Abstract
Purpose
The purpose of this paper is to artificially construct a functional surface with self-propulsion flow characteristics for the directional transportation of propellant in surface tension tanks.
Design/methodology/approach
In this study, a method to enhance the propulsion efficiency by using functional surfaces of self-propulsion performance was proposed. Superhydrophilic wedged-groove with the superhydrophobic background was fabricated and the self-propulsion capacity was verified.
Findings
It is found that the self-propulsion capacity is related to the divergence angle of the wedged-groove in the hydrophilic area, and the velocity of the droplets on the deflector plate is the largest with the divergence angle of 4°; the temperature gradient field formed by the condensing device at the nozzle can accelerate the droplet outflow from the tank.
Originality/value
Realization of this idea provides an accurate control strategy for the complex flow process of propellant in plate surface tension tanks, which could enhance the efficiency of the tension tank significantly.
Keywords
Citation
Li, Q., Zhang, B., Yang, T., Dai, Q., Huang, W. and Wang, X. (2022), "Preliminary investigation on the self-propulsion performance of wedge-shaped functional surfaces", Journal of Intelligent Manufacturing and Special Equipment, Vol. 3 No. 2, pp. 217-227. https://doi.org/10.1108/JIMSE-09-2022-0015
Publisher
:Emerald Publishing Limited
Copyright © 2022, Qianqian Li, Bo Zhang, Tao Yang, Qingwen Dai, Wei Huang and Xiaolei Wang
License
Published in Journal of Intelligent Manufacturing and Special Equipment. Published by Emerald Publishing Limited. This article is published under the Creative Commons Attribution (CC BY 4.0) licence. Anyone may reproduce, distribute, translate and create derivative works of this article (for both commercial and non-commercial purposes), subject to full attribution to the original publication and authors. The full terms of this licence may be seen at http://creativecommons.org/licences/by/4.0/legalcode
1. Introduction
Spacecraft tanks are important devices for storing and managing propellants, requiring the ability to provide propellants for the spacecraft throughout the mission life. The plate surface tension tank is a typical tank structure, which uses the deflector plate as the flow path and the liquid surface tension as the driving force to achieve the supply of propellant (Tam et al., 2008). This kind of tank has the advantages of simple structure, high management reliability, long service life and so on, and is considered as the preferred type of tank for spacecraft, especially for various types of satellites implementing on-orbit refueling (Benton et al., 2007).
However, in the space environment, the liquid properties are different from those under constant gravity, the gas–liquid interface in the tank is not horizontal, and the liquid distribution is discontinuous (Hu and Xu, 1999). Slight external interferences (such as the loss of liquid adsorbed on the deflector when the spacecraft suddenly accelerates) will cause the position of the liquid to change, resulting in liquid sloshing, capillary flow, gas-liquid separation and other phenomena (Griffin, 1986). At this time, the flow process of propellant becomes extremely complex, and its positioning and supply cannot be effectively guaranteed. In light cases, the propulsion efficiency will be reduced, and in serious cases, the dynamic failure of spacecraft will result in the loss of service ability (Nicolas, 1998; Debreceni et al., 1996). In space where there is no reasonable complementary mechanism, accurate management and regulation of propellants have become one of the key technologies that must be broken through in-orbit refueling of spacecraft.
The deflector plate is the core component of the plate surface tension tank, the transport of the propellant in the tank is closely related to the layout of the deflector plate. Its propulsion principle is that the deflector plate is close to the wall of the tank and forms an included angle perpendicular to it, and extends from one end of the propellant tank to the propellant outlet. When the curvature radius of the liquid at the end of the liquid pool is greater than that at the liquid outlet, the pressure difference is formed between the two ends of the included angle, driving the liquid to flow to the tank outlet, which supplies propellant for the system. Compared with liquids, metal materials generally have a higher surface energy (for example, at 20°C, the surface tension of liquid is ∼10–2 N/m, while that of a common metal is about 1 N/m) (Wen and Huang, 2011). The cohesion work between the liquid molecules is much less than the adhesion work during the infiltration process with the metal surface so that the liquid–solid interaction is enough to spread the liquid phase on the solid surface, which means that the surface energy and infiltration characteristics of the deflector plate have a crucial impact on its conductivity (Gao and Liu, 2010). Therefore, whether efficient and controllable propulsion can be realized by modifying the surface structure of the deflector plate is worth pondering by researchers.
In nature, the special microstructures on the surface of an organism can give the organism a unique property. For example, the unique hierarchical structure and special waxes on the surface of lotus leaves make it superhydrophobic (Barthlott and Neinhuis, 1997). The microarray of 5–9 μm is distributed on its surface, and a tiny nano-structure is distributed on the microarray (Figure 1a). The synergistic effect of this micro-nano secondary structure and its biological wax makes it superhydrophobic and low adhesion (Liu and Jiang, 2011). Similarly, there is a large-size groove periodic structure on the submillimeter scale on the surface of rice leaves, which makes it present an anisotropic static hydrophobic angle (Figure 1b) (Lu et al., 2008); the three-layer microstructure of pitcher plant enables the droplets to self-propulsion flow on the surface of its superhydrophobic mouth edge. When the droplet moves inward, it is fixed at the sharp edge φ = 2∼8°; when the droplet moves outward, it expands outward along the wedge-shaped corner, then pushes out the air in the microcavity to fill the liquid, and finally gathers at the front end of the microcavity (Figure 1c) (Li et al., 2017; Chen et al., 2016).
Inspired by the above special functional surfaces with directional transportation in nature, it is expected to artificially construct a functional surface with self-propulsion flow characteristics for the directional transportation of propellant in surface tension tanks (Dai et al., 2020, 2021). Realization of this idea could provide an accurate control strategy for the complex flow process of propellant in plate surface tension tanks, which could enhance the efficiency of the tension tank significantly.
Hereby, in this study, a functional surface of a superhydrophilic wedged-groove with a superhydrophobic background was fabricated, and its water droplets self-propulsion capacity was investigated. The influence of surface texture parameters on the transport capacity of water droplets was investigated, and a combination of functional surfaces and external thermal gradients to enhance the transport performance was realized. A design principle of a surface tension tank with the controllable ability and excellent self-propulsion properties is proposed, which provides general guidance to enhance the maneuverability of spacecraft and improve its service life.
2. Experiments
2.1 Sample preparation
Pure aluminum was selected as the substrate (purity ≥ 99.9%), and its geometric dimension is 71*23*2 mm (length*width*height). The superhydrophobic coating is prepared by chemical coating on the surface of the sample, and then the super-hydrophilic structure is prepared on the superhydrophobic surface by laser direct writing processing technology. The technological process is shown in Figure 2, and the specific processing steps are as follows:
Pretreatment: Polish the surface and edge of the pure aluminum sample until the roughness Ra is less than 0.4 mm, and ultrasonic clean the surface of the sample with anhydrous ethanol to remove oil and impurities.
Coating: the two-stage rotating coating method (rotating speed of both stages is 15r/s, lasting for 10s) is used to spray the samples with two treatment reagents (Rust-oleum 274,232 Never Wet Multi-Purpose Kit, Rust-Oleum, America) to obtain the superhydrophobic coating.
Laser etching: the specific processing parameters for UV laser drilling (KY-MUV3L, Wuhan Keyi, China) are as follows: processing velocity of 1,500 mm/s, output power of 3 W, frequency of 40 KHz, pulse width of 0.1 μm, and processing five times. The hydrophobic surface coating is removed by a computer-controlled laser beam according to the designed structure calibration, and the hydrophilic region with a certain shape is obtained. Table 1 shows the detailed parameters of the functional structure designed in the study.
Figure 3 shows the SEM (SU8200, Hitachi, Japan) of a typical wedge structure prepared for the experiment (divergence angle is 4°). It can be seen from the figure that the microstructure of the coating area (as shown in the blue box) is different from that of the laser marking area (as shown in the red box). The surface of the coating area is relatively flat at the micron-level magnification, and there are sparse micron-level bumps attached. At the near-nanometer magnifications (as shown in the purple box), the surface has a complex interlacing microstructure. This special micro-nano structure makes the region superhydrophobic. In the laser marking area, the traces of laser scanning can be seen at the micron-level magnification, showing a regular “peak and valley” shape with obvious protrusions on the surface. After further magnification (as shown in the green box), it can be observed that there are also nanoscale bumps on the micron bumps. This special structure obtained by laser marking makes the hydrophilic aluminum surface obtain superhydrophilic characteristics.
The contact angles of the hydrophilic and hydrophobic areas of the prepared sample and the surface before treatment were measured with a dose of 10 microliters of deionized water, as shown in Figure 4. The measurement results are as follows: contact angle of deionized water in the hydrophilic area of the sample after preparation is 9° ± 2°, which is in line with the range of superhydrophilic; contact angle of deionized water on the surface before treatment is 69° ± 2°, which is in line with the range of hydrophilic; contact angle of deionized water in the hydrophobic area of the sample after preparation is as high as 153° ± 2°, which is in line with the range of superhydrophobic. The measurement results show that the preparation test results meet the expectations.
2.2 Superhydrophobic and superhydrophilic mechanism
A droplet placed on a solid surface can be regarded as a system where the gas, liquid and solid phases coexist. The relationship between the contact angle (θ) of the liquid on the ideally smooth surface and the three interfacial tensions can be obtained from Young’s equation (Tadmor, 2004) as shown in Figure 5a:
For droplets standing on the rough surface, the famous Wenzel and Cassie–Baxter infiltration models can be used to characterize the relationship between the apparent θ and
In the formula, the
The superhydrophilic and superhydrophobic characteristics of the prepared sample surface can be explained by the Wenzel and Cassie–Baxter formulas above. Since the untreated aluminum surface is hydrophilic, roughening can significantly increase the ratio (r) of the actual contact area of the liquid to the projected area covered. According to formula (2), the equilibrium contact angle (
2.3 Experimental setup and process
A test platform for self-propulsion flow characteristics of the functional surface is built, as shown in Figure 6. The test platform is mainly composed of a rotatable fine-tuning slide and a scale. The rotatable slide can change the climbing angle of droplets. The specific test steps are as follows: 1) Place the prepared sample on the rotatable fine-tuning slide; 2) using a micro syringe, slowly inject deionized water droplets (volume of 10 μL) into the left side of the sample, observe the self-propulsion flowing process of the droplets moving from the left side to the right side of the sample, and record with a camera; 3) through video analysis, obtain the relationship between the flow distance and velocity of droplets on the surface of the sample and the tilt angle, to quantitatively evaluate the directional transportation capacity of the wedge-shaped functional surface.
We complete the exploration experiment starting at 0° (horizontal position), and after the successful horizontal test, increase the tilt angle of the sample by a gradient of 2°. The above test process is repeated until the droplet cannot overcome gravity and move spontaneously to the other end of the sample.
3. Results and discussion
3.1 Propulsion speed on horizontal surfaces
To explore the relationship between the speed of self-propulsion movement of droplets on the wedge-shaped functional surface and the amounts of water, a horizontal exploration experiment is carried out using a sample with a wedge-shaped structure, whose divergence angle is 4°, as an example. Rotate the rotatable slide, and set its tilt angle to 0°. The experimental steps are the same as 2.3, but continuously inject 12 drops of deionized water droplets onto the sample each time. Repeat the steps three times. The experimental process is recorded by a high-definition camera, and the speed of the water droplet is calculated according to the time from the time when the water droplet first touches the surface to the time of pushing 50 mm, and the experimental results are taken as the average of the three tests, as shown in Figure 7b. As can be seen from Figure 7, the prepared wedge-shaped functional surface has excellent self-propulsion flow characteristics, which can rapidly advance the liquid along the divergence direction of wedged-groove. The average advance speed within 50 mm is 31.677 mm/s, and the self-propulsion speed is independent of the amount of liquid.
3.2 Propulsion performance on tilted surfaces
Based on the above experimental results, we further explore the influence of the divergence angle of the wedged-groove on the performance of transporting water of the sample. After preliminary experiments, it is learned that, if setting fault in the hydrophilic area, the droplet velocity will be reduced; the hydrophilic area that has a single wedge-shaped angle is more advantageous to the droplets to the center forward than which has multiple wedge-shaped angles, and the velocity of the droplets is related to the divergence angle of the wedged-groove in the hydrophilic area; when the divergence angle of the wedged-groove ranges from 2° to 5°, the droplet can achieve maximum velocity. Therefore, this test measures the speed of droplets at the divergence angle(α) of 2°, 3°, 4° and 5°, and changes the tilt angle (Ф) of the sample to complete the corresponding antigravity ascending experiment. The test process is shown in Figure 8.
During the test, the flow rate of the droplets is affected by various factors such as the surface treatment of the sample, the degree of infiltration, the size of the droplets and the initial position of the droplet drops. The deviation of individual data caused by these factors will be ignored in the data analysis, the test results are shown in Figure 9. The results show that when the tilt angle of the sample is 0°, the droplet velocity is the largest on the sample whose divergence angle of the wedged-groove is 4°; the larger the tilt angle of the sample is, the greater the resistance in the moving direction is, and the slower the droplet moves. On the samples with divergence angles of 2°, 3°, 4° and 5°, the final tilt angle of the droplet that can climb are 14°, 13°,12° and 14°, respectively.
3.3 Tension tank model based on self-propulsion functional surface
Based on the above experimental results, a tension tank model based on the self-propulsion functional surface is further constructed, as shown in Figure 10. A sample with a wedged-groove divergence angle of 4° is placed in the tank, and the inner wall of the tank is treated with superhydrophobic. The condenser is set at the nozzle to form a temperature gradient field, to realize the active control of droplets from the high-temperature area to the low-temperature area: the low temperature is set by the condenser outside the nozzle duct (TEC2-19008, the temperature is about ∼18°C), the room temperature is kept inside to realize the temperature gradient distribution between the inner sample and the outer duct, so that the temperature control droplets flow from high temperature to low-temperature area, and accelerate the flow of the droplets to the duct.
To explore the active control effect of droplets in the temperature gradient field, tank propulsion tests are carried out under the conditions with and without the condenser respectively. The test process and results are shown in Figure 11.
When there is no condenser at the nozzle of the tank, 18 drops need to be dropped at the nozzle on one side of the tank before droplets appear. And when the tank nozzle is provided with a condenser, droplets appear with just 13 drops dropped, and the advance speed of droplets is faster than that without the condenser. The test results show that the low temperature achieved by the condenser can accelerate the droplet outflow from the tank, which is consistent with the previous theoretical analysis.
3.4 Propulsion mechanism
The three-dimensional distribution of the liquid on the inclined superhydrophobic surface (the inclination is β) is shown in Figure 12. The liquid is firmly confined to the super hydrophilic diffusion tank on the surface (the divergence angle is α, H and L respectively representing the height and length of the curved surface formed by the liquid). Due to the significant difference in wettability between the super hydrophilic region and the super hydrophobic region, the contact angle gradually increases at the boundary between the super hydrophilic region and the super hydrophobic region. When the liquid is stable in the diversion tank, it is mainly affected by the wettability difference induced driving force (
4. Conclusion
According to the above test results, it is confirmed that the hydrophilic area of the designed functional surfaces will reduce the droplet velocity, and if it is too large, the droplets will not flow through it. The self-propulsion capacity is related to the divergence angle of the wedged-groove in the hydrophilic area, and the velocity of the droplets is fastest on the surface with a divergence angle of 4°. The temperature gradient field formed by the condensing device at the nozzle can accelerate the droplet outflow from the tank. It is expected that via the combination of condensing and thermocouple device, one can set different condensing temperatures, explore the minimum amount of liquid by outflow driving the tank at different condensing temperatures and achieve the suitable thermal gradient with an excellent self-propulsion capacity. On this basis, to explore the maximum angle droplets can climb with the tank under the dual action of wettability gradient and temperature gradient field.
Figures
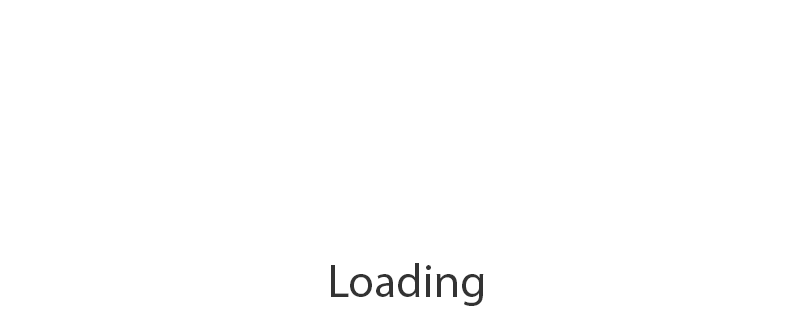
Figure 1
(a) Micro papillae on the surface of lotus leaves (Liu and Jiang, 2011); (b) micro-nano structures on the surface of a rice leaf (Lu et al., 2008); and (c) micro grooves on the mouth edge surface of pitcher plant (Chen et al., 2016)
Dimension parameters of wedged-groove
Description | Symbol | Value |
---|---|---|
Width of the starting end | W | 40 μm |
Divergence angle | α | 1, 2, 4° |
Length of the wedged-groove | L | 70 mm |
Average depth | H | 20 μm |
References
Barthlott, W. and Neinhuis, C. (1997), “Purity of the sacred lotus, or escape from contamination in biological surfaces”, Planta, Vol. 202, pp. 1-8.
Benton, J., Ballinger, I., Jaekle, D.E., Olson, M.F. (2007), “Design and Manufacture of a Propellant Tank Assembly”, 43rd AIAA/ASME/SAE/ASEE Joint Propulsion Conference and Exhibit, AIAA-2007-5559.
Chen, H.W., Zhang, P.F., Zhang, L.W., Liu, H.L., Jiang, Y., Zhang, D.Y., Han, Z.W. and Jiang, L. (2016), “Continuous directional water transport on the peristome surface of nepenthes alata”, Nature, Vol. 532 No. 7597, pp. 85-89.
Dai, Q.W., Huang, W., Wang, X.L. and Khonsari, M.M. (2021), “Directional interfacial motion of liquids: fundamentals, evaluations, and manipulation strategies”, Tribology International, Vol. 154, p. 106749.
Dai, Q.W., Qiu, Z.H., Chong, Z.J., Huang, W. and Wang, X.L. (2020), “Propelling liquids on superhydrophobic surfaces with superhydrophilic diverging grooves”, Surface Innovations, Vol. 8 No. 3, pp. 158-164.
Debreceni, M., Lay, W.D., Kuo, T., Jaekle, D.E. (1996), “Design and development of a communications satellite propellant tank”, 32nd AIAA/ASME/SAE/ASEE Joint Propulsion Conference and Exhibit, AIAA-1996-2749.
Gao, S.Q. and Liu, H.P. (2010), Capillary Mechanics, Science Press, Beijing.
Griffin, J.W. (1986), “Background and programmatic approach for the development of orbital fluid resupply tankers”, 22nd Joint Propulsion Conference Huntsville, AIAA 86-1601.
Hu, W.R. and Xu, S.C. (1999), Microgravity Fluid Mechanics, Science Press, Beijing.
Li, C.X., Wu, L., Yu, C.L. and Dong, Z.C. (2017), “Peristome-mimetic curved surface for spontaneous and directional separation of micro water-in-oil drops”, Angewandte Chemie-International Edition, Vol. 56 No. 44, pp. 13623-13628, 13623.
Liu, K.S. and Jiang, L. (2011), “Bio-inspired design of multiscale structures for function integration”, Nano Today, Vol. 6, pp. 155-175.
Lu, X.B., Zhou, J.H., Zhao, Y.H., Qiu, Y. and Li, J.H. (2008), “Room temperature ionic liquid based polystyrene nanofibers with superhydrophobicity and conductivity produced by electrospinning”, Chemistry of Materials, Vol. 20 No. 10, pp. 3420-3424.
Nicolas, C. (1998), “Design and development methodologies of a propellant management device for small satellite tanks”, 34th AIAA/ASME/SAE/ASEE Joint Propulsion Conference and Exhibit, AIAA-98-3814, pp. 1-8.
Tadmor, R. (2004), “Line energy and the relation between advancing, receding, and young contact angles”, Langmuir, Vol. 20 No. 18, pp. 7659-7664.
Tam, W., Ballinger, I., Jaekle, D. E. (2008), “Surface tension PMD Tank for on orbit fluid transfer”, 44th AIAA/ASME/SAE/ASEE Joint Propulsion Conference and Exhibit, AIAA 2008-5105.
Wen, S.Z. and Huang, P. (2011), Interface Science and Technology, Tsinghua University Press, Beijing.
Acknowledgements
The authors are grateful for the support from the National Natural Science Foundation of China (No. 51805252).