Abstract
Purpose
The existing Nonlinear Dynamic Vibration Absorbers (NLDVAs) have the disadvantages of complex structure, high cost, high installation space requirements and difficulty in miniaturization. And most of the NLDVAs have not been applied to reality. To address the above issues, a novel Triple-magnet Magnetic Dynamic Vibration Absorber (TMDVA) with tunable stiffness, only composed of triple cylindrical permanent magnets and an acrylic tube, is designed, modeled and tested in this paper.
Design/methodology/approach
(1) A novel TMDVA is designed. (2) Theoretical and experimental methods. (3) Equivalent dynamics model.
Findings
It is found that adjusting the magnet distance can effectively optimize the vibration reduction effect of the TMDVA under different resonance conditions. When the resonance frequency of the cantilever changes, the magnet distance of the TMDVA with a high vibration reduction effect shows an approximately linear relationship with the resonance frequency of the cantilever which is convenient for the design optimization of the TMDVA.
Originality/value
Both the simulation and experimental results prove that the TMDVA can effectively reduce the vibration of the cantilever even if the resonance frequency of the cantilever changes, which shows the strong robustness of the TMDVA. Given all that, the TMDVA has potential application value in the passive vibration reduction of engineering structures.
Keywords
Citation
Chen, X., Leng, Y., Sun, F., Su, X., Sun, S. and Xu, J. (2023), "Theoretical and experimental study of a novel triple-magnet magnetic dynamic vibration absorber with tunable stiffness", Journal of Intelligent Manufacturing and Special Equipment, Vol. 4 No. 2, pp. 99-128. https://doi.org/10.1108/JIMSE-04-2023-0002
Publisher
:Emerald Publishing Limited
Copyright © 2023, Xiaoyu Chen, Yonggang Leng, Fei Sun, Xukun Su, Shuailing Sun and Junjie Xu
License
Published in Journal of Intelligent Manufacturing and Special Equipment. Published by Emerald Publishing Limited. This article is published under the Creative Commons Attribution (CC BY 4.0) licence. Anyone may reproduce, distribute, translate and create derivative works of this article (for both commercial and non-commercial purposes), subject to full attribution to the original publication and authors. The full terms of this licence may be seen at http://creativecommons.org/licences/by/4.0/legalcode
1. Introduction
Structural vibration is ubiquitous in various fields such as aerospace, mechanical and civil engineering. John Milne first proposed the concept of vibration control in the early 19th century (Housner et al., 1997), and then Yao (1972) introduced it into civil engineering in 1972 to study the vibration control of civil structures. Dynamic Vibration Absorber (DVA), a kind of passive vibration reduction device, was first proposed by Frahm in 1909 (Xu, 2015). Till now, DVAs have been widely used in the vibration control of engineering structures. Linear Dynamic Vibration Absorber (LDVA), also called Tuned Mass Damper (TMD), is usually composed of a linear stiffness element, a mass block and a damping element. When the resonance frequency of the LDVA is approximately equal to the vibration frequency of the primary structure, the LDVA can provide the primary structure with a force that is opposite to the excitation force and can dissipate vibration energy through its damping (Liu et al., 2007). The TMD classical design theory proposed by Den Hartog (1947) and Ormondroyd and Den Hartog (1928) has been widely used in the parameter optimization of TMDs or LDVAs. Cheng et al. (2020) have proposed a novel Inertial Amplification Mechanism (IAM) to improve the damping performance of a classical TMD. With IAM-TMD, the dynamic response of the primary structure and the damper are simultaneously mitigated. Christie et al. (2019) have developed a magnetorheological-fluid-based pendulum TMD, which is effective in reducing the dynamic response of multistory structures. Di Matte et al. (2019) have investigated the use of a TMD to control the response of foundation vibration isolation structures under random excitation. With proper optimization of the proposed procedure, the TMD can effectively reduce the response of the foundation isolation structure even under strong earthquakes. Bae et al. (2012) have proposed a new TMD consisting of a classical TMD and eddy current damping. The main advantages of this TMD are as follows: (1) it is relatively simple to apply; (2) it does not require any electronic equipment or external power supply; (3) it can effectively suppress the vibration of the primary structure. In all, the theory and research of TMDs have been developed over time. However, due to the narrowband vibration reduction performance and poor robustness of TMDs, it is difficult for TMDs to meet the vibration reduction requirements under complex working conditions.
With the development of the DVA research, increasing researchers begin to focus on the Nonlinear Dynamic Vibration Absorber (NLDVA). Roberson (1952) has indicated that introducing nonlinear stiffness to DVAs is beneficial to expanding the vibration reduction frequency band and enhancing the robustness of DVAs. There are many kinds of NLDVAs, such as cubic stiffness NLDVAs (Oueini et al., 1999), piecewise stiffness NLDVAs (Pun and Liu, 2000) and tuned stiffness NLDVAs (Walsh and Lamancusa, 1992). Nonlinear Energy Sink (NES) is a kind of NLDVA that can make the vibration energy targeted transferred to itself from the primary structure and dissipated by the damping of the NES. NES has been first proposed and named by Vakakis (2001). And the NES enjoys the following characteristics: high energy dissipation efficiency, strong robustness, low mass and insensitivity to stiffness degradation (Zhang et al., 2019; Gourdon et al., 2007; Tripathi et al., 2017; Guo et al., 2015). Thanks to its strong nonlinear stiffness, the NES has no definite initial resonance frequency and can form an infinite number of nonlinear resonance conditions with different primary structures. Therefore, compared to TMDs, NESs have a wider vibration reduction frequency band. Javidialesaadi and Wierschem (2019) have introduced a new NES equipped with an inertial apparatus for passive vibration control of the primary structure and given results related to the performance evaluation of the vibration reduction device. Geng et al. (2021) have proposed a new type of NES with limited vibration amplitude. Adjusting the design parameters of the NES appropriately can effectively reduce the dynamic response of the primary structure, which lays a foundation for the engineering application of the NES. Yao et al. (2019) have designed a grounded NES with segmental linear stiffness for the vibration reduction needs of modern rotating machinery. Simulation results show that the vibration reduction effect of this NES can reach 78%. According to the above references, it is found that the existing NESs have the disadvantages of complex structure, high cost and difficulty in miniaturization. And most of the NLDVAs have not been applied to reality.
In the studies of NLDVAs, the researchers have also paid attention to the DVA with magnetic properties. The nonlinear stiffness of the magnetic DVA is generated by the interaction between magnets (Zhang and Leng, 2020; Zhang et al., 2017, 2020). Compared with NLDVAs constructed from nonmagnetic components, magnetic DVAs greatly reduce the difficulty of obtaining nonlinear stiffness. Moreover, magnetic DVAs are not prone to stiffness degradation because there is no contact between the magnets; therefore, they enjoy stronger stability and longer service life. Pennisi et al. (2018) have implemented the design of an NES with both positive and negative stiffness using some cylindrical permanent magnets and stored the vibration energy through the coil while damping. Benacchio et al. (2016) and Lo Feudo et al. (2019) have designed a magnetic DVA with tunable stiffness using some ring magnet sets and applied it to vibration control of a multistory structure. Chen et al. (2020) have used some rectangular magnets to design a bistable magnetic DVA suitable for vibration control of a multistory structure. Overall, the existing magnetic DVAs usually need a lot of magnets, which makes the structures of the magnetic DVAs complicated. Meanwhile, because of that, the magnetic DVAs, with high installation space requirements, are not conducive to miniaturization. It is difficult for the existing magnetic DVAs to be applied to the vibration reduction of small-sized structures.
Based on the above background and our preliminary work (Chen et al., 2023a, b, c), a novel Triple-magnet Magnetic Dynamic Vibration Absorber (TMDVA) with tunable stiffness is designed, modeled and tested in this paper. The tuning methodology is passive, and it relies on the magnet distance of the TMDVA. The TMDVA is composed of only an acrylic tube and triple cylindrical permanent magnets. Its structure is simpler than that of other existing magnetic DVAs. The TMDVA creates a nonlinear magnetic force with the mutual repulsion between the triple magnets. Due to that, the stiffness characteristics of the nonlinear magnetic force can be changed when the magnet distance of the TMDVA is adjusted. No magnetic DVA with this kind of structural characteristic has been reported so far. A cantilever is taken as the vibration reduction object. And the theoretical model of the TMDVA cantilever vibration reduction system is established. Based on the equivalent magnetizing current theory, a calculation model of the nonlinear magnetic force is derived. Next, the influence of the magnet distance on the nonlinear stiffness characteristics is analyzed. Subsequently, the effect of the magnet distance (nonlinear stiffness characteristics) on the vibration reduction performance of the TMDVA is investigated from the perspective of transient dynamics and energy. After that, experiments are carried out to verify the correctness of the simulation results. Finally, the conclusions are drawn.
2. Theoretical model
2.1 Triple-magnet magnetic dynamic vibration absorber (TMDVA) cantilever vibration reduction system
Figure 1(a) is the schematic diagram of the TMDVA. The TMDVA is composed of triple cylindrical permanent magnets A, B and C and an acrylic tube D. The magnets A and C are fixedly connected to the tube D, and the positions of the two fixed magnets are adjustable. The magnet B repels not only the magnet A but also the magnet C, and can move inside the tube D (the magnetic pole arrangements are shown in Figure 1(a)).
Figure 1(c) shows the equivalent dynamics model of the vibration reduction system. According to Newton’s second law, the dynamics equations of the system can be written as follows:
In the real case, the magnet B is also affected by friction damping (coulomb damping). Therefore, the dynamics Equation (1) needs to be modified:
2.2 Nonlinear magnetic force
2.2.1 Theoretical model
The calculation model of the nonlinear magnetic force
Magnetic induction intensity generated by a permanent magnet in space can be calculated according to Biot Savart’s Law. The magnetic induction intensity generated by a section of the current element at an arbitrary point P in space can be expressed as follows:
In Equation (19),
2.2.2 Nonlinear magnetic force and stiffness characteristics
The parameters of the magnets are shown in Table A1 of Appendix. Figure 5(a) shows the nonlinear magnetic force
To further understand the characteristics of the nonlinear magnetic force
Figure 6 shows the variation of the stiffness coefficients in the nonlinear magnetic force fitting formula when the magnet distance
In Figure 6, when the magnet distance is approximately less than 40 mm, the stiffness coefficients in the magnetic force fitting formula exhibit large variations with the change of the magnet distance. On the contrary, when the magnet distance is approximately larger than 40 mm, the variations of the stiffness coefficients become very small as the magnet distance changes. This indicates that when the magnet distance is small, the adjustment of the magnet distance has a significant effect on the characteristics of the nonlinear magnetic force. When the magnet distance is large, the influence of the magnet distance on the nonlinear magnetic force becomes smaller. From this, changing the magnet distance essentially affects the nonlinear magnetic stiffness. Hence, the change of the magnet distance means the adjustment of the TMDVA’s stiffness.
3. Numerical simulation
In this section, from the perspective of transient dynamics and energy, the influence of the magnet distance change (the adjustment of the magnetic stiffness) on the TMDVA vibration reduction performance is revealed. The parameters of the TMDVA and the cantilever are shown in Table A2 of Appendix. For descriptive convenience, the TMDVA with a magnet distance of 38 mm is named TMDVA-38. And when the magnet distance of the TMDVA is 48 mm, the TMDVA is named TMDVA-48. The amplitude of the acceleration
To evaluate the vibration reduction effect of the TMDVA, the vibration reduction percentage
In order to reveal the energy transfer characteristics of the system, an energy index is introduced as follows:
3.1 The length l E of the cantilever is 92 mm
Figure 7 displays the time-domain waveform and the spectrum of the linear cantilever displacement response when the length
In Figure 8(b) and (d), the displacement of the magnet B is overall higher than that of the cantilever, which demonstrates the targeted transfer of vibration energy to the TMDVA. However, compared with the TMDVA-38 vibration reduction system, the trend of the energy transfer is more pronounced in the TMDVA-48 vibration reduction system, indicating that more energy is dissipated in the TMDVA-48. The percentage of instantaneous total energy carried by the magnet B depicted in Figure 9 illustrates that there are strong energy exchanges between the cantilever and the TMDVA in the initial time period. The characteristics of the energy transfer show that nonlinear beat phenomena occur in both the two vibration reduction systems. Another indication that the nonlinear beating occurs is that the envelope of the magnet B response undergoes large modulations in this case in Figure 8(b) and (d). Figure 9(a) illustrates that the nonlinear beat phenomenon dominates the early regime of the motion in the TMDVA-38 vibration reduction system. However, a less vigorous but faster energy exchange is now observed after 0.5s. Figure 8(b) demonstrates that 1:1 Transient Resonance Capture (1:1TRC) occurs in the TMDVA-38 system (Vakakis et al., 2008). However, Figure 9(b) illustrates that the nonlinear beat phenomenon dominates the entire vibration reduction process of the TMDVA-48 system, and
Figure 10 shows the system Wavelet Transform (WT) spectra, which provide further evidence for the nonlinear beat phenomenon and 1:1 TRC. Figure 10(b) indicates that, in 0
3.2 The length l E of the cantilever is 52 mm
Figure 11 displays the time-domain waveform and the spectrum of the linear cantilever displacement response when the length
Figure 13 shows the percentage of instantaneous total energy carried by the magnet B in the TMDVA. From Figures 12 and 13(b) and (d), it can be seen that the vibration energy has also been targeted transferred to the TMDVA. In the TMDVA-38 vibration reduction system, a nonlinear beat phenomenon dominates the entire vibration reduction process. And the overall trend of
Figure 14 displays the system’s WT spectra when the resonance frequency of the linear cantilever is 25 Hz. Figure 14(b) indicates that 1:1 internal resonance and 3:2 super-harmonic resonance appeared in the TMDVA-38. At the same time, some weak subharmonic resonances also occur in the system. Figure 14(d) illustrates that 1:1 internal resonance and 1:2 subharmonic resonance occurred in the TMDVA-48. However, because the 1:2 subharmonic resonance is much weaker than the 1:1 internal resonance, the manners of energy transfer between the TMDVA-48 and the cantilever are mainly 1:1 internal resonance.
Through the analysis in Section 3.1 and this section, it can be found that the TMDVA can achieve resonance capture with cantilevers with different resonance frequencies. When the magnet distance of the TMDVA changes, the nonlinear magnetic stiffness changes accordingly. Due to this, the TMDVA-38 and the TMDVA-48 exhibit different vibration reduction performances. In general, the minimum magnetic stiffnesses of nonlinear magnetic forces corresponding to different magnet distances are different. For example, the minimum values of nonlinear magnetic stiffnesses with magnet distances of 38 mm and 48 mm are 23.63 N/m and 7.72 N/m, respectively. The nonlinear magnetic force with a magnet distance of 38 mm lacks stiffness components less than 23.63 N/m. And the nonlinear magnetic force with a magnet distance of 48 mm lacks stiffness components less than 7.72 N/m. The absence of low-stiffness components means that the TMDVA cannot form low-frequency resonance conditions with primary structures with lower resonance frequencies. Thus, when the resonance frequency of the primary structure is low, the TMDVA with a too small magnet distance, such as 38 mm, may not be able to achieve 1:1 resonance capture with the primary structure, resulting in a limited vibration reduction effect of the TMDVA. From this, for the primary structures with lower resonance frequencies, the TMDVA-48 may be able to show a better vibration reduction performance because of its larger magnet distance.
3.3 The length l E of the cantilever is 140 mm
In order to verify the correctness of the analysis in Section 3.2, the length of the cantilever is adjusted to 140 mm. Figure 15 shows the time-domain waveform and the spectrum of the linear cantilever displacement response when the length
Figure 18 depicts the system’s WT spectra when the resonance frequency of the linear cantilever is 9.5 Hz. Figure 18(b) shows that the manner of energy exchange between the TMDVA-38 and the cantilever in 0
4. Experiment
In this section, experiments are carried out to verify the correctness of the simulation analysis. First, the nonlinear magnetic force measurement experiments are carried out to check the validity of the
Figure 19(b) depicts the comparison of the experimental and theoretical results of the force
Figure 20 shows the experimental dynamic response measurement system. The excitation signal generated by the signal generator (33500B) is input into the vibrator through the power amplifier (LA-200), and the vibrator (MS-200) excites the TMDVA cantilever vibration reduction system. The acceleration sensor is used for acquiring the excitation acceleration. Then the data can be input into the computer through the signal acquisition device (NI PXI-1033). The sampling frequency of the signal acquisition device is 1.652 kHz. The displacement of the cantilever is measured by the laser displacement sensor (LK-H050), and the data should also be input into the computer. The sampling frequency of the laser displacement sensor is 10 kHz. A triangular pulse signal is generated by the signal generator. The experimentally measured excitation acceleration
Figure 22 displays the comparison between the experimental results and simulation results of the cantilever displacement response when the resonance frequency of the linear cantilever is 16.7 Hz. The vibration reduction effects of the TMDVA-38 and the TMDVA-48 in the experiment are 63.58% and 78.06%, respectively. Direct measurement of the motion states of the magnet B cannot be realized given the existing laboratory conditions. However, it can be seen from Section 3 that the motion state of the magnet B will affect the WT spectrum of the cantilever. Therefore, the WT spectrum of the experimental displacement response of the cantilever can be compared with the WT spectrum in the simulation to indirectly verify the motion state of magnet B. Figure 23 shows the experimental and simulation WT spectra of the cantilever displacement response. Figure 23(b) and (d) demonstrate that both the experimental TMDVA-38 and TMDVA-48 show harmonic components consistent with the simulation results, but the super-harmonic resonances in the experimental results are both weaker compared with the simulation results. Particularly, in the TMDVA-38 cantilever system, the energy transfer between the TMDVA-38 and the cantilever relies almost only on the 1:1 internal resonance. This leads to a lower vibration reduction effect of the TMDVA in the experiment than that of the TMDVA in the simulation.
Figure 24 shows the comparison between the experimental results and simulation results of the cantilever displacement response when the resonance frequency of the linear cantilever is 25 Hz. The vibration reduction effects of the TMDVA-38 and the TMDVA-48 in the experiment are 77.18% and 66.53%, respectively. The vibration reduction effect of the TMDVA-38 is better than that of the TMDVA-48. Figure 25 displays the experimental and simulation WT spectra of the cantilever displacement response. The figure illustrates that harmonic components consistent with the simulation results appear in the experimental results. The experimental results are in general agreement with the simulation results. However, Figure 25(b) demonstrates that some subharmonic components also appear in the experimental results of the TMDVA-38 system, which is not obvious in the simulation results of Figure 25(a). Combined with the WT spectrum of the magnet B in the TMDVA-38 shown in Figure 14(b), it can be found that the subharmonic resonance also appears in the system response of the TMDVA-38 in its simulation analysis. This indicates that the subharmonic resonance appears more strongly in the experimental TMDVA-38 vibration reduction system than in the simulation.
Figure 26 displays the comparison between the experimental results and simulation results of the cantilever displacement response when the resonance frequency of the linear cantilever is 9.5 Hz. The vibration reduction effects of the TMDVA-38 and the TMDVA-48 are 56.25% and 83.03%, respectively. The vibration reduction effect of the TMDVA-48 is better than that of the TMDVA-38 under this condition. Figure 27 depicts the WT spectra of the experimental and simulation displacement response of the cantilever. The figure indicates that when the resonance frequency of the linear cantilever is 9.5 Hz, the harmonic components appear in the experimental results in full agreement with the simulation results.
5. Discussion
Under the parameter conditions of this paper, the simulation and experimental results demonstrate that both the TMDVA-38 and the TMDVA-48 can effectively reduce the vibration of the cantilever, even if the resonance frequency of the cantilever changes. However, the two TMDVAs with different magnet distances show different vibration reduction performances when the resonance frequency of the cantilever is different. To further investigate the law, under the parameters in Appendix, Figure 28 illustrates the vibration reduction effect of the TMDVA-38 and the TMDVA-48 when the cantilever resonance frequency continuously changes. According to the comparison between Figure 28(a) and (b), it is found that the vibration reduction effect of the TMDVA-38 can reach more than 80% in [24 Hz, 30 Hz], while the vibration reduction effect of the TMDVA-48 can reach more than 80% in [9.5 Hz, 21.5 Hz]. And when the frequency is greater than 22 Hz, the vibration reduction effect of the TMDVA-38 is always better than that of the TMDVA-48. On the contrary, when the frequency is less than 22 Hz, the vibration reduction effect of the TMDVA-48 is better than that of the TMDVA-38. Therefore, the TMDVA-38 is more suitable for vibration reduction in the high-frequency region, while the TMDVA-48 exhibits a better vibration reduction performance in the low-frequency region. As previously mentioned in Section 3, the vibration reduction effect of the TMDVA-38 in the low-frequency region (about less than 10 Hz) is not satisfactory due to the absence of low-stiffness components below 23.63 N/m, while the TMDVA-48 achieves more than 80% vibration reduction effect at 9.5 Hz. Figure 28(b) illustrates that the vibration reduction effect of the TMDVA-48 also decreases rapidly when the resonance frequency of the cantilever is further reduced. Near the frequency of 5 Hz, the vibration reduction effect of the TMDVA-48 is reduced to less than 60%.
Figure 29 displays the vibration reduction effect of the TMDVA with different magnet distance when the resonance frequency of the cantilever changes. This figure shows more comprehensively the relationship between the broadband vibration reduction characteristics of the TMDVA and the magnet distance. The figure clearly indicates that when the resonance frequency of the cantilever changes, the vibration reduction effect of the TMDVA can reach more than 80% by adjusting the magnet distance properly. Moreover, under such high vibration reduction effects, the figure illustrates that the magnet distance of the TMDVA and the resonance frequency of the cantilever show an approximately linear relationship. That is, to achieve the optimal vibration reduction effect, the higher the resonance frequency of the cantilever, the smaller the magnet distance of the TMDVA. Similarly, the lower the resonance frequency of the cantilever, the larger the magnet distance of the TMDVA. Therefore, for the vibration reduction of the cantilevers with different resonance frequencies, the approximately linear relationship between the magnet distance and the cantilever resonance frequency provides a convenient way to optimize the vibration reduction effect of the TMDVA.
It should be noted that, from Figure 29, when the resonance frequency of the cantilever is close to 5 Hz and the magnet distance is increased to 60 mm, the vibration reduction effect of the TMDVA still cannot reach more than 80%. Moreover, it can be seen from the trend of the image that even if the magnet distance continues to increase, it is too difficult to make the vibration reduction effect of the TMDVA reach more than 80%. This is due to the fact that the effect of the magnet distance on the nonlinear magnetic force characteristics gradually decreases when the magnet distance is larger than a certain value (see Section 2.2.2).
In addition, Figure 29 also demonstrates that when the cantilever resonance frequencies are 9.5 Hz, 16.7 Hz and 25 Hz, respectively, the vibration effect of the TMDVA with magnet distances of 42 mm
6. Conclusion
A novel TMDVA with tunable stiffness is designed, modeled and tested. The tuning methodology is passive and the adjustment of the TMDVA’s stiffness can be achieved by changing the magnet distance of the TMDVA. With its simple structure, the TMDVA is easy to be implemented and miniaturized. The magnet distance of the TMDVA affects the nonlinear magnetic stiffness characteristics, and ultimately affects the vibration reduction performance of the TMDVA. Therefore, the vibration reduction effect of the TMDVA can be optimized by adjusting the magnet distance. When the resonance frequency of the cantilever is different, the magnet distance of the TMDVA with a high vibration reduction effect shows an approximately linear relationship with the resonance frequency of the cantilever, which is convenient for the design optimization of the TMDVA. Taken together, the TMDVA, with strong robustness, can effectively reduce the vibration of the cantilever even if the resonance frequency of the cantilever changes. The TMDVA has potential application value in the vibration reduction of engineering structures.
Figures
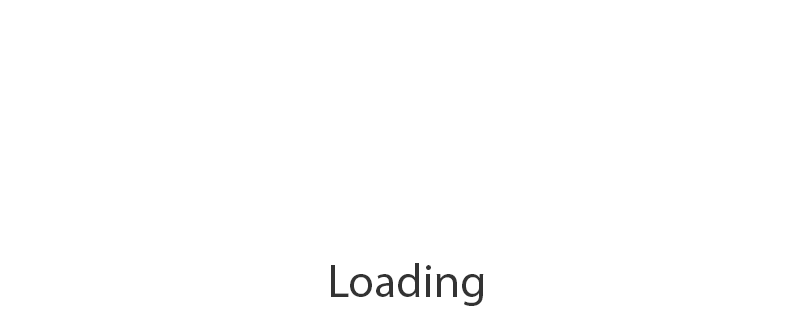
Figure 8
The displacement response time-domain waveforms of (a) the linear cantilever and the TMDVA-38 cantilever, (b) the TMDVA-38 cantilever and the magnet B in the TMDVA-38, (c) the linear cantilever and the TMDVA-48 cantilever and (d) the TMDVA-48 cantilever and the magnet B in the TMDVA-48 when the resonance frequency of the linear cantilever is 16.7 Hz
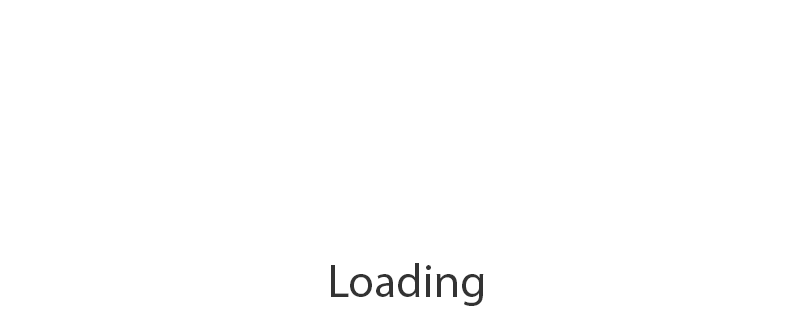
Figure 12
The displacement response time-domain waveforms of (a) the linear cantilever and the TMDVA-38 cantilever, (b) the TMDVA-38 cantilever and the magnet B in the TMDVA-38, (c) the linear cantilever and the TMDVA-48 cantilever and (d) the TMDVA-48 cantilever and the magnet B in the TMDVA-48 when the resonance frequency of the linear cantilever is 25 Hz
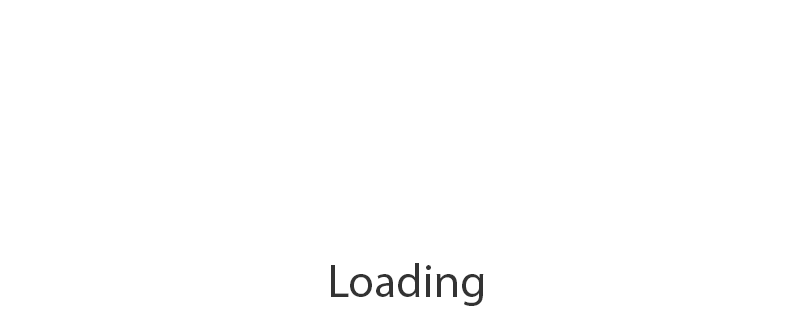
Figure 16
The displacement response time-domain waveforms of (a) the linear cantilever and the TMDVA-38 cantilever, (b) the TMDVA-38 cantilever and the magnet B in the TMDVA-38, (c) the linear cantilever and the TMDVA-48 cantilever and (d) the TMDVA-48 cantilever and the magnet B in the TMDVA-48 when the resonance frequency of the linear cantilever is 9.5 Hz
Parameters of magnets A, B and C
Material | Parameter | Numerical value |
---|---|---|
Magnet B material | Density Height Magnetization | 7,500 9.95 2.985 |
Magnet A and C material | Density Height Magnetization Vacuum permeability | 7,500 4 2.985 |
Source(s): Authors’ own work
Parameters of the cantilever system
Material | Parameter | Numerical value |
---|---|---|
Cantilever beam E: Silicon steel | Young’s modulus Density Length Width Height Damping ratio | 200 7,700 52/92/140 10.02 0.55 0.0021 |
Magnetic suspension tube D: Acrylic plastic | Density Length Inner radius Outer radius Friction coefficient Damping coefficient | 1,200 58 3.05 4.01 0.3 0.02 |
Gripper G: Acrylonitrile Butadiene Styrene copolymers (ABS) | Mass/kg | 0.0029 |
Source(s): Authors’ own work
Funding: This work is supported by the National Natural Science Foundation of China (Grant No. 52275122) and the National Natural Science Foundation of China (Grant No. 12132010).
Author contributions: All authors contributed to the study conception and design. Material preparation, data collection and analysis were performed by Xiaoyu Chen and Yonggang Leng. The experimental structures were made and prepared by Xiaoyu Chen. Fei Sun, Xukun Su, Shuailing Sun and Junjie Xu revised and polished the English writing of the manuscript. All authors read and approved the final manuscript.
Data availability: The data that support the findings of this study are available from the corresponding author upon reasonable request.
Competing interests: We declare that we have no financial and personal relationships with other people or organizations that can inappropriately influence our work, there is no professional or other personal interest of any nature or kind in any product, service and/or company that could be construed as influencing the position presented in, or the review of, the manuscript entitled, “Theoretical and Experimental Study of a Novel Triple-magnet Magnetic Dynamic Vibration Absorber With Tunable Stiffness”.
References
Bae, J.S., Hwang, J.H., Roh, J.H., Kim, J.H., Yi, M.S. and Lim, J.H. (2012), “Vibration suppression of a cantilever beam using magnetically tuned-mass-damper”, Journal of Sound and Vibration, Vol. 331, pp. 5669-5684.
Benacchio, S., Malher, A., Boisson, J. and Touze, C. (2016), “Design of a magnetic vibration absorber with tunable stiffnesses”, Nonlinear Dynamics, Vol. 85, pp. 893-911.
Chen, Y., Qian, Z., Zhao, W. and Chang, C. (2020), “A magnetic Bi-stable nonlinear energy sink for structural seismic control”, Journal of Sound and Vibration, Vol. 473, 115233.
Chen, X., Leng, Y., Sun, F., Su, X., Sun, S. and Xu, J. (2023a), “A novel triple-magnet magnetic suspension dynamic vibration absorber”, Journal of Sound and Vibration, Vol. 546, 117483.
Chen, X., Leng, Y., Sun, F., Su, X., Sun, S. and Xu, J. (2023b), “Design and modeling of a novel triple-magnet magnetic dynamic vibration absorber”, International Journal of Applied Electromagnetics and Mechanics, Vol. 71 No. 4, pp. 363-388.
Chen, X., Leng, Y., Sun, F., Su, X., Sun, S. and Xu, J. (2023c), “Passive vibration reduction performance of a triple-magnet magnetic suspension dynamic vibration absorber under sinusoidal excitation”, Acta Mechanica Sinica, Vol. 39, 522286.
Cheng, Z., Antonio, P., Shi, Z. and Marzani, A. (2020), “Enhanced tuned mass damper using an inertial amplification mechanism”, Journal of Sound and Vibration, Vol. 475, 115267.
Christie, M.D., Sun, S., Deng, L., Ning, D.H., Du, H., Zhang, S.W. and Li, W.H. (2019), “A variable resonance magnetorheological-fluid-based pendulum tuned mass damper for seismic vibration suppression”, Mechanical Systems and Signal Processing, Vol. 116, pp. 530-544.
Den Hartog, J.P. (1947), Mechanical Vibrations, pp. 112-132, McGraw-Hall Book Company, New York.
Di Matteo, A., Masnata, C. and Pirrotta, A. (2019), “Simplified analytical solution for the optimal design of tuned mass damper inerter for base isolated structures”, Mechanical Systems and Signal Processing, Vol. 134, 106337.
Geng, X., Ding, H., Mao, X. and Chen, L. (2021), “Nonlinear energy sink with limited vibration amplitude”, Mechanical Systems and Signal Processing, Vol. 156, 107625.
Gourdon, E., Alexander, N.A., Taylor, C.A., Lamarque, C.H. and Pernot, S. (2007), “Nonlinear energy pumping under transient forcing with strongly nonlinear coupling: theoretical and experimental results”, Journal of Sound and Vibration, Vol. 300, pp. 522-551.
Guo, C., AL-Shudeifat, M.A., Vakakis, A.F., Bergman, L.A., McFarland, D.M. and Yan, J. (2015), “Vibration reduction in unbalanced hollow rotor systems with nonlinear energy sinks”, Nonlinear Dynamics, Vol. 79, pp. 527-538.
Housner, G.W., Bergman, L.A., Caughey, T.K., Chassiakos, A.G., Claus, R.O., Masri, S.F., Skelton, R.E., Soong, T.T., Spencer, B.F. and Yao, J.T.P. (1997), “Structural control: past present, and future”, Journal of Engineering Mechanics ASCE, Vol. 123, pp. 897-971.
Javidialesaadi, A. and Wierschem, N.E. (2019), “An inerter-enhanced nonlinear energy sink”, Mechanical Systems and Signal Processing, Vol. 129, pp. 449-454.
Liu, Y., Yu, D., Zhao, H. and Wen, X. (2007), “Review of passive dynamic vibration absorbers”, Journal of Mechanical Engineering, Vol. 43, pp. 14-21.
Lo Feudo, S., Touzé b, C., Boisson, J. and Cumunel, G. (2019), “Nonlinear magnetic vibration absorber for passive control of a multi–storey structure”, Journal of Sound and Vibration, Vol. 438, pp. 33-53.
Ormondroyd, J. and Den Hartog, J.P. (1928), “The theory of the dynamic vibration absorber”, Journal of Applied Mechanics, Vol. 50, pp. 9-22.
Oueini, S.S., Chin, C.M. and Nayfeh, A.H. (1999), “Dynamics of a cubic nonlinear vibration absorber”, Nonlinear Dyn, Vol. 20, pp. 283-295.
Pennisi, G., Mann, B.P., Naclerio, N., Stephan, C. and Michon, G. (2018), “Design and experimental study of a Nonlinear Energy Sink coupled to an electromagnetic energy harvester”, Journal of Sound and Vibration, Vol. 437, pp. 340-357.
Priya, S., Inman, D.J., Translated by, Huang, J.Q. and Huang, Q.A. (2010), Energy Harvesting Technologies, Southeast University Press, Nanjing, pp. 1-4.
Pun, D. and Liu, Y.B. (2000), “On the design of the piecewise linear vibration absorber”, Nonlinear Dynamics, Vol. 22, pp. 393-413.
Roberson, R.E. (1952), “Synthesis of a nonlinear dynamic vibration absorber”, Journal of the Franklin Institute, Vol. 254, pp. 205-220.
Tripathi, A., Grover, P. and Kalmár-Nagy, T. (2017), “On optimal performance of nonlinear energy sinks in multiple-degree-of-freedom systems”, Journal of Sound and Vibration, Vol. 388, pp. 272-297.
Vakakis, A.F. (2001), “Inducing passive nonlinear energy sinks in vibrating systems”, Journal of Vibration and Acoustics, Vol. 123, pp. 324-332.
Vakakis, A.F., Gendelman, O.V., Bergman, L.A., Mcfarland, D.M., Kerschen, G. and Lee, Y.S. (2008), Nonlinear Targeted Energy Transfer in Mechanical and Structural Systems, Springer-Verlag, New York, pp. 310-336.
Walsh, P.L. and Lamancusa, J.S. (1992), “A variable stiffness vibration absorber for minimization of transient vibrations”, Journal of Sound and Vibration, Vol. 158, pp. 195-211.
Xu, J. (2015), “Advances of research on vibration control”, Chinese Quarterly of Mechanics, Vol. 36, pp. 547-565.
Yao, J.T.P. (1972), “Concept of structural control”, Journal of the Structural Division, Vol. 98, pp. 1567-1574.
Yao, H., Cao, Y., Ding, Z. and Wen, B. (2019), “Using grounded nonlinear energy sinks to suppress lateral vibration in rotor systems”, Mechanical Systems and Signal Processing, Vol. 124, pp. 237-253.
Zhang, Y. and Leng, Y. (2020), “Special behaviors of two interacting permanent magnets with large different sizes”, International Journal of Applied Electromagnetics and Mechanics, Vol. 62, pp. 315-329.
Zhang, Y., Leng, Y., Tan, D., Liu, J. and Fan, S. (2017), “Accurate analysis of magnetic force of bi-stable cantilever vibration energy harvesting system with the theory of magnetizing current”, Acta Physica Sinica, Vol. 66, pp. 154-166.
Zhang, Y., Lu, Y. and Chen, M.L. (2019), “Energy harvesting via nonlinear energy sink for whole - spacecraft”, Science China Technological Sciences, Vol. 62, pp. 1483-1491.
Zhang, Y., Leng, Y., Zhang, H., Su, X., Sun, S., Chen, X. and Xu, J. (2020), “Comparative study on equivalent models calculating magnetic force between permanent magnets”, Journal of Intelligent Manufacturing and Special Equipment, Vol. 1 No. 1, pp. 43-65.