell (1995) and Wireman (2005); and (2) MM process and framework elucidated upon by Márquez (2007). Through persistent individual communication with experts and the chance to freely effect changes or maintain their response based on good reasons for the latter, internal validity for the study was affirmed. During the Delphi survey process at each round, an estimated statistical view of the experts' through the use of interquartile deviation, standard deviation, median and mean was calculated and analysed.
4. Results
4.1 Demographic information result
Nonetheless, in both one and two rounds of the survey, only fifteen (15) experts participated whose demographic profile is reported upon in Table 3. Summary analysis reveals that: 46.67% of the participating experts were lecturers; 40% were maintenance managers of public buildings; while 23.33% were professional/research institutions of buildings. All participants were members of a professional institute in the built environment industry in Nigeria, with a bachelor's degree as the minimum education level attained. Moreover, all participants had > five years of experience, where: 6.67% had 6–10 years of experience; 60% had 11–20 years of experience; 20% had 21–30 years of experience; while 13.33% had over 31 years of working experience in the Nigerian built environment industry. In respect of the demographic profile to the checklist for experts' selected (see Appendix 1), it indicated that for the educational level the minimum attained mark was 2 (Bachelor degree). While a minimum of 1 point was obtained by all the experts because of their membership to a professional association, whereas 2 points (6–10) were obtained for the year of experience. Similarly, for this study, before becoming part of the panel a minimum of 5 points was the prerequisite point for an expert (see Appendix 1). This was obtained by all the experts for this study. Thus, all the experts selected for the Delphi study were deemed fit for the study.
4.2 Round one result of Delphi study
The Delphi Survey round sought to establish the elements of OMP that influence MM of public buildings in the Nigerian built industry. Twenty (20) elements of OMP that were identified from extant literature were validated by the panellists to have influenced the MM of public buildings in Nigeria. To further augment the survey, panellists were given chance to recommend new elements that may not be included in the questionnaire. Out of the twenty elements, six (6) had a very high impact on MM (VHI: 9.00–10.00) which are: “preparation of safety procedure”, “optimization of the maintenance policy’, “optimization of the maintenance action plan”, “well-defined priority system”, “risk factor establishment” and “suitable maintenance procedures and process” while seven (7) variables had a high impact (HI: 7.00–8.99) which are: “assembling of maintenance organization structure”, “change in policy and its associated results”, “preparation of maintenance operation”, “organization operational efficiency”, “appropriate procurement strategy”, “maintenance strategies development”, and “meeting maintenance objectives” and seven (7) other variables scored a medium impact (MI: 5.00–6.99) which are: “target performance measurement”, “spare-part management”, “timely identification of maintenance work”, “maintenance contracts suitability”,“routinisation of optimization techniques”, “reduction in mean time to repair” and “analysis of maintenance procedure” (see Appendix 2). Similarly, during the round one survey, the panellists suggest three new elements which have been marked by a * sign (see Table 4). These new elements were: “the design of a preventive plan”, “the optimization of preventive maintenance design”, and “working in line with regulatory agencies. These new elements were included for rating by all the experts in the second round of the questionnaire because they were considered important by the research team (see Table 3).
4.3 Round two results of Delphi study
A total of twenty-three (23) elements constituted the elements of OMP in round two. Among the twenty-three elements, only six (6) which are: “preparation of safety procedure”, “optimization of the maintenance policy”, “optimisation of the maintenance action plan”, “well-defined priority system,” “risk factor establishment”, and “suitable maintenance procedures and process” were ranked very high impact (VHI: 9.00–10.00) by the panellists with a median score of nine (9) (see Table 4); while nine (9) elements which are: “the design of a preventive plan”, “assembling of maintenance organization structure”, “change in policy and its associated results”, “preparation of maintenance operation”, “optimisation of preventive maintenance design”, “organization operational efficiency”, “appropriate procurement”, “maintenance strategies development” and “meeting maintenance objectives” were ranked by the panellists to have a high impact (HI: 7.00–8.99); and eight (8) other elements which are: “maintenance contracts suitability”, “target performance measurement”, “spare-part management”, “timely identification of maintenance work”, “routinisation of optimisation techniques”, “working in line with regulatory agencies”, “reduction in the meantime to repair” and “analysis of maintenance procedures” scored a medium impact (MI: 5.00–6.99). Moreover, among the elements consensus levels varied, whereas the standard deviation scores among the elements suggest strong consistency levels and little variability in the panellist responses.
5. Discussions
This study sought to establish whether the elements of OMP that influence MM (found in other countries) are relevant to the MM of public buildings in the Nigerian built environment industry.
Twenty-three elements of OMP were revealed. Among the twenty-three (23) elements, six (6) elements have a very high impact with a median score range (VHI: 9:00–10.00), while nine (9) elements had a high impact (HI: 7.00–8.99) and eight (8) other elements recorded a medium impact (MI: 5.00–6.99). Although, among the elements, the level of consensus varied, the IQD scores respectively showed consensus with the IQD being ≤1 for fifteen (15) of the elements. Likewise, their respective standard deviation (σx) revealed consistency in the responses of the experts as their respective σx values were at most (1). Out of the fifteen elements that have consensus, six of the elements that recorded (VHI: 9.00–10.00) were: “preparation of safety procedure” with mean (
5.1 Practical and theoretical implications of this work
The outcome of the study has curriculum, practical, theoretical and policy implications. It empirically shows elements of OMP necessary for effective MM of public buildings in the Nigerian built environment industry. The identified elements of OMP will assist maintenance organisations in the determination of how to effectively maintain building infrastructure. The study theoretically advances that OMP for effective MM of buildings embodies fifteen vital elements. Among these vital elements is preparation of safety procedures which indicates that safety comes first in every maintenance activity to be carried out (Riaz et al., 2006). This includes the safety of users as well as the safety of maintenance personnel. On a practical note, the study demonstrates the relative influence of each of the elements. This ought to guide stakeholders in the built environment industry in maintenance policy formulation for the proposed and in-use public buildings. The study was however limited to Southwestern Nigeria due to time and cost constraints (and the global COVID-19 pandemic) which means that the findings cannot be completely generalised for the Nigerian built environment. However, the Southwestern Nigeria region used for this study accounts for the country's major built environment activities. To ensure the findings of this study is applicable to the built environment practically, future studies must be conducted to test the OMP elements in practice. This will involve the incorporation of industry practitioners who have first-hand experience with day-to-day maintenance activities.
6. Conclusions and recommendations
This study was carried out to establish whether the elements of OMP found in other countries that influence MM of buildings are relevant in the MM of public buildings in the Nigerian built environment industry. A total of twenty-three (23) OMP elements that were perceived to have influence MM were evaluated by the expert panellists. Fifteen (15) elements of the OMP out of the elements validated were found to have influenced MM of public buildings, in the built environment industry in Nigeria. Similarly, these elements were concordant with OMP elements that have been identified by earlier studies in some national and industrial contexts.
Hence, the study recommends that in OMP development by building and facility management firms in the Nigerian built environment industry, the following elements are vital to building and facility management firms toward effective MM of buildings. Namely: preparation of safety procedure; optimisation of the maintenance policy; optimisation of the maintenance action plan; well-defined priority system; risk factor establishment; suitable maintenance procedures and process; design of a preventive plan; assembling of maintenance organisation structure; change in policy and its associated results; optimisation of preventive maintenance design; preparation of maintenance operation; organisation operational efficiency; appropriate procurement strategy; maintenance strategies development; and meeting maintenance objectives. In conclusion, the study suggested that the elements of OMP that determine MM of public buildings in the Nigerian built environment are largely similar to the determinants in other geographical contexts. This is because the findings from this study aligns with previous studies carried out in other geographical locations. Also, effective MM of public buildings is assured if there is a critical consideration of these elements in the development of OMP for the MM of the public buildings in the Nigerian built environment industry. However, it is worthy of note that further study could be carried out on validation of the Delphi findings of this study quantitatively.
Based on the foregoing, it is recommended that policy makers in the Nigerian built environment should focus on the adoption of existing OMP elements from other geographical locations. This is because the OMP elements have been found to be applicable to the MM of public buildings in Nigeria. Also, it is recommended that the OMP elements identified from this study should guide industry practitioners in maintenance practices. Lastly, future curriculum reviews on MM should also be informed to make the content of the existing curriculum more receptive to the needs of the built environment industry as it brings to the forefront emerging vital elements of OMP development.
Figures
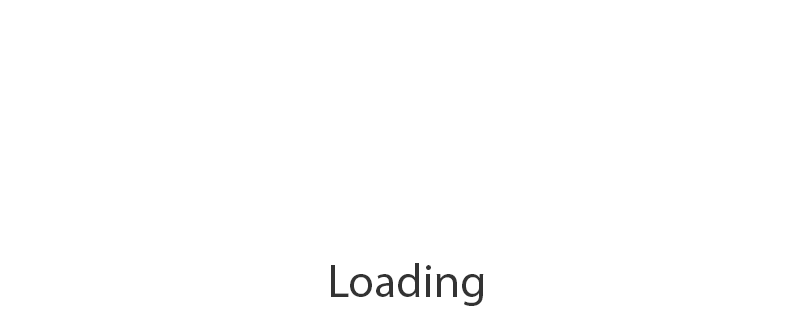
Figure 1
Campbell (1995) maintenance management model
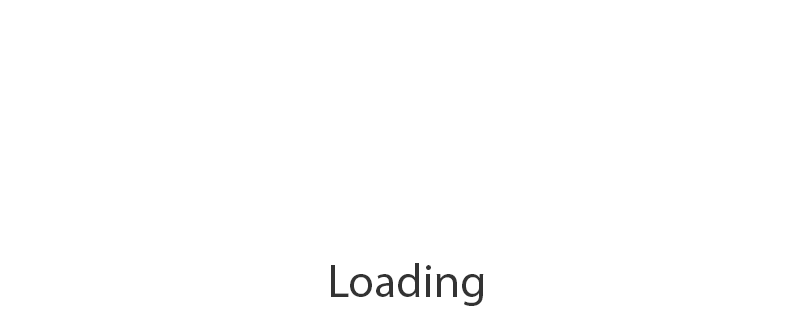
Figure 2
Wireman (2005) maintenance management model
Márquez (2007) maintenance management process and framework
Maintenance management process | Strategic | Start from business plan to maintenance plan Maintenance priorities is define A close loop process |
Tactics | From the maintenance plan to the resources. assignment and task scheduling A close loop process | |
Maintenance management framework | Operational | Proper task completion and date recording A close loop process |
IT | CMMS, condition monitoring technologies | |
Maintenance engineering techniques | RCM, TPM, reliability data analysis, maintenance policy optimisation models OR/MM models | |
Organisational techniques | Relationships management techniques motivation, operators' involvement, etc. |
Element of organisational maintenance policy
Source(s): Researchers' literature survey (2022)
Respondents' demographic profile
Respondents' demographic profile | Frequency (n = 15) | Percentage (%) |
---|---|---|
Highest qualification | ||
Doctor of Philosophy (Ph.D.) | 4 | 26.67 |
Master's degree | 7 | 46.67 |
Bachelor's degree | 4 | 26.67 |
Higher Diploma | 0 | 0 |
Total | 15 | 100 |
Designation | ||
Lecturer | 7 | 46.67 |
Maintenance manager of public buildings | 6 | 40.00 |
Professional/Research institution of buildings | 2 | 13.33 |
Total | 15 | 100 |
Years of experience | ||
1–5 | 0 | 0 |
6–10 | 1 | 6.67 |
11–20 | 9 | 60.00 |
21–30 | 3 | 20.00 |
Over 31 years | 2 | 13.33 |
Total | 15 | 100 |
Professional affiliation | ||
Nigerian Institute of Building | 4 | 26.67 |
Nigeria Institute of Quantity Surveyors | 2 | 13.33 |
Nigeria Institute of Architects | 3 | 20.00 |
Nigeria Society of Engineers | 1 | 6.67 |
Nigeria Institute of Estate Surveyors and Valuer | 2 | 13.33 |
Real Estate Developers Association of Nigeria | 3 | 20.00 |
Total | 15 | 100 |
Round two Delphi study results – elements of OMP for maintenance management of public buildings in Nigeria
Sub-attributes | Median (M) | Mean ( | Standard deviation (σx) | Interquartile deviation (IQD) | Mean scores ranking (R) |
---|---|---|---|---|---|
Organisation operational efficiency | 8 | 8.11 | 1.55 | 1.00 | 12 |
Suitable maintenance procedures and process | 9 | 8.31 | 1.54 | 1.00 | 6 |
Assembling of maintenance organisation structure | 8 | 8.25 | 0.77 | 1.00 | 8 |
Analysis of maintenance procedures | 5 | 5.50 | 1.41 | 1.25 | 23 |
Preparation of maintenance operation | 8 | 8.13 | 0.72 | 1.00 | 10 |
Preparation of safety procedure | 9 | 8.59 | 1.08 | 0.63 | 1 |
Risk factor establishment | 9 | 8.38 | 0.72 | 1.00 | 5 |
Target performance measurement | 6 | 6.65 | 1.27 | 2.00 | 17 |
Routinisation of optimisation techniques | 6 | 5.70 | 1.36 | 1.65 | 20 |
Maintenance strategies development | 8 | 8.05 | 1.48 | 1.00 | 14 |
Spare-part management | 6 | 6.25 | 1.44 | 2.00 | 18 |
Meeting maintenance objectives | 8 | 8.00 | 1.73 | 1.00 | 15 |
Optimisation of the maintenance policy | 9 | 8.53 | 1.73 | 0.50 | 2 |
Optimisation of the maintenance action plan | 9 | 8.47 | 2.10 | 0.50 | 3 |
Well-defined priority system | 9 | 8.40 | 1.24 | 1.00 | 4 |
Appropriate procurement strategy | 8 | 8.07 | 1.49 | 1.00 | 12 |
Change in policy and its associated results | 8 | 8.20 | 1.52 | 1.00 | 9 |
Working in-line with regulatory agencies* | 6 | 5.60 | 1.92 | 2.00 | 21 |
Maintenance contracts suitability | 6 | 6.73 | 1.58 | 2.00 | 16 |
Timely identification of maintenance work | 6 | 6.00 | 1.20 | 1.50 | 19 |
Reduction in mean time to repair | 5 | 5.60 | 1.35 | 2.00 | 21 |
Design of a preventive plan* | 8 | 8.27 | 0.70 | 1.00 | 7 |
Optimisation of preventive maintenance design* | 8 | 8.13 | 0.74 | 0.50 | 10 |
Note(s): The three marked *italic elements in Table 4 were the new elements of OMP that the panelist suggested and was included for rating by all the experts in the second round of the questionnaire because they were considered important by the research team
Questionnaire items | Marks possible | Expected maximum marks | Expected minimum marks | Obtained minimum marks |
---|---|---|---|---|
Q1. Please indicate your highest level of education | ||||
Higher diploma | 1 point | 1 point | ||
Bachelor's degree | 2 points | 2 points | ||
Master's degree | 3 points | |||
Doctoral degree | 4 points | 4 points | ||
Q2. Are you a member of any professional body in Nigeria? | ||||
Yes | 1 point | 1 point | 1 point | |
No | 0 point | 0 point | ||
Q3. Please indicate your years of experience in the Nigerian built environment | ||||
0–5 years | 1 point | 1 point | ||
6–11 years | 2 points | 2 points | ||
11–20 years | 3 points | |||
21–30 years | 4 points | |||
Over 31 years | 5 points | 5 points | ||
Total | 10 points | 2 points | 5 points |
No impact | Low impact | Medium impact | High impact | Very high impact | |||||
---|---|---|---|---|---|---|---|---|---|
1 | 2 | 3 | 4 | 5 | 6 | 7 | 8 | 9 | 10 |
X |
S/N | Element of organisational maintenance policy for effective maintenance management of public buildings | No impact | Low impact | Medium impact | High impact | Very high impact | |||||
---|---|---|---|---|---|---|---|---|---|---|---|
1 | 2 | 3 | 4 | 5 | 6 | 7 | 8 | 9 | 10 | ||
1 | Organisation operational efficiency | X | |||||||||
2 | Suitable maintenance procedures and process | X | |||||||||
3 | Assembling of maintenance organisation structure | X | |||||||||
4 | Analysis of maintenance procedures | X | |||||||||
5 | Preparation of maintenance operation | X | |||||||||
6 | Preparation of safety procedure | x | |||||||||
7 | Risk factor establishment | x | |||||||||
8 | Target performance measurement | x | |||||||||
9 | Routinisation of optimisation techniques | X | |||||||||
10 | Maintenance strategies development | X | |||||||||
11 | Spare-part management | X | |||||||||
12 | Meeting maintenance objectives | X | |||||||||
13 | Optimisation of the maintenance policy | X | |||||||||
14 | Optimisation of the maintenance action plan | X | |||||||||
15 | Well-defined priority system | X | |||||||||
16 | Appropriate procurement strategy | X | |||||||||
17 | Change in policy and its associated results | X | |||||||||
18 | Maintenance contracts suitability | x | |||||||||
19 | Timely identification of maintenance work | x | |||||||||
20 | Reduction in the meantime to repair | x |
S/N | Element of organisational maintenance policy | From no impact to very high impact | ||||||||||
---|---|---|---|---|---|---|---|---|---|---|---|---|
1 | 2 | 3 | 4 | 5 | 6 | 7 | 8 | 9 | 10 | Group median | ||
1 | Organisation operational efficiency | 8 | ||||||||||
2 | Suitable maintenance procedures and process | 9 | ||||||||||
3 | Assembling of maintenance organisation structure | 8 | ||||||||||
4 | Analysis of maintenance procedures | 5 | ||||||||||
5 | Preparation of maintenance operation | 8 | ||||||||||
6 | Preparation of safety procedure | 9 | ||||||||||
7 | Risk factor establishment | 9 | ||||||||||
8 | Target performance measurement | 6 | ||||||||||
9 | Routinisation of optimisation techniques | 6 | ||||||||||
10 | Maintenance strategies development | 8 | ||||||||||
11 | Spare-part management | 6 | ||||||||||
12 | Meeting maintenance objectives | 8 | ||||||||||
13 | Optimisation of the maintenance policy | 9 | ||||||||||
14 | Optimisation of the maintenance action plan | 9 | ||||||||||
15 | Well-defined priority system | 9 | ||||||||||
16 | Appropriate procurement strategy | 8 | ||||||||||
17 | Change in policy and its associated results | 8 | ||||||||||
18 | Maintenance contracts suitability | 6 | ||||||||||
19 | Timely identification of maintenance work | 6 | ||||||||||
20 | Reduction in the meantime to repair | 6 | ||||||||||
21 | Working in line with regulatory agencies | 5 | ||||||||||
22 | Design of a preventive plan | 8 | ||||||||||
23 | Optimisation of preventive maintenance design | 8 | ||||||||||
Reasons/comments |
Q4. Kindly, list elements of organisational maintenance policy for effective maintenance management of public buildings in the Nigerian built environment
Note: Reference can be made to the list of elements of organisational maintenance policy generated from the review of literature
- (a)
Organisation operational efficiency;
- (b)
Suitable maintenance procedures and process;
- (c)
Assembling of maintenance organisation structure;
- (d)
Analysis of maintenance procedures;
- (e)
Preparation of maintenance operation;
- (f)
Preparation of safety procedure;
- (g)
Risk factor establishment;
- (h)
Target performance measurement;
- (i)
Routinisation of optimisation techniques;
- (j)
Maintenance strategies development;
- (k)
Spare-part management;
- (l)
Meeting maintenance objectives;
- (m)
Optimisation of the maintenance policy;
- (n)
Optimisation of the maintenance action plan;
- (o)
Well-defined priority system;
- (p)
Appropriate procurement strategy;
- (q)
Change in policy and its associated results;
- (r)
Maintenance contracts suitability;
- (s)
Timely identification of maintenance work and
- (t)
Reduction in the meantime to repair.
Appendix 2 Delphi round one and questionnaire instructions
Q1. Based on your experience and knowledge, please indicate the extent to which the under listed elements of organisational maintenance policy impact the maintenance management of public buildings in the Nigerian built environment by placing “X” in the boxes provided against each element of organisational maintenance policy using a 10-point scale. Other elements of organisational maintenance policy that have not been listed could also be suggested.
Q2. Kindly rate the impact of the listed attributes of organisational maintenance policy on ensuring effective maintenance management of public buildings in Nigerian.
Appendix 3 Delphi round 2 and questionnaire instructions
Attached is the response computed group median for each of the elements of organisational maintenance policy from round one of the Delphi surveys. You are at autonomy to either accept the group response as computed, maintain your response in round one, or indicate a new response. In cases where your opinion differs from the group median, please provide a reason/comment. Also, from round one of the surveys new elements identified have been included for your response: these are indicated in italic.
Q1. Based on your knowledge and experience, please indicate the extent to which the under-listed elements of organisational maintenance policy impact maintenance management of public buildings in the Nigerian built environment by placing “X” in the boxes provided against each element of organisational maintenance policy using a 10-point scale. 1 = no impact to 10 = very high impact.
References
Adnan, H., Rosman, M.R., Rashid, Z.A., Yusuwan, N.M. and Bakhary, N.A. (2018), “Application of Delphi expert panel in joint venture projects”, IOP Conference Series: Earth and Environmental Science, Vol. 117 No. 1, IOP Publishing, 012048.
Aghimien, D.O., Aigbavboa, C., Edwards, D.J., Mahamadu, A.-M., Olomolaiye, P., Nash, H. and Onyia, M. (2020), “A fuzzy synthetic evaluation of the challenges of smart city development in developing countries”, Smart and Sustainable Built Environment, Vol. ahead-of-print No. ahead-of-print. doi: 10.1108/SASBE-06-2020-0092.
Ahmed, H., Edwards, D.J., Lai, J.H.K., Roberts, C., Debrah, C., Owusu-Manu, D.G. and Thwala, W.D. (2021), “Post occupancy evaluation of school refurbishment projects: multiple case study in the UK”, Buildings, Vol. 11 No. 4, p. 169, doi: 10.3390/buildings1104016.
Ahzahar, N., Karim, N.A., Hassan, S.H. and Eman, J. (2011), “A study of contribution factors to building failures and defects in construction industry”, Procedia Engineering, Vol. 20, pp. 249-255, doi: 10.1016/j.proeng.2011.11.162.
Aigbavboa, C.O. (2014), “An integrated beneficiary-centered satisfaction model for publicly funded housing schemes in South Africa”, Published doctoral dissertation, University of Johannesburg.
Al-Najjar, B. and Alsyouf, I. (2004), “Enhancing a company's profitability and competitiveness using integrated vibration-based maintenance: a case study”, European Journal of Operational Research, Vol. 157 No. 3, pp. 643-665, doi: 10.1016/S0377-2217(03)00258-3.
Ali, A.S. (2009), “Cost decision making in building maintenance practice in Malaysia”, Journal of Facilities Management, Vol. 7 No. 4, pp. 298-306, doi: 10.1108/14725960910990044.
Alzaben, H. (2015), “Development of a MM framework to facilitate the delivery of healthcare provisions in the Kingdom of Saudia Arabia”, Published doctoral dissertation, Nottingham Trent University.
Ameyaw, E.E., Hu, Y., Shan, M., Chan, A.P. and Le, Y. (2016), “Application of Delphi method in construction engineering and management research: a quantitative perspective”, Journal of Civil Engineering and Management, Vol. 22 No. 8, pp. 991-1000, doi: 10.3846/13923730.2014.945953.
Atkin, B. (2003), “Contracting out or managing services in-house”, Nordic Journal of Surveying and Real Estate Research, Vol. 1, pp. 19-33, available at: https://journal.fi/njs/article/view/41490.
Ben-Daya, M., Duffuaa, S.O., Raouf, A., Knezevic, J. and Ait-Kadi, D. (Eds) (2009), Handbook of Maintenance Management and Engineering, Vol. 7, Springer-Verlag London: Springer, London, doi: 10.1007/978-1-84882-472-0.
Campbell, J.D. (1995), “Outsourcing in maintenance management: a valid alternative to -provision”, Journal of Quality in Maintenance Engineering, Vol. 1 No. 3, pp. 18-24, doi: 10.1108/13552519510096369.
Campbell, J.D. (1998), Uptime, Strategies for Excellence in Maintenance Management, Productivity Press, Portland, OR.
Cholasuke, C., Bhardwa, R. and Antony, J. (2004), “The status of maintenance management in UK manufacturing organisations: results from a pilot survey”, Journal of Quality in Maintenance Engineering, Vol. 10 No. 1, pp. 5-15, doi: 10.1108/13552510410526820.
Cobbinah, P.J. (2010), “Maintenance of buildings of public institutions in Ghana. Case study of selected institutions in the Ashanti Region of Ghana”, Published doctoral dissertation, Kwame Nkrumah University of Science and Technology.
Crespo Márquez, A., Moreu de León, P., Gómez Fernández, J.F., Parra Márquez, C. and López Campos, M. (2009), “The maintenance management framework: a practical view to maintenance management”, Journal of Quality in Maintenance Engineering, Vol. 15 No. 2, pp. 167-178, doi: 10.1108/13552510910961110.
Ding, S.H. and Kamaruddin, S. (2015), “Maintenance policy optimization—literature review and directions”, The International Journal of Advanced Manufacturing Technology, Vol. 76 No. 5, pp. 1263-1283, doi: 10.1007/s00170-014-6341-2.
Duffuaa, S.O., Raouf, A. and Campbell, J.D. (1999), Planning and Control of Maintenance Systems, New York, New York, doi: 10.1007/978-3-319-19803-3.
Edwards, D.J., Holt, G.D. and Harris, F.C. (1998), “Predictive maintenance techniques and their relevance to construction plant”, Journal of Quality in Maintenance Engineering, Vol. 4 No. 1, pp. 25-37, doi: 10.1108/13552519810369057.
Edwards, D., Parn, E.A., Sing, M.C.P. and Thwala, W.D. (2019), “Risk of excavators overturning: determining horizontal centrifugal force when slewing freely suspended loads”, Engineering, Construction and Architectural Management, Vol. 26 No. 3, pp. 479-498, doi: 10.1108/ECAM-03-2018-0125.
Edwards, D.J., Rillie, I., Chileshe, N., Lai, J., Hosseini, M.R. and Thwala, W.D. (2020), “A field survey of hand–arm vibration exposure in the UK utilities sector”, Engineering, Construction and Architectural Management, Vol. 27 No. 9, pp. 2179-2198, doi: 10.1108/ECAM-09-2019-0518.
Faghihinia, E. and Mollaverdi, N. (2012), “Building a maintenance policy through a multi-criterion decision-making model”, Journal of Industrial Engineering International, Vol. 8 No. 1, pp. 1-15, doi: 10.1186/2251-712X-8-14.
Fatokun, T.O. (1997), “Prospect control of schemes of maintenance, repairs and improvement works”, Paper Presented at a 2-Day Workshop on Residential Property Maintenance Planning and Management, organized by Estate Surveyors Registration Board of Nigeria in with First State Communication.
Fisher, L., Edwards, D.J., Pärn, E.A. and Aigbavboa, C.O. (2018), “Building design for people with dementia: a case study of a UK care home”, Facilities, Vol. 36 Nos 7/8, pp. 349-368, doi: 10.1108/F-06-2017-0062.
Fletcher, A.J. and Marchildon, G.P. (2014), “Using the Delphi method for qualitative, participatory action research in health leadership”, International Journal of Qualitative Methods, Vol. 13 No. 1, pp. 1-18, doi: 10.1177/160940691401300101.
HajShirmohammadi, A. and Wedley, W.C. (2004), “Maintenance management – an AHP application for centralization/decentralization”, Journal of Quality in Maintenance Engineering, Vol. 10 No. 1, pp. 16-25, doi: 10.1108/13552510410526839.
Hou, H.C., Lai, J. and Edwards, D. (2020), “Gap theory based post-occupancy evaluation (GTbPOE) of dormitory building performance: a case study and a comparative analysis”, Building and Environment, Vol. 185, 107312, doi: 10.1016/j.buildenv.2020.107312.
Irajpour, A., Fallahian-Najafabadi, A., Mahbod, M.A. and Karimi, M. (2014), “A framework to determine the effectiveness of maintenance strategies lean thinking approach”, Mathematical Problems in Engineering, Vol. 2014, p. 11, 132140, doi: 10.1155/2014/132140.
Karia, N., Asaari, M.H.A.H. and Saleh, H. (2014), “Exploring maintenance management in service sector: a case study”, Proceedings of International Conference on Industrial Engineering and Operation Management, Bali, Indonesia, 7-9 January, pp. 3119-3128.
Leung, W.C. (2001), “How to design a questionnaire”, University of East Agnlia: BMJ, Vol. 322, Suppl S6, pp. 1-9.
Lind, H. and Muyingo, H. (2012), “Building maintenance strategies: planning under uncertainty”, Property Management, Vol. 30 No. 1, pp. 14-28, doi: 10.1108/02637471211198152.
Loo, R. (2002), “The Delphi method: a powerful tool for strategic management”, Policing: An International Journal of Policy Strategies and Management, Vol. 25 No. 4, pp. 762-769, doi: 10.1108/13639510210450677.
Márquez, A.C. (2007), The Maintenance Management Framework: Models and Methods for Complex Systems Maintenance, Springer Science & Business Media, Berlin.
Marquez, A.C. and Gupta, J.N. (2006), “Contemporary maintenance management: process, framework, and supporting pillars”, Omega, Vol. 34 No. 3, pp. 313-326, doi: 10.1016/j.omega.2004.11.003.
Miller, M.M. (1993), “Enhancing regional analysis with the Delphi method”, Review of Regional Studies, Vol. 23 No. 2, pp. 191-212.
Mobley, R.K. (2002), An Introduction to Predictive Maintenance, Butterwort-Heineman, Elsevier, Amsterdam.
National Building Code (2006), Federal Republic of Nigeria: National Building Code, 1st ed., Government Report, Nigeria.
Oberschmidt, J., Geldermann, J., Ludwig, J. and Schmehl, M. (2010), “Modified PROMETHEE approach for assessing energy technologies”, International Journal of Energy Sector Management, Vol. 4 No. 2, pp. 183-212, doi: 10.1108/17506221011058696.
Ogunbayo, B.F. and Aigbavboa, O.C. (2019), “Maintenance requirements of students' residential facility in higher educational institution (HEI) in Nigeria”, in IOP Conference Series: Materials Science and Engineering, Vol. 640 No. 1, 012014, IOP Publishing, doi: 10.1088/1757-899X/640/1/012014.
Ogunbayo, B.F., Ajao, A.M., Alagbe, O.T., Ogundipe, K.E., Tunji-Olayeni, P.F. and Ogunde, A. (2018), “Residents' facilities satisfaction in housing project delivered by public-private partnership (PPP) in Ogun State, Nigeria”, International Journal of Civil Engineering and Technology (IJCIET), Vol. 9 No. 1, pp. 562-577.
Ogunbayo, B., Aigbavboa, C. and Akinradewo, O. (2021), “Experimental assessment of strength parameters of river sand for sandcrete block production”, International Journal of Engineering Research in Africa, Trans Tech Publications, Vol. 53, pp. 67-75.
Ogunbayo, B.F., Aigbavboa, C.O., Thwala, W., Akinradewo, O., Ikuabe, M. and Adekunle, S.A. (2022), “Review of culture in maintenance management of public buildings in developing countries”, Buildings, Vol. 12 No. 5, p. 677, doi: 10.3390/buildings12050677.
Oke, S.A. (2005), “An analytical model for the optimisation of maintenance profitability”, International Journal of Productivity and Performance Management, Vol. 54 No. 2, pp. 113-136, doi: 10.1108/17410400510576612.
Oke, S.A. and Charles-Owaba, O.E. (2006), “An approach for evaluating preventive maintenance scheduling cost”, International Journal of Quality and Reliability Management, Vol. 23 No. 7, pp. 847-879, doi: 10.1108/02656710610679842.
Olanrewaju, A.L. and Abdul-Aziz, A.R. (2015), “Building maintenance processes, principles, procedures, practices and strategies”, in Building Maintenance Processes and Practices, Springer, Singapore, pp. 79-129.
Olanrewaju, O., Chileshe, N. and Edwards, D.J. (2020), “Estimating on-site emissions during ready mixed concrete (RMC) delivery: a methodology”, Case Studies in Construction Materials, Vol. 13, doi: 10.1016/j.cscm.2020.e00439.
Omar, M.F., Ibrahim, F.A. and Omar, W.M.S.W. (2016), “An assessment of the maintenance management effectiveness of public hospital building through key performance indicators”, Sains Humanika, Penerbit UTM Press, Vol. 8 Nos 4-2, pp. 51–56.
Parida, A. and Kumar, U. (2009), “Maintenance productivity and performance measurement”, in Ben-Daya, M., Duffuaa, S., Raouf, A., Knezevic, J. and Ait-Kadi, D. (Eds), Handbook of Maintenance Management and Engineering”, Springer, London, doi: 10.1007/978-1-84882-472-0_2.
Pinjala, S.K., Pintelon, L. and Vereecke, A. (2006), “An empirical investigation of the relationship between business and maintenance strategies”, International Journal of Production Economics, Vol. 104 No. 1, pp. 214-229, doi: 10.1016/j.ijpe.2004.12.024.
Pintelon, L. and Muchiri, P.N. (2009), Safety and Maintenance: Handbook of Maintenance Management and Engineering, Springer, London, pp. 613-648.
Public Procurement Act (2007), “Laws of the Federal Republic of Nigeria”, Interpretation, Government printer, Abuja, Vol. 1, p. 4.
Riaz, Z., Edwards, D.J. and Thorpe, A. (2006), “Sight Safety: a hybrid information and communication technology system for reducing vehicle/pedestrian collisions”, Automation in Construction, Vol. 15 No. 6, pp. 719-728, doi: 10.1016/j.autcon.2005.09.004.
Rowe, G. and Wright, G. (2001), “Expert opinions in forecasting: the role of the Delphi technique”, in Armstrong, J.S. (Ed.), Principles of Forecasting. International Series in Operations Research and Management Science, Vol. 30, Springer, Boston, MA, doi: 10.1007/978-0-306-47630-3_7.
Sarantakos, S. (2005), Social Research, 3rd ed., Palgrave Macmillan, Basingstoke.
Seeley, I.H. (1996), Building Economics: Appraisal and Control of Building Design Cost and Efficiency, Macmillan International Higher Education, doi: 10.1007/979-1-349-13757-2.
Sherwin, D. (2000), “A review of overall models for maintenance management”, Journal of Quality in Maintenance Engineering, Vol. 6 No. 3, pp. 138-164, doi: 10.1108/13552510010341171.
Sing, M., Fung, I., Liu, H. and Edwards, D.J. (2021), “Dynamic construction site layout planning: an application of branch and bond algorithm”, International Journal of Building Pathology and Adaptation, Vol. ahead-of-print No. ahead-of-print, doi: 10.1108/IJBPA-06-2020-0053.
Somiah, M.K., Aigbavboa, C.O. and Thwala, W.D. (2020), “Validating elements of competitive intelligence for competitive advantage of construction firms in Ghana: a Delphi study”, African Journal of Science, Technology, Innovation, and Development, Vol. 13 No. 3, pp. 1-10, doi: 10.1080/20421338.2020.1762309.
Swanson, L. (2001), “Linking maintenance strategies to performance”, International Journal of Production Economics, Vol. 70 No. 3, pp. 237-244, doi: 10.1016/S0925-5273(00)00067-0.
Takata, S., Kirnura, F., van Houten, F.J., Westkamper, E., Shpitalni, M., Ceglarek, D. and Lee, J. (2004), “Maintenance: changing role in life cycle management”, CIRP Annals, Vol. 53 No. 2, pp. 643-655, doi: 10.1016/S0007-8506(07)60033-X.
Tengan, C. and Aigbavboa, C. (2021), “Validating factors influencing monitoring and evaluation in the Ghanaian construction industry: a Delphi study approach”, International Journal of Construction Management, Vol. 21 No. 3, pp. 223-234.
Tilakasiri, K.K. (2015), “Development of new frameworks, standards, and principles via Delphi data collection method”, International Journal Science Research, Vol. 4 No. 9, pp. 1189-1194.
Tsang, A.H. (2002), “Strategic dimensions of maintenance management”, Journal of Quality in Maintenance Engineering, Vol. 8 No. 1, pp. 7-39, doi: 10.1108/13552510210420577.
Vanneste, S.G. and Van Wassenhove, L.N. (1995), “An integrated and structured approach to improve maintenance”, European Journal of Operational Research, Vol. 82 No. 2, pp. 241-257, doi: 10.1016/0377-2217(94)00261-A.
Visser, J.K. (1998), “Maintenance management: an appraisal of current strategies”, ICOMS Conference, Adelaide, Australia, May 20-21, Paper 031.
Wang, H. (2002), “A survey of maintenance policies of deteriorating systems”, European Journal of Operational Research, Vol. 139 No. 3, pp. 469-489, doi: 10.1016/S0377-2217(01)00197-7.
Wireman, T. (2005), Developing Performance Indicators for Managing Maintenance, Industrial Press, New York.